PRODUCT LIFECYCLE MANAGEMENT CONSULTING
Ensuring long-term competitiveness, profitability and sustainability
Good product development is based on the principles of systems engineering: cross-functional from the outset, with all requirements of the entire product lifecycle taken into account as early as possible. This is based on the "Rule of Ten", according to which change costs increase exponentially throughout the product development process.
In Product Lifecycle Management (PLM), the organizational areas involved are linked in such a way that an overall corporate optimum of sales growth, costs and time-to-market in the Product portfolio is achieved. The central challenges in optimization are:
- Coordinating the responsibilities and work results of the business units involved (shared product responsibility).
- Synchronization of working methods in the relevant functions along the entire product lifecycle, e.g. through simultaneous engineering and advanced quality planning.
- Coordination and consistency of product-relevant information flows and data, e.g. via PDM or PLM systems.
- Coordination of operational information flows, e.g. in project management tools, ERP and ALM systems.
- Transparency and definition of targets for costs and quality features, e.g. failure rates in production due to inappropriate design.
- Efficient adaptation or further development of products in line with market conditions to maximize revenue over the product lifecycle (Total Lifecycle Costing).
Building a cross-functional organization
The business models of many companies are no longer limited to the pure sale of products, but are being expanded to include services such as "product-as-a-service" or usage-based pricing. This trend is due to both the attractive margins of the service business and the need to meet future sustainability requirements, for example in the context of the circular economy.
The leading role in aligning and controlling these aspects falls to product management. It must ensure efficient communication with the market and customers on the one hand and the internal departments involved on the other.
EFESO offers you comprehensive experience in setting up and aligning cross-functional, customer and profitability-oriented organizations.
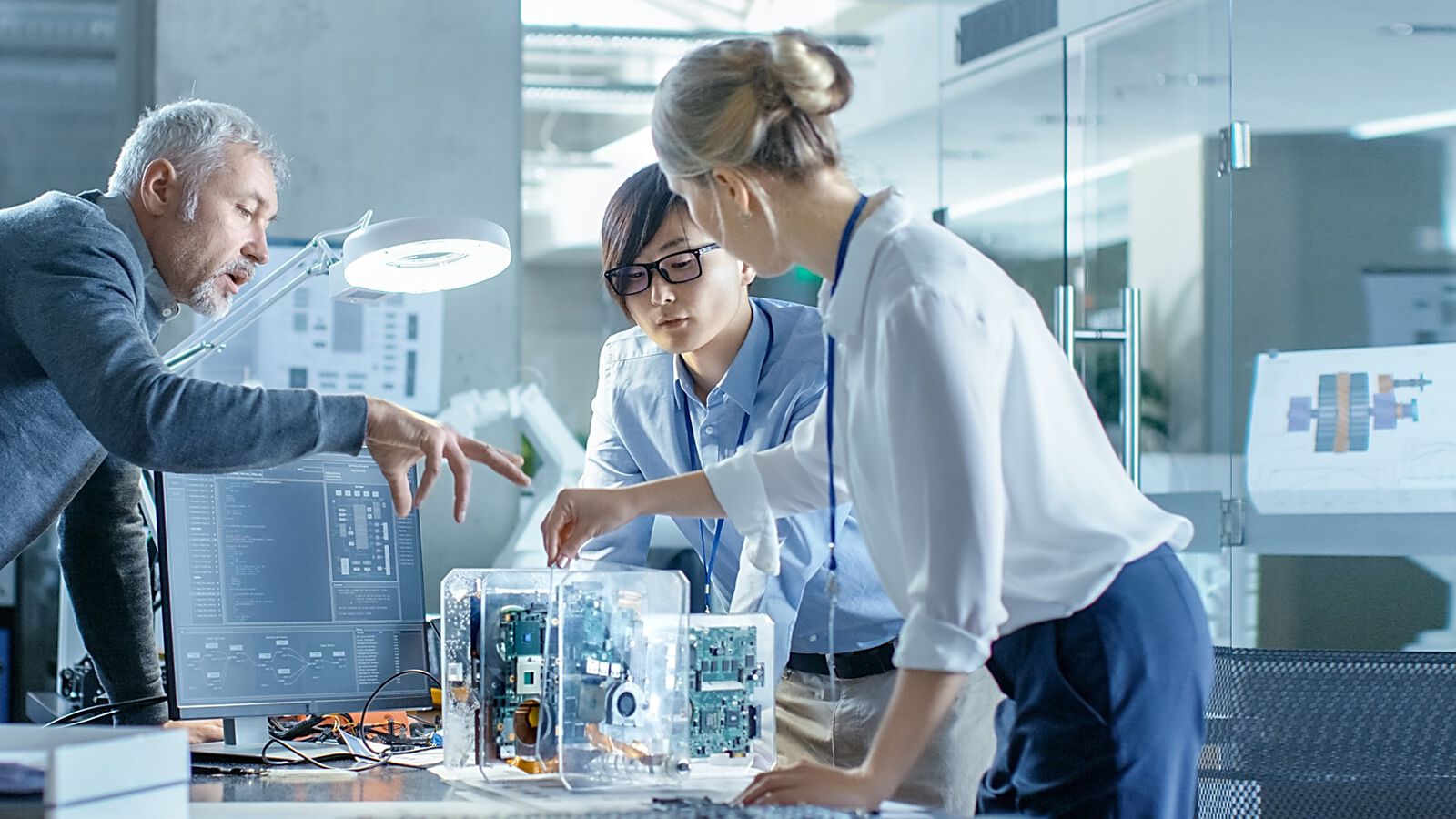
Development model for networked systems
In addition to pure hardware, products increasingly contain software components, which requires specially adapted process models. These bring together the various development cycles and methods in an optimized and coordinated manner - such as the waterfall model for hardware and agile methods for software development.
Most of these products also have data exchange capabilities (connectivity) and thus become "smart products". Hybrid process models alone are then not sufficient to map the increase in complexity in the coordination and optimization of networked systems. A new systematic approach is therefore required to master development projects in this context.
Aligning the development organization with product success
The central feature of this systematic is the connection of the relevant organizational structures as a cross-functionally coordinated development organization geared towards product success. Analogous to organizational networking, the developmental information (data) is intelligently coordinated. This concerns e.g:
- Product structures such as color and material.
- Product data such as specifications, individual features and feature cross-dependencies.
- Customer data such as prices, volumes, country specifics.
- Marketing information such as tutorials for specific areas of application.
- Development data such as eBOM and drawings.
- Production data such as mBOM and work plans.
In addition, life cycle engineering must be integrated as a technical discipline. The starting point are company-wide standardized Life Cycle Assessments (LCA), which can be used to determine TCO evaluations and the CO2 footprint of products and services, among other things. Hotspots in the life cycle must be identified in order to derive constructive solutions with the greatest possible effect as early as possible. This applies in particular to the environmental compatibility and sustainability of products, which must be considered over the entire life cycle.
Creating a consistent product data model
One challenge with this approach is not to introduce separate, locally optimized tools for each organizational unit. Once introduced, these can only be integrated with very large investments and effort, making efficient development more difficult (catchphrase "media discontinuity").
An inconsistent product data model harbors major business risk. For example, there may be difficulties with product approvals. In contrast, intelligent and expandable data models and information architectures enable companies to work efficiently throughout the entire product life cycle.
SysLM as an integrative approach
Against this background, "System Lifecycle Management" (SysLM) offers an integrative approach. In this approach, all components and information are coordinated from the beginning to the end of the life cycle of a product system.
This ensures maximum quality and cost efficiency, particularly in terms of total cost of ownership (TCOQ). In addition, further revenue opportunities can be generated at later points in the life cycle, such as digital twin applications or service-oriented business models.
The consultants at EFESO support you in the design and implementation of holistic lifecycle solutions. Our product lifecycle management service portfolio includes the following services in particular:
- Optimization of product architectures and development of a cross-domain variant system.
- Analysis and design of the necessary organizational and procedural changes, setting up all areas involved.
- Design of collaboration processes and selection of solutions for integration and data exchange.
- Implementation of suitable agile working methods, e.g. agile and hybrid.
- Architecture design, system selection and system integration.
- Selection of platforms for the integration of ALM, PLM, ERP and work systems.
- Introduction of system engineering tools and methods and end-to-end integration into processes and systems.