TOPICS & NEWS
Articles and interviews on current trends, technology and industry challenges, information on our consulting services, seminars and events as well as company topics:
Here you can find out what drives EFESO.
Interview
"AI creates added value as soon as it makes synergy options visible."
Experte: Dr.-Ing. Uwe Steinkötter, Partner, EFESO | 10/31/2024 | Teilen auf in
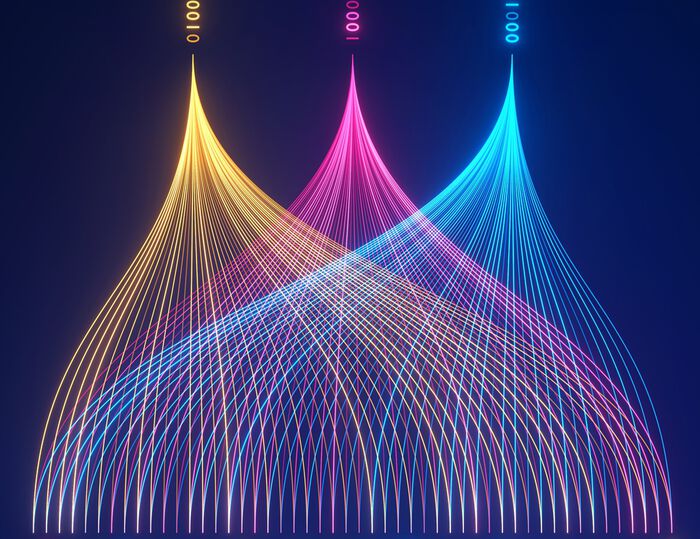
Industrial Recommendation Engine: Using production data properly with AI
Dr. Steinkötter, manufacturing companies sometimes experience their digitalization as a process that is not progressing as quickly as it should. They are already collecting gigantic amounts of data from machines and processes, analyzing, and visualizing complex information such as in shop floor management – but at the same time, they realize that the impact of their IT investments could be much bigger. What's the reason for this situation?
Uwe Steinkötter: Because these steps - collecting, correlating, visualizing, and evaluating data - are not trivial per se and demand a lot from even progressive companies. Nevertheless, this only lays the foundations for playing a part in industrial digitalization. The impression, that investments that have already been made are not exploiting their full potential, can be attributed to two omissions. On the one hand, if the "predetermined breaking point" between strategy and implementation has not been critically scrutinized in digitalization projects, for example with questions like these: How realistic are the KPIs set? What actually happens in the implementation phase if strategy consultants or IT service providers are no longer on board?
On the other hand, industrial digitalization unfolds its potential as soon as advances are made beyond production – first into other direct areas, then indirect areas and, in the long term, even into ecosystems with other companies. In Germany, we are generally confronted with the situation that the IT infrastructures of production are still completely encapsulated from a cloud or other IT environment. Those who still use production computers with Windows XP, for example, and are concerned with the data protection guidelines for cloud computing, usually do not want to establish one-to-one connections. And when working out the alternatives, you should again be able to answer the questions just mentioned. However, with the addition that IT security investments pay off if certain situations do not occur. This must therefore be considered separately from the classic OEE, cycle time and efficiency issues.
Now, however, we are also seeing how Artificial Intelligence (AI) is redefining the technological framework for industrial digitalization. How do you assess this development?
US: There is no way around the use of AI for the industry – but AI does not solve problems by "plug & play". The strengths of AI today lie in its ability to evaluate a wide range of different information and simulate process alternatives, i.e. to provide an overall picture of the options for action in a manufacturing as well as in other operations areas.
The mandatory prerequisite for this is information that is collected by employees according to specifications for the IT/OT architecture and the required data. However, such an idea, such a "data picture" does not yet exist in many companies. Instead, decisions are made on a case-by-case basis, for example when a pilot project gets out of hand and the planned investment is questioned after a short time. Such pilot projects often start with systems or machines, whose specifications and topics the employees are already very familiar with – this is useful for data collection, but in the "data picture" it is just one "color" among others.
What do you recommend instead?
US: Direct work on the machine remains decoupled from the cloud in terms of data. The evaluations of performance, operating states, etc. are carried out on the shop floor, transferred to the cloud, and reflected back to the machine with a certain delay in order to make decisions. You should already have the topics or subdivide evaluations according to "real-time, near real-time, long-term". Anyone who has implemented this not just for one pilot, but for all particularly relevant machines, comes a big step closer to realizing the data picture of their production.
The right choice of time period is important here: this opens up different options to intervene in the process promptly or to control or optimize it. The costs for the evaluation speed in the cloud must also be taken into account. Some decisions, such as changing filters or tools in the systems, have a certain lead time and therefore do not have to be made in real time or near real time – which means that costs can be saved in cloud computing.
AI does not solve problems by "plug & play".
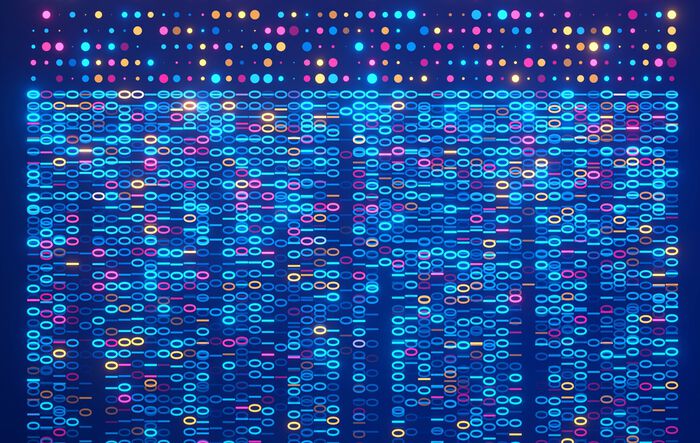
At what point should investments in AI technologies prove useful?
US: In my experience, tangible benefits arise when - in addition to humans - an AI "observes" the mentioned data image of the various machines in the entire production process. AI creates added value here as soon as it makes synergy options visible that were not perceived on the individual machine. And which even an employee with their experience cannot see, as they do not even know what happened in the previous process steps. These AI-relevant aspects - monitoring, simulating, forecasting, making recommendations for action - require the evaluation of a holistic system.
Are there any other requirements for the use of AI?
US: The IoT infrastructure may need to be expanded to collect additional data. Depending on the field of application, with sensor technology for relevant measured values or tracking technology for setting up digital process twins in production and supply chains, for example. The common denominator is to bring all this data into a standardized data pool. With this database, it is worth creating two variants of the evaluation: one with a knowledge logic, i.e. by a data analyst - and also free of specifications, such as pattern detection via Power BI. In this way, you gain many, often completely new insights.
However, this also requires a certain level of maturity in terms of basic knowledge, which varies depending on the manufacturing context. Essentially, it is about creating a digital product twin - what was manufactured on which machine at what time? Where is which product or component located in internal or external logistics? Ultimately, it should be possible to clearly assign the product so that the AI can effectively support process control.
Discuss with Dr.-Ing. Uwe Steinkötter on how to drive digitization in your company in a results-oriented way.
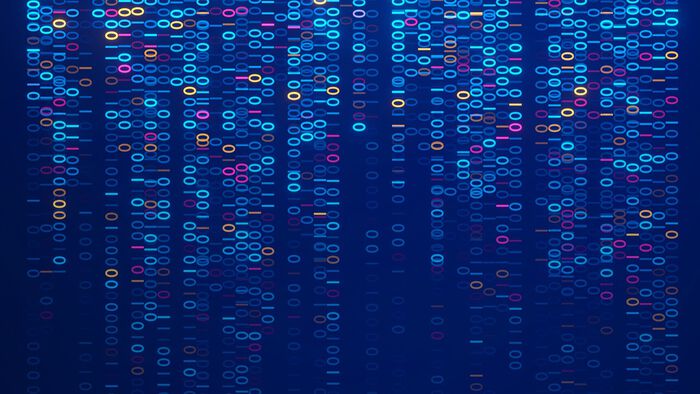
In the future, AI will not only be able to monitor and warn, but also proactively recommend actions. Such "Recommendation Engines" present today personalized products and topics on web portals and social networks that they derive from our online behavior. How can companies build an "Industrial Recommendation Engine"?
US: That depends, first of all, on whether you operate a mass production – or highly specialized in batch size 1 or in very small quantities. In the first case, the "Industrial Recommendation Engine" is trained in advance with data and parameters from production, so it learns independently based on this information. Mostly, these are use cases on classic topics such as quality control and error detection. So, the system learns at first, what is a fault or a "good part" and a "bad part", often using image recognition software.
By the way, we have found that AI can adapt human logic in such a learning process: if the training images were marked with the symbols "thumbs up" and "thumbs down", the AI only paid attention to these parameters after a short time – after all, it was trained to do so from its "point of view". In this case, well-considered training rules are therefore important. We also need a large number of operations in order to obtain a bad part from the process in the first place and then to be able to establish a correlation with the previous process steps. In a well-organized production facility, we are talking about 1-3ppm, i.e. one to three bad parts per million parts in total.
However, this statistical mass is not available for make-to-order production ...
US: Correct, for small quantities such as in plant production, AI is trained using other parameters. Here, it tends to identify errors in the setup processes, missing or incorrect tools and materials or assembly errors in the product. The development of an "Industrial Recommendation Engine" therefore refers more to an assisting control and recommendation function that facilitates and secures the work process. Of course, product parameters such as weld seams could also be photographed in this case and used as a database to reduce errors in AI training. However, this database should be enriched and compared with generic welding data or data from machine manufacturers for better classification.
The use of AI may address economic KPIs, but it will also influence the development of the company's organization and culture. What experiences and recommendations from best practice projects can you share?
US: Expectation management is always an important topic – as mentioned, AI rarely cures problems in a quick fix. In our digitalization projects, we therefore present realistic, case-related perspectives for AI and all other technologies. In doing so, we find out exactly which technology makes the most sense for which application. In AI applications, the topic of "decision-making power" is also becoming more common. This usually remains with the employee, but thanks to AI, they make these decisions based on a larger database and better forecasting accuracy. AI is therefore currently in the role of assistant and is likely to remain there for years to come.
However, the change aspect of the topic is actually very important. If AI as an assistant enables more and more employees to make more and more decisions, this changes the understanding and tasks of leadership enormously. For example, regarding to the shorter time cycles: if AI makes information available much more quickly, more decisions have to be delegated to lower levels. A few control meetings with the management level can quickly become a thing of the past if machine setters and operators have all the relevant data directly at their disposal and decision-making authority is gradually shifted. Best practice companies solve this with the appropriate skills to "let go" from one direction – and to be able to accept and take on this role from the other.
Find out more about solutions for industrial digitalization
Digitalization, Industry 4.0 and IIOT >
Digitalization as a performance driver >
![]() |
Thank you for Signing Up |

