“For a long time, sustainability was more an accidental by-product”
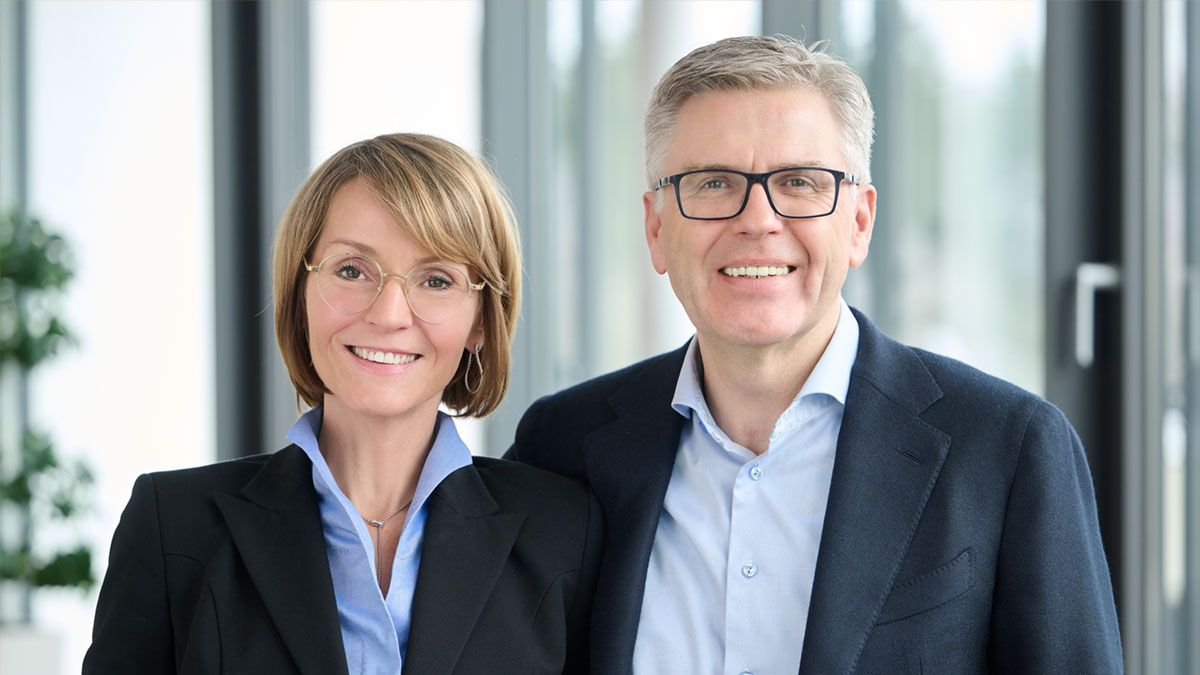
Industrial Sustainability is created at the point where sustainability, innovation and process excellence intersect. Few products embody this principle as well as the screw compactors manufactured and sold worldwide by H&G Systems.
These waste disposal solutions, which come from a medium-sized company based in the Siegerland region of Germany, enable the compaction of large-volume waste and recyclable materials, handling anything from plastic and composite materials to cardboard boxes and Euro pallets.
Thanks to their electromechanical direct drive systems and effective screw shape, designed to break down materials while generating a constant forward motion, the products achieve significantly higher throughput rates and filling weights than conventional hydraulic pressing systems. As a result of their superior compaction, denser load weights can be achieved, allowing more efficient shipping and enabling CO2 savings of up to 50%.
At the same time, the H&G Group itself is a shining example of corporate sustainability. A family-owned and managed business, this technology and market leader supplies products worldwide to customers from its headquarters in Burbach, helping to control the rising global tide of waste and recyclable materials in logistics and trade.
Interview with Alexandra and Bernd Henrich, Managing Directors of H&G Entsorgungssysteme GmbH
DIALOG: Your innovative screw compactor promises reductions of up to 50% in CO2 compared to conventional disposal solutions. What role does such a sustainability benefit play in the eyes of your customers?
BH: I think the perspective on this has changed a lot. When we started developing the screw compactor back in the 1990s, the initial focus was on very specific questions of process efficiency: how can you organize the disposal of cardboard boxes without having refuse trucks blocking the loading ramp twice a day? How can the number of trips be reduced by increasing transport load weights?
Of course, even then, this had an impact on reducing CO2 emissions - but the focus mainly was on optimizing operational processes and disposal costs. Sustainability was an accidental by-product, so to speak. Since then, we have seen this aspect increasingly coming to the fore, because companies are taking a closer look at their own CO2 footprints: they are actively looking for easy wins, areas where they can make their processes more sustainable and resource-efficient.
DIALOG: Has this stronger focus on sustainability at your customers also changed your own processes?
BH: Yes, quite significantly. Today, we are in a position to offer our products on a climate-neutral basis. In order to be able to justify that claim, we determined our own carbon footprint and have since been working continuously to make our value creation processes largely climate neutral.
As far as production is concerned, this initially comes down to the type of energy supply used: with a combination of photovoltaics and a combined heat and power plant, we now generate 60 percent of our energy requirements from renewable sources. And what electricity we can’t generate now comes from ‘green’ renewable energy sources, too.
In addition, we are constantly trying to reduce the wastage of resources in a multitude of areas. A good example is our recent investment in two new paint shops, both of which have heat recovery, which reduces paint wastage, as well as energy consumption.
DIALOG: Most CO2 emissions occur in the supply chain. Steel in particular, as an essential component of your products, is a very climate-intensive material. What does that mean for your supply chain management?
BH: Yes, steel is a raw material whose production releases large quantities of CO2. New process methods for CO2-neutral steel production using green hydrogen could change that one day but they are still several years away. Until then, we are relying on CO2-reduced steels and working to optimize our supply chain footprint. We do this by purchasing the materials we need to manufacture our machines in Europe, wherever possible, and also have the mechanical processing carried out in the region, too, where we can. Unfortunately, this is not always that easy, as many steel mills have downsized their portfolios in recent years.
AH: We rely heavily on our partners to make our supply chain sustainable. This also applies when it comes to the issue of transparency. In order to be able to reliably report the footprint of our machines, we have to hold our suppliers and upstream suppliers accountable for proving what the carbon footprint of their supplied materials and components are, before we install them in our machines. These are things that we are constantly examining as part of our overall sustainability strategy.
DIALOG: The H&G Group is an family owned and managed business. How does that shape your view of sustainability?
AH: For us, sustainable entrepreneurship means working responsibly with the resources that are available to us. This applies both to the investments we make and to the natural resources we consume. But above all, it applies to the people who live and work here in the region.
DIALOG: What role do these regional roots play for you, in terms of sustainability?
BH: Our connection to the location and the region determines our actions in many respects. For us, the preservation and further enhancement of the location always take top priority.
With more than 150 employees working in our company, we supply more than 35 countries, spread across the globe, from here. We very much see ourselves as part of the community and are actively involved - whether that be in the local sports club or with local fire department - and want to offer the people here a lasting, stable perspective. That certainly sets us apart from one or two other large corporations.
At the same time, our location also regulates our actions. Because the company was founded 60 years ago on open countryside, we now find ourselves bordering a landscape conservation area and so are always looking for ways to reconcile our growth with the need to conserve nature. For me, dealing with these framework conditions and their interactions forms the core of sustainable entrepreneurship. And so far, I think we’ve done pretty well.