TOPICS & NEWS
Articles and interviews on current trends, technology and industry challenges, information on our consulting services, seminars and events as well as company topics:
Here you can find out what drives EFESO.
Global Footprint – Revisited
How companies are aligning their existing footprint with what is required
“Things do not change; we change.” The views of Henry David Thoreau, the American essayist, settler and philosopher, would be a thorn in the side of established change management approaches in 2017, which actually regard "things" as being in a state of flux. We acknowledge changes and perform modifications and adjustments as required strictly, and resolutely. Problem identified, problem eliminated. Isn't that all it takes? Maybe not.
Things Change
It's a given. Especially when managing a global value chain. The geographical shift in markets is just as inexorable and under the radar as that of the continental plates. Customers demand that their suppliers have a global presence, and reaffirm this by awarding contracts globally. Competitors change their business models, and new players leverage aggressive pricing to force their way into comfort zones that suddenly become very uncomfortable. Exchange rates respond to real estate bubbles and unstable economies, while impulsive politicians and populist movements spark changes to import, customs and tax regulatory frameworks – or even sudden staggering exits from economic communities. Technological leaps ensure that previously sought-after raw materials and acclaimed top-rank suppliers are suddenly left to gather dust like returned goods on the shelves. As we said before, things change.
We Change
But there's more to it than that. As businesspeople, we choose – thank goodness – to view things from a different perspective – even if, objectively, they remain the same. For example, when our growth strategy proves ineffective and the results are unsatisfactory. Or new markets open up and development and procurement finally think and act globally. Existing assets are also reevaluated when acquisitions are to be integrated, or new products and services rolled out. And last but not least, at some stage comes the point when plant and distribution structures – having evolved over time as well as “legacy burdens” from past relocations – reach a level of hurt which can no longer be ignored.
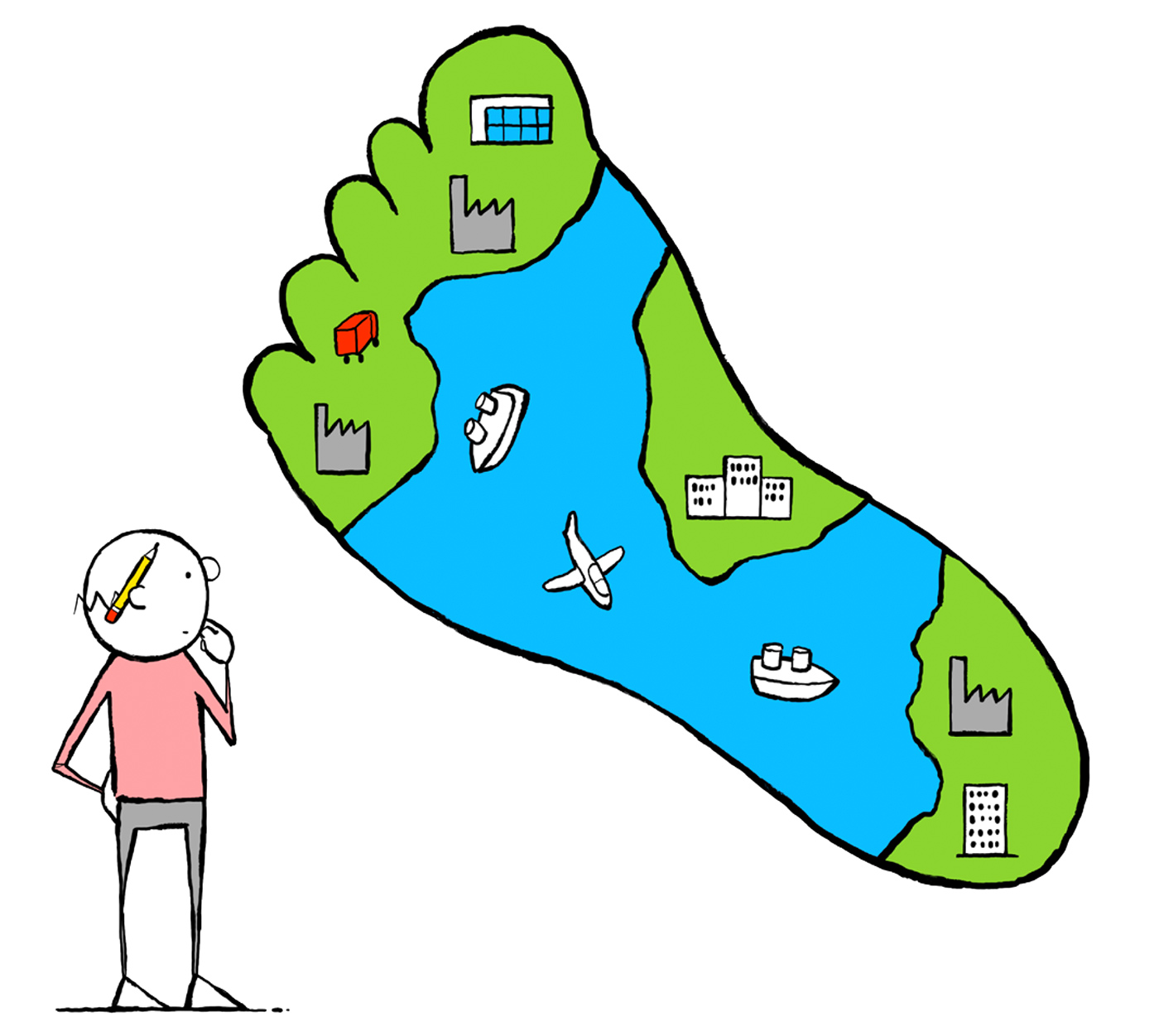
The Roots of the Mismatch
Whether we change ourselves or we change things, ultimately what emerges is a situation where existing and required footprints no longer coincide. This “mismatch” can be analyzed using a number of dimensions.
For example, a company’s competitive position may become imbalanced, as evidenced by e.g. insufficient local presence, over-long or inflexible delivery times, extreme supply chain risks or noticeably increasing price pressure. Alternatively, a structural cost problem is identified due to global overcapacity, an increasing proportion of material costs, high fixed and indirect costs, or exchange rate risks. Awareness that an operating strategy is no longer appropriate or that the necessary transparency can no longer be guaranteed is significantly more complex. This becomes noticeable, for example, when the role of production plants within the network is not clearly defined, when a coordinated investment strategy or general standards and uniform KPIs are lacking, and when gaining an overview of global capacity utilization is impossible.
Few things are as complex, and few changes as risky, as restructuring a global footprint.
At the end of the day, when several such factors coincide and begin to dominate not just the agenda but also management's sleepless nights, that is when it's time to act. This is Easier said than done; however, few things are as complex, and few changes, as risky as restructuring a global footprint. What helps here is an analytically rigorous, implementation-oriented view of the key design features, which can be subdivided into “network configuration” and “network coordination” areas.
Network Configuration
When configuring a global network, four core elements generally stand out: Suppliers, production, the supply chain, and development. Collectively, they are the main variables dictating the shape of the footprint.
When looking at supplier structure, the key levers are striking the right balance between local and global sourcing, global quality and material group management, and the purchasing organization. What counts in production, meanwhile, is the number of sites and role of the plants, looking at capacities and technologies, as well as the production systems. When looking at the supply chain, it is important to scrutinize distribution and service centers, stock optimization, and planning and control aspects.
Finally, in development, it is important to answer questions about how local customization is organized, how prototypes are separated from series production, and how ramping up is organized.
Network Coordination
Network coordination centers on the topics of organization and cooperation. The spotlight in the organizational area goes on questions with special relevance to heterogeneous, distributed structures. How can an effective management system be established? How can we find the right balance between centralization and standardization on the one hand and decentralization on the other? Cooperation and communication within the network are designed in line with these formulated problems – particularly when topics such as best practice sharing, exchanging resources and internal benchmarking are concerned. Last but not least, what counts is supporting the structure with stable and highly efficient IT systems, binding process models and, of course, systematic digitalization.
Achieving a New Global Footprint – Step by Step
Even though the requirements in a footprint project may differ widely, it is still important to try to define standard design guidelines – at least at a strategic level – because if you fail to create “stable, methodological zones”, you will soon end up with a virtually unmanageable children's mobile – a mesh of wires from which whole plants are suspended, rather than toys. It is essential to build on corporate strategy to develop the operational footprint approach, market requirements and the potential of the current structure, and also define future competences, value chains and locations. This is the springboard for developing and assessing alternative scenarios to create a basis for the design phase. The task here is to determine the number, location and role of production plants, perform integrated adjustments to supplier, distribution and service structures, and define the interfaces elsewhere in the company.
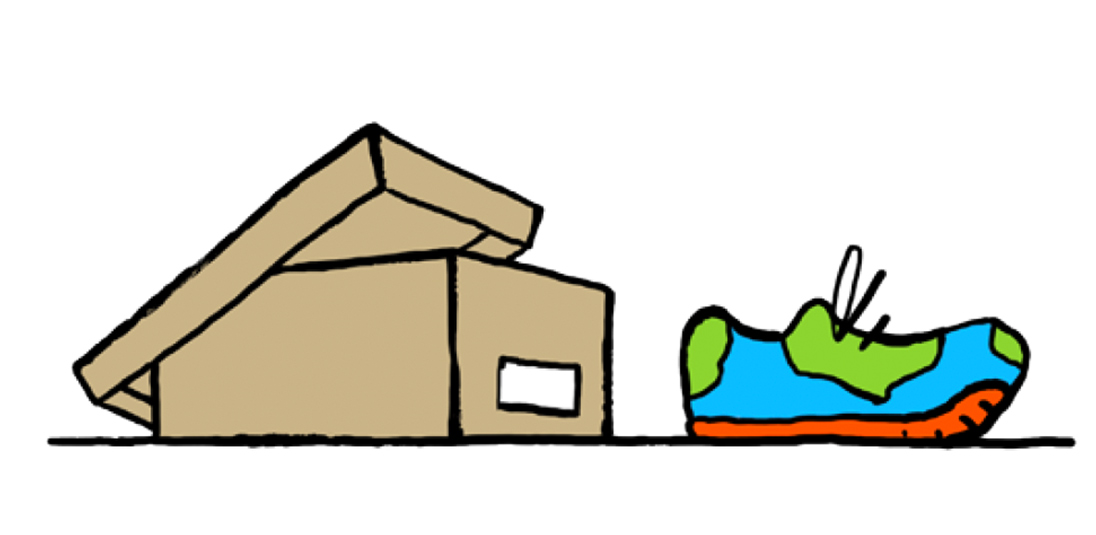
Success Factors
What are the success factors in this complex and thoroughly political process? Based on our project experience, they can be grouped into three categories. First, it is essential to set clear planning guidelines. This is effective when handling critical questions such as plant, for example, plant consolidations, relocations with increases and decreases in headcount, and the promotion of internal competition (or its avoidance!) without the process becoming overloaded with issues that do not belong there.
The second crucial aspect is the methodology and the strong link acknowledged to market and customer requirements, absolute potential benefits system-wide, and a holistic appraisal of the scenario. These include, for example, softer factors such as the long-term nature/resilience of the solution, practicability within the team, and risk potential.
The third and final category is project and change management – an ostensibly soft and often uncomfortable topic that is all too often underestimated, or even deliberately kept under the radar. However, anyone failing to deal sensitively with the fears of the plants and employees and involve the most important stakeholders in the regions will achieve little. Failing to concentrate resources and management attention on the process and/or develop a strong project organization headed by a neutral, globally accepted project leader will leave the processes mired in content-related and political complexity.
Change is one of those things. Changing things alone is not enough; it is also important to motivate and bring the team on board.
If no “stable, methodological zones” are created, you very soon find yourself having to tackle a virtually unmanageable children's mobile.