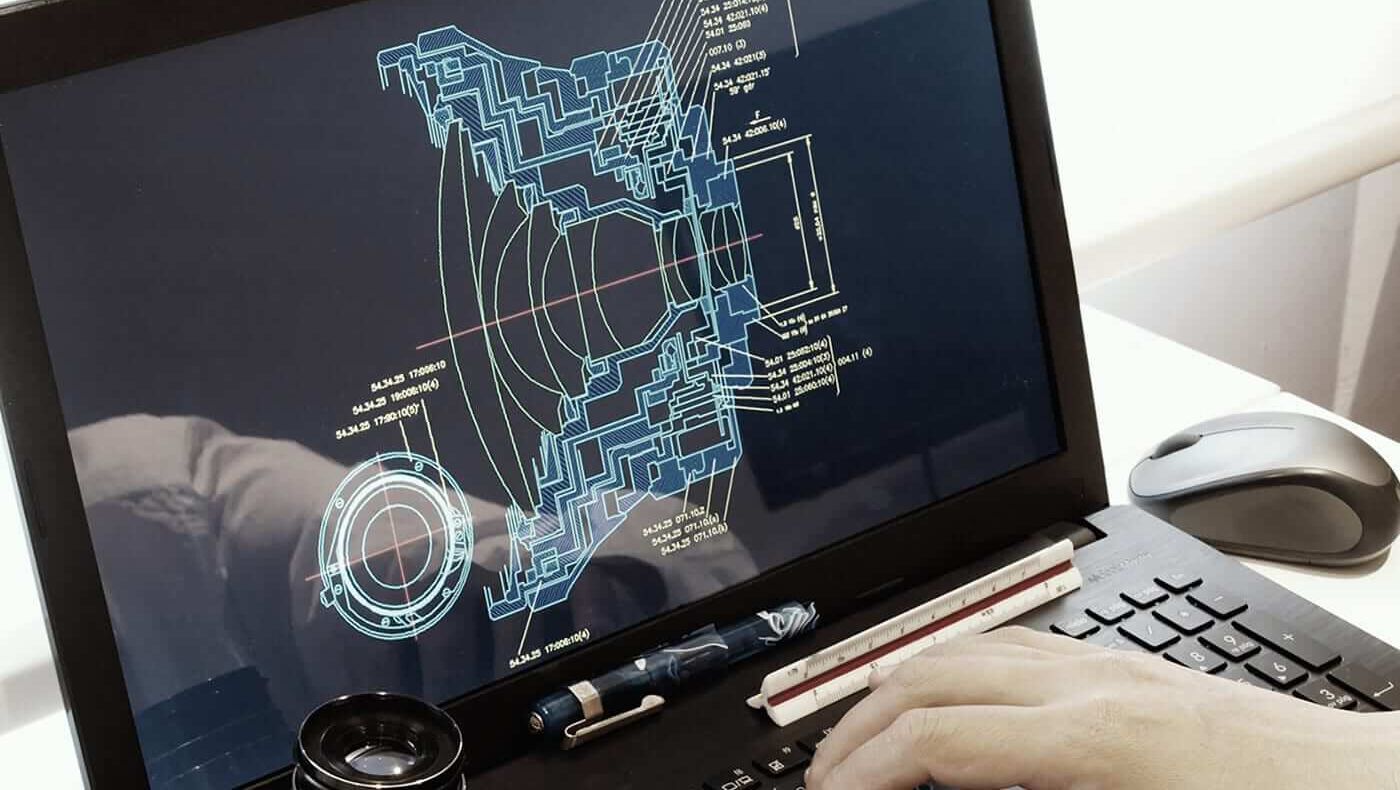
Digital Process Twin: Process optimization through Predictive Quality and Predictive Production
Virtual cockpit for value stream management
When it came to improving a production plant for dashboards, an automotive supplier faced two challenges: the entire process chain – together with all risk factors in production and supplier management – had to become more transparent. At the same time, even small errors in the manufacturing process led to the rejection of complete components, since a sensitive material was being processed – this scrap rate had to be reduced. Together with EFESO, the company was able to map the entire production process step by step using a ‘digital twin'’. This resulted in an IoT pilot which identifies potential for improvement and triggers improvements in both manufacturing and value stream management at suppliers.
Challenge
One automotive supplier improved the transparency of work and organisational processes in its manufacturing plant for dashboards. The task was to identify and eliminate errors and efficiency losses with a high number of variants and at high speed.
MOREEFESO approach
With its ‘Digital Process Twin’, EFESO not only reduced the reject rate, but also made parameters in production and beyond more transparent in the company’s value-added networks, which in turn influences earnings.
MORELessons learned
Virtual process twins not only contribute to increasing efficiency and quality but are also an important strategic factor in the development of a smart supply chain management.
MOREWith a variety of variants of up to 600 series and individual cockpits, the company manufactures several thousand cockpits every day. Different surface concepts additionally increase the number and complexity of the process steps, such as injection moulding, foaming, punching, welding and assembly. In the foaming process alone, more than 1,000 parts are produced per shift with a cycle time of less than one minute. This leaves little scope to define the benchmark in terms of costs, quality and delivery capability, to ensure the transfer to external suppliers and to initiate process improvements.
High scrap rate and efficiency losses
The particular challenge in this case was the frequent use of polyurethane foam, i.e. for mouldings and hardening. This usually involves a significant scrap rate, especially due to the very high industry standards. However, most of the errors and efficiency losses are not due to the material but rather the work processes: up to 60 robot arms work on the individual production steps of a single cockpit. After cooling down, the lightweight carrier of the cockpit is connected to the cockpit skin that is visible later. This is done on a carousel-like apparatus, the foam rotary table. On this rotary table element, 14 tools are available, which are equipped on two levels. Ten tools are in operation at the same time. Together with EFESO, the automotive supplier took a very close look at this manufacturing segment.
Focus on performance and quality
As a starting point, the project team defined process parameters, which can influence both the performance of the plant and the quality result. The derivation of these values was based on experience and initially covered well over a hundred different parameters, which were reduced or supplemented over the further course of the analysis. In the next step, the project team made sure that the existing process data was correctly aggregated and processed and collected data that had not been previously recorded. The team also used additional sensors to acquire the new data required for the defined parameters.
Digital Process Twin by EFESO
The data base thus generated was then merged in a cloud application and analysed. On this basis, the project team developed a model that mapped the process of improving the production line for dashboards as precisely as possible – i.e. all relevant parameters, their interactions and critical values. Like the process itself, this model can also extend far beyond the company itself. In the case described, for example, as far as the logistics company that transports the foam or even to the foam manufacturer. This is because the causes of problems in the foaming process – such as temperature fluctuations that are dangerous for the sensitive polyurethane – can occur at any point in the value chain. As a result, the company ended up with a digital process map that monitors the entire physical process in real time and allows early intervention based on critical process parameters – a ‘Digital Process Twin’.
Precise check of value creation networks
With the help of this ‘digital twin’, the project team was not only able to significantly reduce the reject rate of the plant, but also to make the correlations of relevant influencing factors on the quality result more transparent. The company also developed a prediction model of the result at the next quality gate.
In addition, EFESO’s ‘Digital Process Twin’ offers completely new options in value stream management, for example in the evaluation, control and qualification of suppliers. By using the virtual process model, the actual structures and processes in value creation networks can be analysed much more precisely and profoundly than with today’s checklists and lean manuals. On the one hand, this provided the company an excellent tool for qualifying its suppliers. On the other hand, it can now integrate new partners much faster and easier, reducing dependencies and facilitating the construction of new local production sites. This makes virtual process twins an eminently strategic factor in the development of smart supply chain management.