- Digital transformation can accelerate business processes and thus create competitive advantages. Throughput times from development to production can be reduced by 30%, throughput times in the administrative area by up to 80%.
- Good digitization solutions are roll-out capable and scalable. The complete roll-out for a EFESO Aerospace & Defense customer to several plants took only 2 years.
- Good digitization projects use agile project methods. For example, an engine manufacturer was able to connect entire production lines within two weeks and use the data for digital shop floor management.
- Digitization helps to avoid or automate interfaces. As a result, manual processes can be partially eliminated or transferred to workflows. People only have to make decisions, non value-adding activities are reduced.
- In high-wage countries like Germany, digitization can help to drastically reduce personnel costs. The greatest potential lies in the automation of manual interfaces, the use of RPAs, the integration of development, industrial engineering and production, and the automated creation of complex documents such as assembly instructions and work orders, possibly in combination with the use of new automation solutions such as AGVs, Cobots and intelligent goods provisioning.
Our services for industrial digitalization
The consultants of EFESO are Europe's leading experts for industrial digitalization, Industry 4.0 and Industrial IoT. Our multidisciplinary expertise is based on in-depth technical, methodological and technological know-how as well as access to top benchmarks in digitalization through the presentation of the renowned INDUSTRIE 4.0 AWARD and extensive experience from several hundred projects. In addition, EFESO operates its own learning factories/IoT Fabs and is involved in the committees and associations relevant to the implementation of digitalization, such as BitKom and IIC. Our services for industrial digitalization include the following topics:
- Development and operationalization of the digital strategy
- Maintaining and improving Operational Excellence with AI
- Design and implementation of Smart Factories and Digital Twins
- Implementation of data analytics projects
- IT architecture, IT development planning, platform and system selection
- SAP PROJECT RECOVERY
- Adaptation of the management system
- Extensive training and qualification offers
EFESO process model for industrial digitalization and Industry 4.0
Digital transformation of industrial value creation
The digital factory (Smart Factory) plays a central role in this. It is characterized on the one hand by the comprehensive and consistent use of data, and on the other hand by the use of assistance systems, new manufacturing technologies and flexible automation. The horizontal and vertical integration of the R&D, Engineering, Manufacturing, Supply Chain Management and Customer Management and Future Factory divisions enables highly individual, flexible and efficient production up to the economic production of batch size 1. Global digitalized value-added networks are emerging around the Smart Factory. Integrated digital tools and simulations increase transparency in the supply chain and improve the ability to react to unforeseen events.
Smart products & services
Another important aspect of industrial digitalization is the development of smart products and services to enable and monetize new applications. Through integrated connectivity, sensor technology and data processing capacities, smart products are able to perform tasks autonomously, coordinate centrally and decentrally via cloud platforms and adapt to changing environmental conditions and tasks. Smart products thus also form the basis for the development of smart services such as data-based business models, Smart City, Smart Agriculture or Smart Healthcare.
Digital transformation of the organization
And finally, industrial digitalization means the introduction of new innovation, work and organizational principles such as design sprints, MVPs or crowd innovation into the supply chains of the manufacturing industry and their integration with LEAN principles. On the one hand, this process requires a profound change in the forms of cooperation, culture and organization and the development of new skills and competencies. On the other hand, it requires a consistent further development of the corporate strategy, a high degree of transparency regarding the digital maturity of the company and the definition of implementation-oriented digitalization roadmaps.
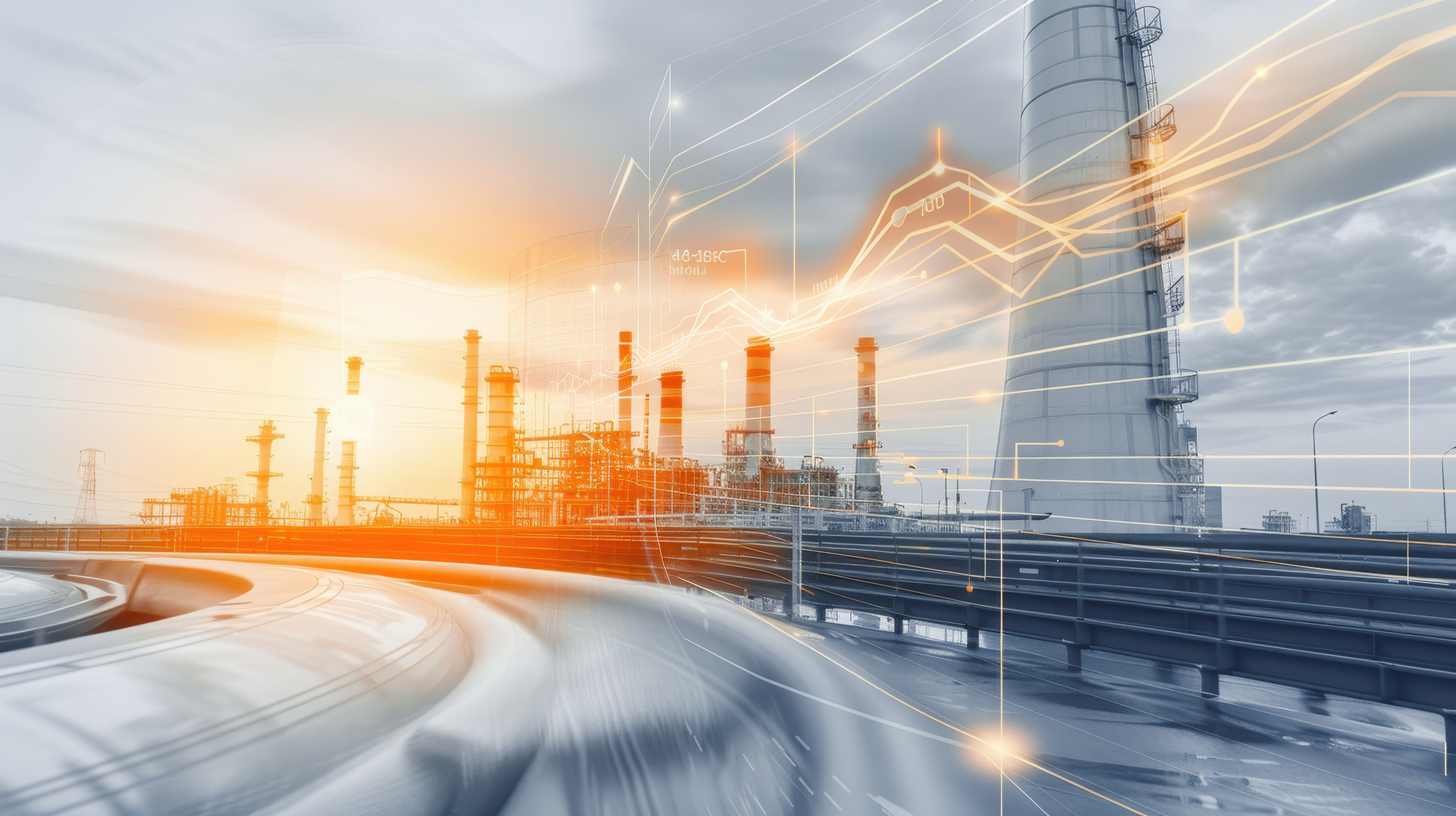
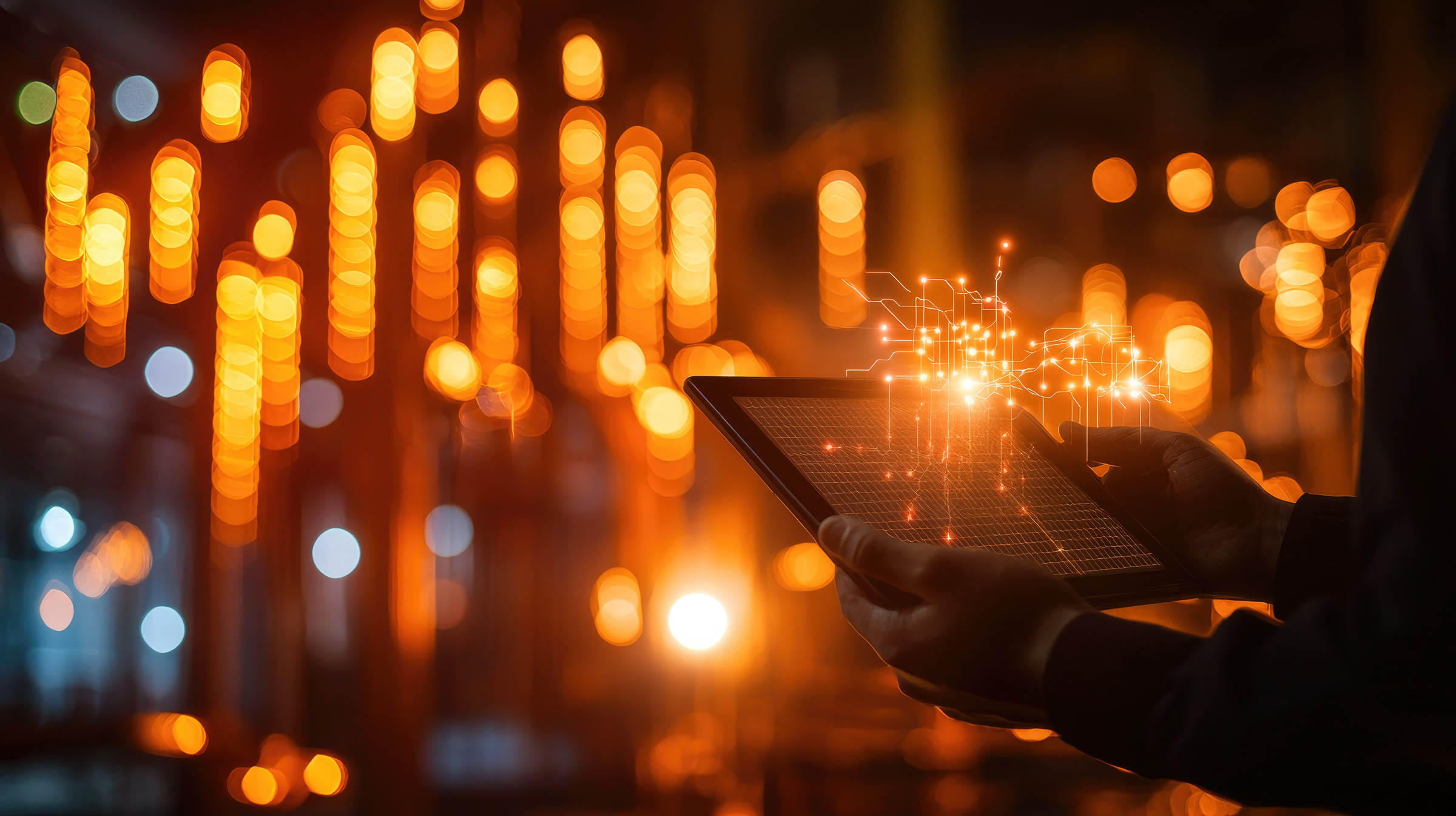
Measurement and evaluation of the digitization maturity levels (IoT Scan) and roadmap
The starting point for a feasible and economical IoT and Industry 4.0 strategy is a complete and objective view of the potentials and implementation hurdles of industrial digitization existing in the company. In practice, it has proven to be a good idea to start with a systematic maturity analysis, as most companies already have a large number of digitisation solutions in place, but these often do not follow a consistent strategy. The method of this IoT scan developed by EFESO consultants ensures transparency and makes it possible to evaluate the initial situation in a structured way, collect ideas and derive approaches for improvement and development. Fields of action are also prioritised and an initial roadmap with concrete implementation measures is drawn up.
Focus on digitalization ROI
Since there are countless technologies and suppliers for every application or task, the management consultancy EFESO's goal is to find the right technologies and solutions to suit the company and its IT infrastructure. The benefit is always in the foreground. Digital transformation, correctly thought and done, always has a positive ROI. Our customers have shown in many projects that efficiency increases of up to 30% through process redesign are realistic and up to 10% through digital support of existing processes.
Digitalization Top Down & Bottom Up
EFESO starts the digital transformation process from two perspectives: Top Down, derived from the corporate strategy and Bottom Up, based on an analysis of the processes, systems & organization to determine the potentials. When evaluating the digital maturity level, we focus on the following dimensions: The processes in production, logistics, quality, maintenance and their mastery, on the IT architecture and on the company organization. All dimensions are systematically examined and fields of action are developed.
The IoT pyramid, which represents successive stages of digitization, also serves as a reference framework for the maturity assessment:
For a single production plant, the complexity of maturity assessment is relatively low and becomes correspondingly more demanding in a supply network and plant group. From all fields of action, those are identified which represent a benefit for the entire company. Instead of "Proof of Concept", it is therefore a question of "Proof of Value".
These fields of action are consolidated and described in solutions (use cases). The requirement for a solution, even if it was developed at one location, is to take into account the requirements of all. Because the real challenge is not to develop a digital solution, but to ensure its scalability.
Scaling digitization successes
The most promising solutions found in this way are transferred into a digital "development plan" with a horizon of typically 5 years and successively detailed and implemented in the plant network.
In order for the industrial digital transformation to succeed, an appropriate organization must be created - here a balance is struck between centralization and decentralization with corresponding degrees of freedom. In order to be able to pick up speed during implementation, not all solutions should be conceived and rolled out in a pilot plant, but rather, when designing the roadmap, it should be ensured that each relevant plant in the network is responsible for certain topics and can develop these for the sister plants.