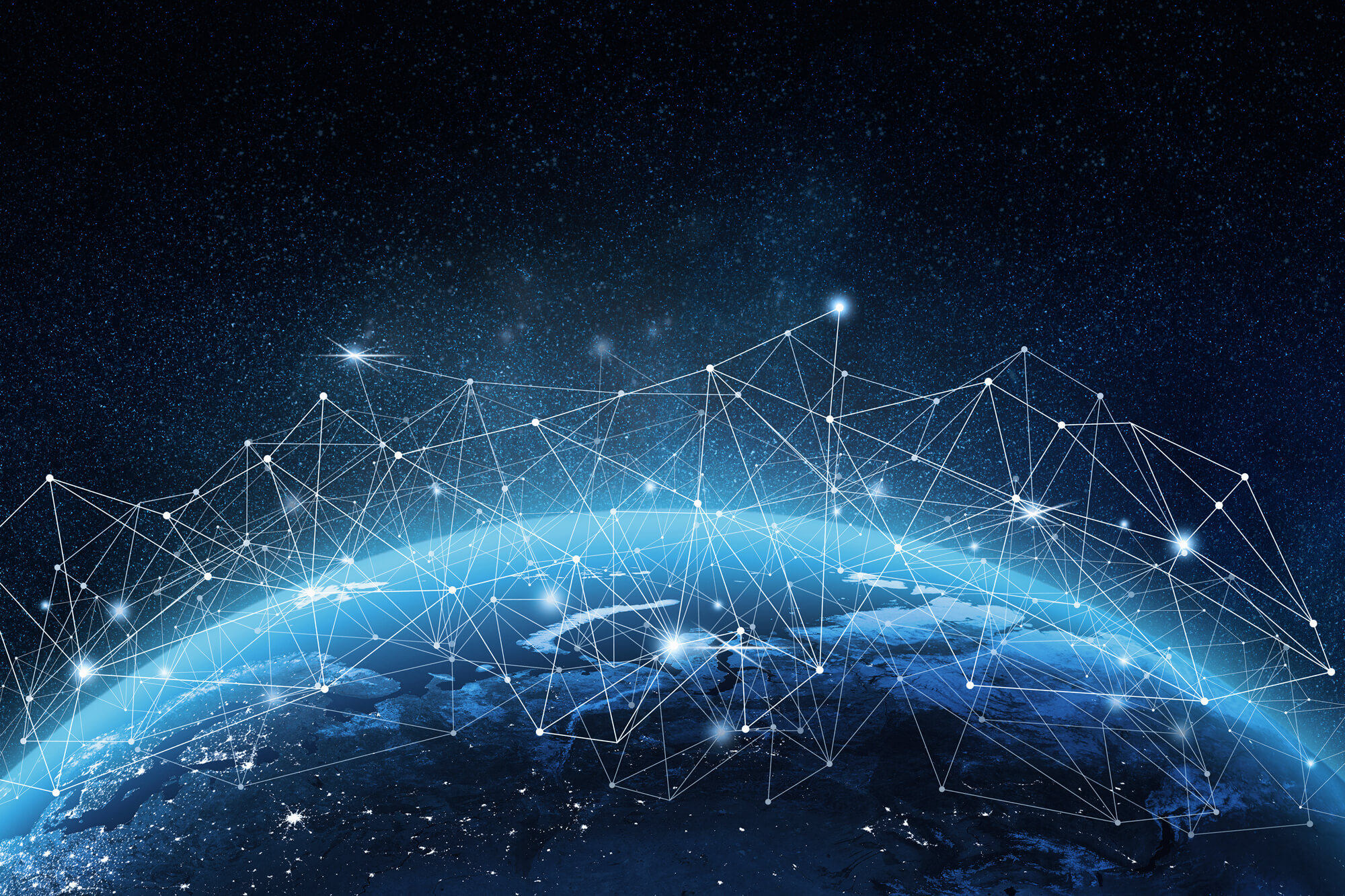
Sustainability update for the global production network
How a supplier company is laying the foundation for achieving its sustainability goals with global standards for sustainable production.
A leading automotive supplier with more than 80,000 employees and production sites around the world has set itself ambitious sustainability targets: By 2030, production - by 2040, the entire supply chain - is to be climate-neutral. The problem is that the existing factories, which will be in operation for at least another 20 to 30 years, are not designed to meet these requirements. In order to make them fit for the sustainability goals they have set themselves, ROI-EFESO is working with the customer to develop a maturity model that provides binding targets for all of the customer's existing and planned plants.
Challenge
In order to achieve the sustainability targets it has set itself, an automotive supplier must optimize its global production network. However, there are no overarching standards for evaluating the status quo and deriving measures.
MOREROI-EFESO approach
Involving all relevant functions, ROI-EFESO works with the customer to develop a common target picture for the plants that takes into account the different perspectives of factory planners and factory operators.
MORELessons learned
A holistic approach that brings together all stakeholders involved or affected by the issue of sustainability from the outset, taking into account the different interests involved, is essential for the operational effectiveness of the initiative.
MOREROI-EFESO success model
A common target picture that provides individual development paths for the sustainable optimization of all global sites is an essential building block for achieving strategic sustainability goals at the customer.
MORELocal targets - global standards
The customer's global production network has grown strongly over the years and now includes more than 70 plants worldwide. Uniform standards for assessing resource consumption and production emissions on site have been lacking until now, as have criteria for sustainable factory planning for new production sites. In addition, many plants are home to different business units, each with very different requirements. A common regulatory framework had to be found for them which, on the one hand, provides binding specifications for achieving the long-term sustainability targets and, on the other hand, takes into account the local requirements and special features of the individual business units.
Overcoming functional silos
As part of a holistic approach that takes into account not only sustainability but also other aspects such as digitalization, operational excellence, factory planning and supply chain management, individual target images were first developed together with the respective functional areas. To this end, the project team worked with the responsible areas to identify existing approaches and best practices in the company and supplemented these with promising future topics. The resulting target images were then superimposed to identify relevant interfaces between the various functional areas. This ensured that topics such as sustainability were not considered in isolation, but in interaction with the other functions. In the case of energy transparency, for example, there are logical interfaces to digital technologies and even links at plant level.
Change of perspective: sustainability from the factory operator's point of view
In order for the optimization levers developed in this way to become operationally effective on site, they then had to be transferred from the functional view into a representation that corresponds to the perspective of both the factory planner and the factory operator. The result: an overall picture of the factory in which the topics from the target picture were re-located and assigned to concrete processes, technologies or behaviors.
"A factory operator doesn't look at sustainability per se, but at processes, technologies or a building envelope."
At the same time, this representation forms the basis for a maturity model for evaluating existing and planning future factories in terms of their sustainability and other criteria. It defines an ideal state from which measures for optimizing the respective factory can be derived. An individual target state can be defined for each factory, depending on the respective requirements and framework conditions on site as well as the specifications of the overarching sustainability strategy.
Lessons Learned: Shared goal alignment as the key to success
Sustainability is not clearly located as a topic in the organization, but is dealt with from various functional areas. A holistic view was missing. A key success factor of the project was therefore to detach sustainability from this isolated view and integrate it into an overall picture of the factory, which on the one hand shows the interrelationships between the different functional areas and on the other hand takes into account the perspective of those who are to implement corresponding measures on site.
At the same time, different mindsets and target perspectives clashed in many areas when it came to sustainability: starting with the functional side, through the various business units, which each have their own requirements for the topic depending on their orientation, to the plants, which view the topic purely from a cost logic. The aim was to bring them all together at an early stage and align them to a common target system. It was crucial to demonstrate the benefits of the measures - not only in monetary terms, as a result of more resource-efficient production processes, but also with regard to aspects such as employee recruitment or employer attractiveness.
Sustainability as a core component of factory planning
Factories that are already in operation today and will be for another 20 to 30 years play a crucial role in reducing CO2 reductions on the way to climate-neutral production. By developing a standardized maturity model that takes sustainability into account in all dimensions of factory planning, the ROI-EFESO project team is providing the basis for a roadmap to upgrade the Group's more than 70 factories and a key building block for achieving strategic sustainability goals.