Low Impact Operations
Operational processes in manufacturing and the supply chain offer numerous starting points for decarbonization and reducing the consumption of raw materials and energy. As such, they can make a significant contribution to achieving companies' sustainability goals and meeting legal requirements.
Promising opportunities for improvement arise above all from the design of the manufacturing footprint, from lean processes geared to avoiding waste, and from the digitization of physical processes.
Increase resource productivity in the value chain
EFESO Management Consulting supports companies in a future-oriented, holistic view and alignment of manufacturing and supply chain networks. With our Sustainable Value Creation approach, our customers define sustainability goals and optimize their use of resources in all segments of the value chain.
We offer the following services for the establishment and further development of "Low Impact Factories" and "Low Impact Supply Chains":
Improving manufacturing and logistics processes
How can the utilization of plants, machines and means of transport be increased in order to reduce or avoid emissions and environmental pollution? We develop pragmatic solutions for sustainability-oriented process optimization, using methods and technologies such as TQM, Industry 4.0, advanced analytics or KI.
Measuring and improving sustainability performance
We make sustainability potentials transparent by means of data acquisition and visualization and create the necessary foundation with MES, ERP, EMS systems. We also implement IoT platforms with analytics functionalities, energy-adaptive PPS systems and other systems for comprehensive optimization of production.
Sustainability assessment of the manufacturing footprint
We use technical energy audits and process analyses to determine the sustainability maturity level of the manufacturing footprint. We also provide support in auditing and developing the supplier network to meet sustainability requirements.
Using life cycle analyses for decision-making
Does installing a photovoltaic system on the factory roof bring the optimal "green ROI"? Or are better results achievable if the company car fleet and all vans at the site are "electrified" instead? More interesting questions that involve a high degree of complexity in implementation are answered with the help of life cycle analyses. These quantify, for example, the impact of the measures on CO2 emissions over the next ten years and thus enable rapid decision-making for the ultimately more suitable measure.
Linking digitization and sustainability initiatives
Companies should use existing digitization projects and initiatives to make the current consumption values and process flows of each machine transparent, for example - and improve them from a sustainability perspective.
Systematics and success factors of a "Low Impact Factory "
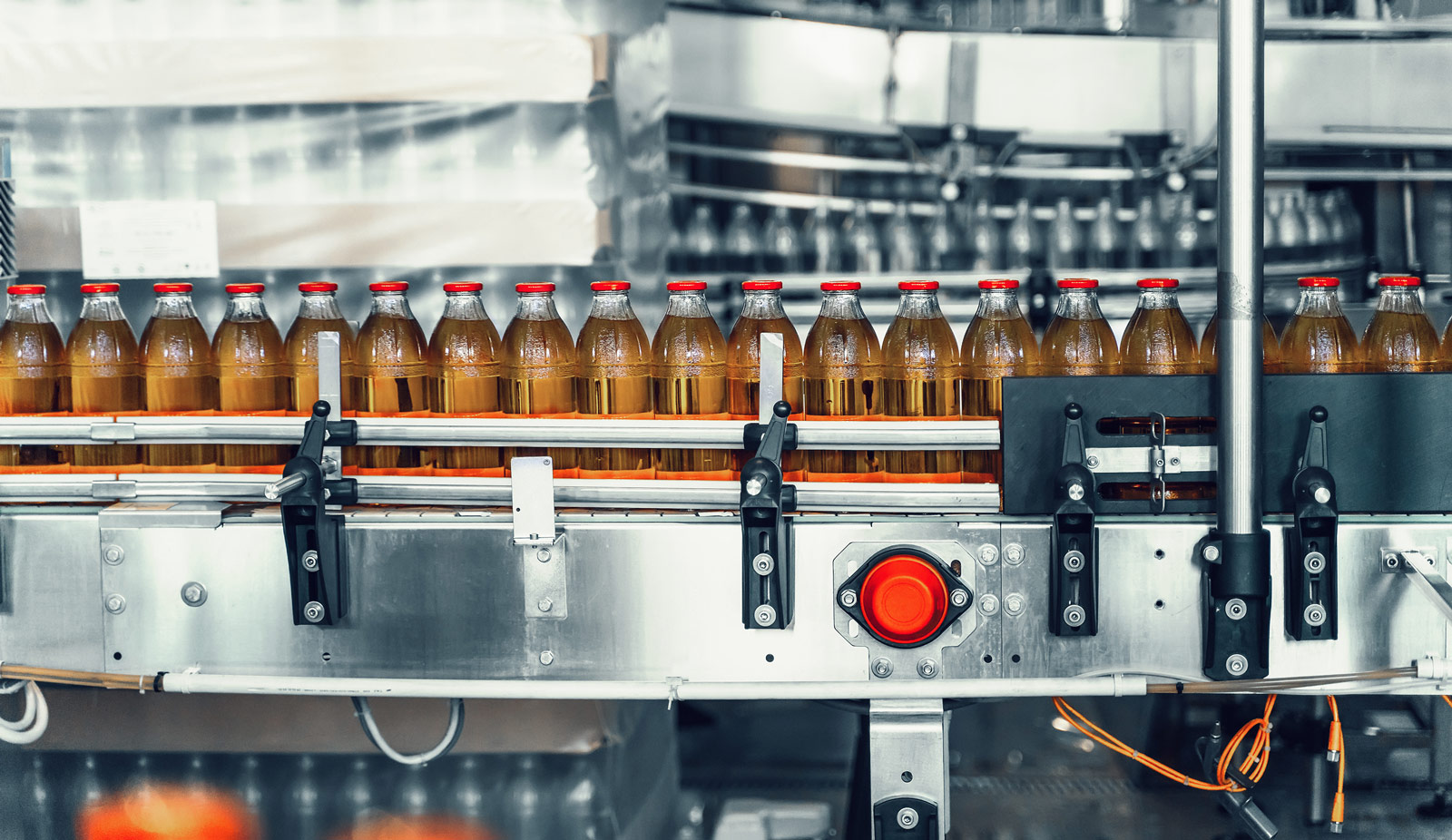
Projekt: Programme to reduce energy losses and reduce the amount of waste.
Ergebnis: Up to 20% energy saving.
Systematization of sustainability management
Which sustainability fields of action should be prioritized in the operations area? What needs to be considered when developing sustainability initiatives and target systems, and how can these be embedded in the overarching corporate strategy? We help to solve these challenges as well as to integrate sustainability goals into investment planning and management systems and reporting.
Balancing emissions
We show companies how to define realistic emission reduction targets, develop compensation strategies and use the right measures to achieve a balanced emissions balance. In doing so, we take into account industry-specific compliance requirements as well as international and national legal requirements.
Optimization of the entire value cycle
Avoiding the Waste of raw materials and energy plays just as important a role in this point as the use of renewable energies. We support with appropriate measures and show how closed raw material cycles are created.
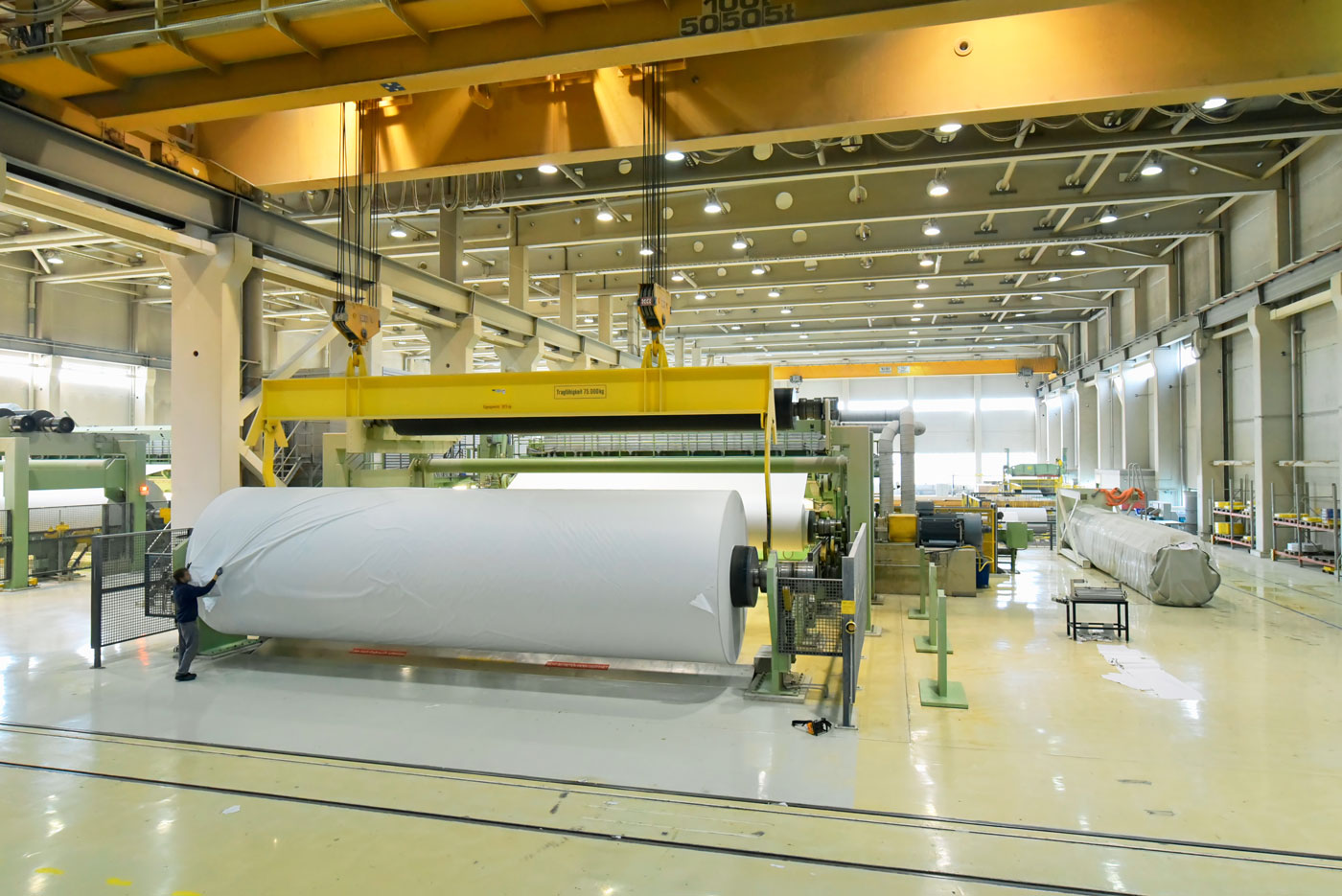
Project: High plant OEE was achieved due to excessive use of chemicals, which overloaded the wastewater treatment.
Result: Root cause analysis and optimisation of critical machine parameters lowered consumption levels.
Building Remanufacturing Supply Chains
We provide further assistance in the integration of dismantling and remanufacturing (recycling) in the value chain.
Assembling teams of experts for the integration of sustainability aspects
Building up expertise on the topic of sustainability is a key factor in the further development of production systems. We help build teams of experts to help companies create the structural and organizational conditions for continuous improvement initiatives.
Systematics and success factors of a „Low Impact Supply Chain“
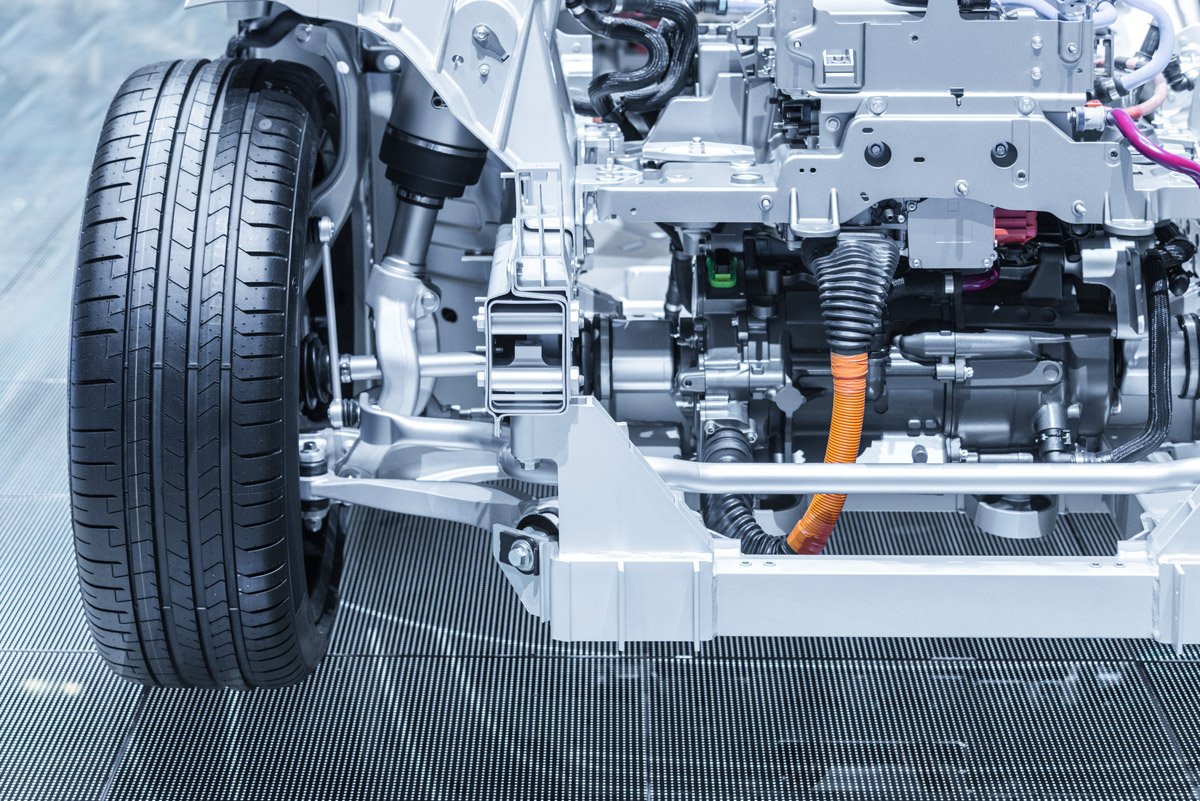
Project: Use of advanced analytics to reduce process losses.
Result: Significantly less waste improves the balance sheet of the individual product.
EINE NACHHALTIGE LOGISTIK FÖRDERT INNOVATIONEN
Strategien zur Verbesserung des ökologischen Fußabdrucks in der Logistik.
Zum Interview
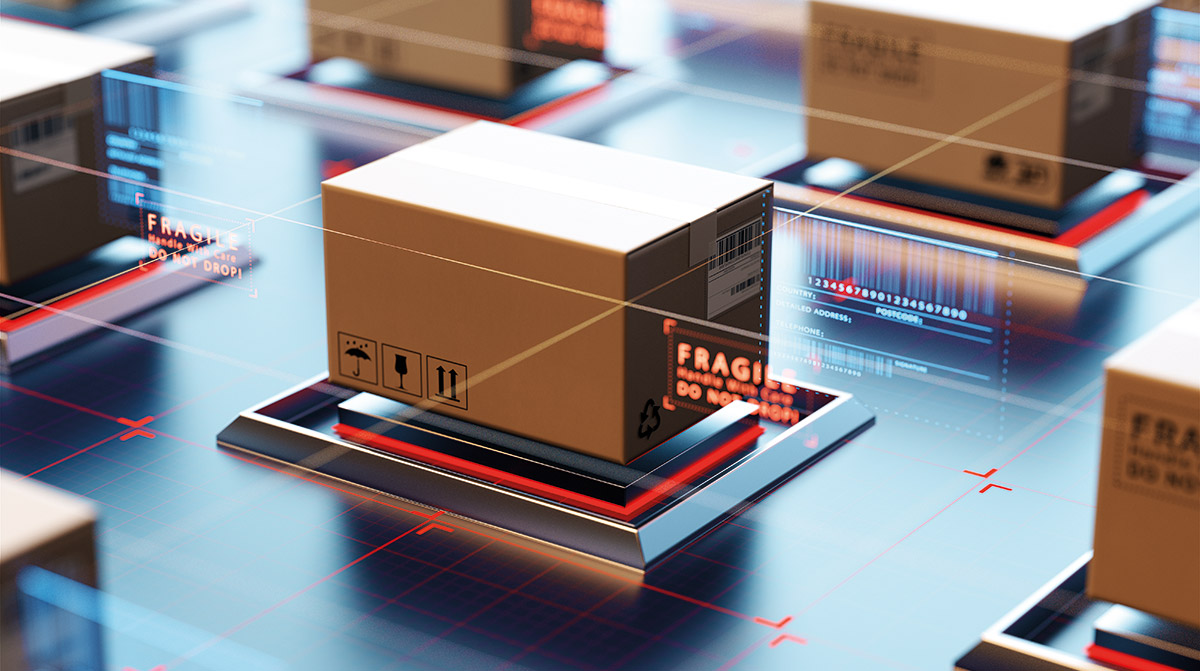
Elements for operationalizing sustainability strategies in purchasing
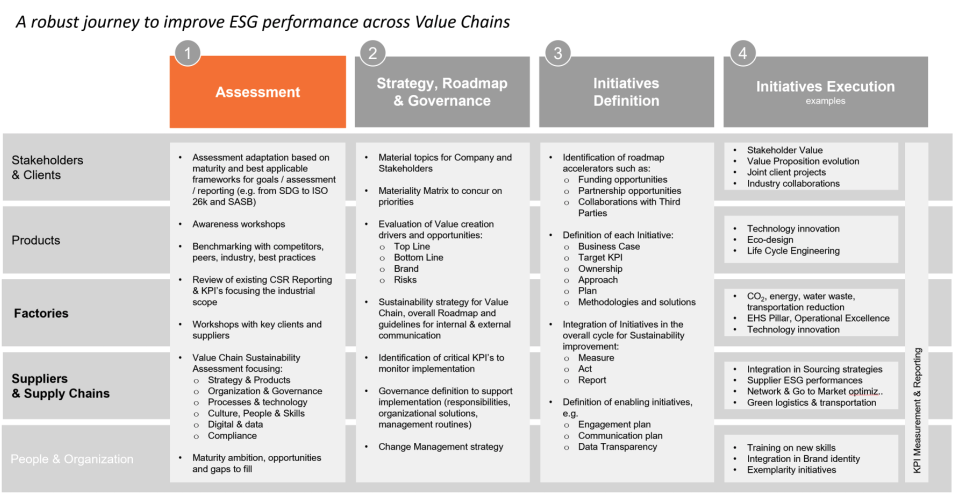
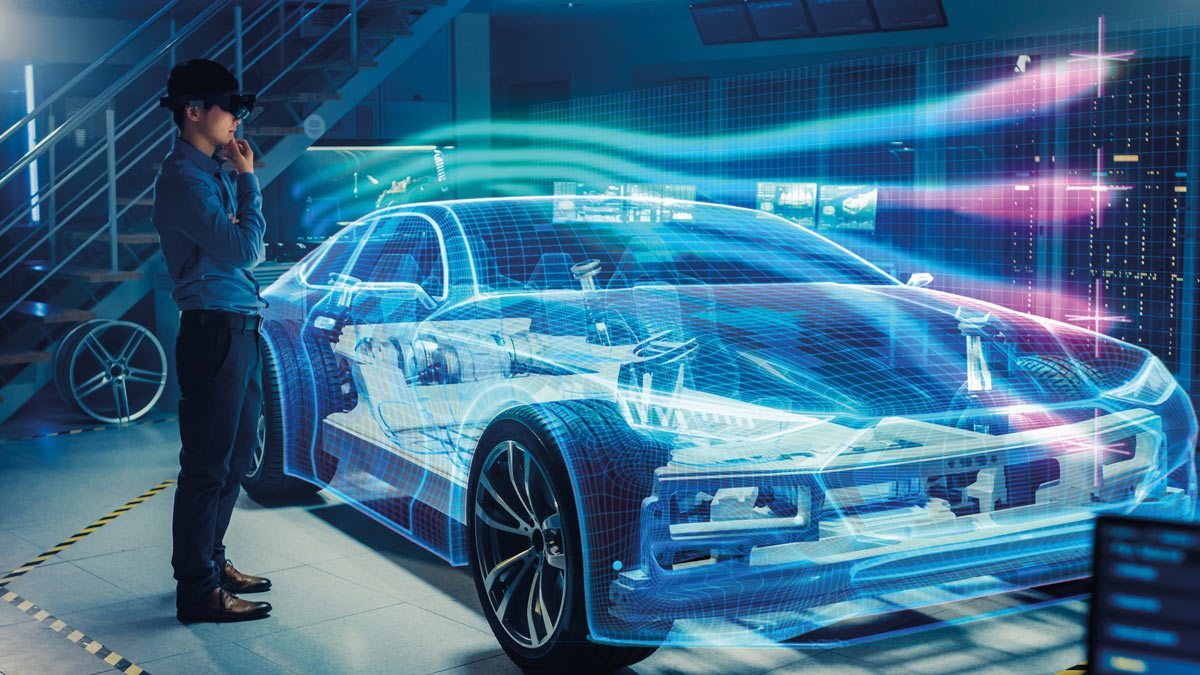
NACHHALTIGKEITSRISIKEN BEWERTEN
Ein Automobilhersteller integriert Nachhaltigkeits-KPIs in sein Risiko- und Beschaffungsmanagement.
Zum Projekt