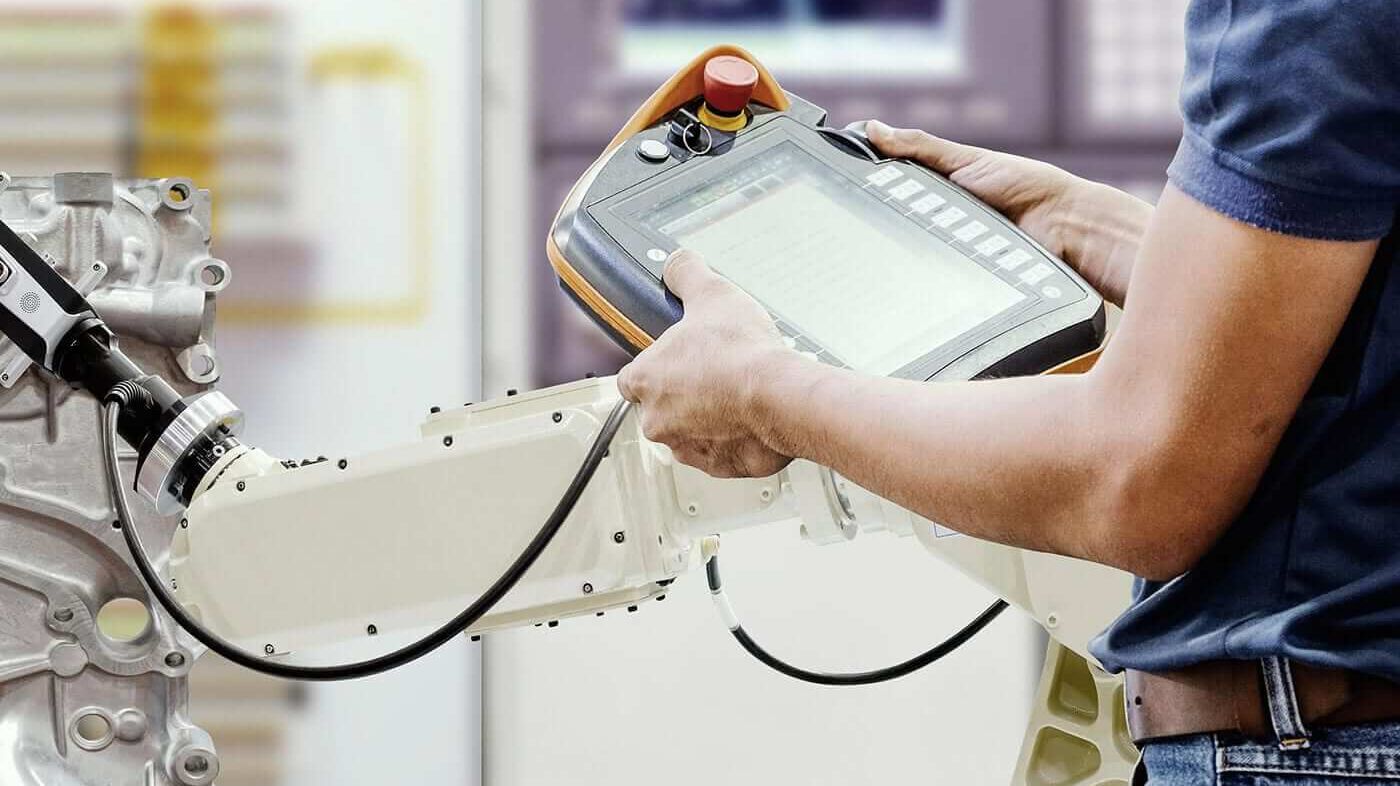
Electromobility: New manufacturing processes
Predictive quality and manufacturing
A 1st-tier automotive supplier was faced with the task of developing electromechanical components for a future electric vehicle concept. With a steep start-up curve to the accustomed series quality of the customer, the company had to implement a new manufacturing technology with new materials. Together with EFESO, it expanded its core competencies.
Challenge
An automotive supplier is confronted with two paradigm shifts in its core business as a result of the requirements of e-mobility and product digitization. In one of its plants, the company establishes adequate solutions for the production of a "new product" with completely new planning and manufacturing processes.
MoreEFESO approach
EFESO developed a future-oriented, modular overall concept with a focus on reducing waste through "predictive manufacturing" and "predictive quality" in the production line. A "Digital Process Twin" plays a central role here.
MoreLessons learned
Traditional structures in IT and manufacturing processes must be rethought and harmonized. The correct use of existing and future data is the key to success.
MoreEFESO success model
The vendor-independent consulting as well as the result of a newly set up process as an overall package were convincing. A degree of maturity was reached that allows further development to scalable IIoT architectures and smart factory based on artificial intelligence.
MoreNew manufacturing processes for the mobility of the future
Companies in the automotive industry today are confronted with the challenge of mastering more than just a serious upheaval in their market: autonomous driving brings with it a completely different kind of functionality and communication in the vehicle - the product becomes digital. In addition, alternative, more environmentally friendly drive concepts are urgently needed. All these changes have an impact on the entire product development process. As in this case of a first-tier automotive supplier who was faced with the task of developing electromechanical components for a future electric vehicle concept. With a steep start-up curve to the accustomed series quality of the customer, the company had to implement a new production technology with new materials. With EFESO, the company expanded its core competencies.
Due to the extraordinarily high complexity of the task, it was important in the first step to question the previous methods and processes in industrial engineering and process planning and to define new, suitable alternatives. The fact that there were no empirical values for this did not make the task any easier: the tools used so far were self-sufficient and the data already collected was isolated in data silos. The existing empirical values were neither sufficiently analyzed nor systematically used for further development and optimization.
Understanding and modifying processes
Right from the start of the project, the team, which consisted of nine customer employees and three EFESO consultants, was aware of one thing: it had to completely examine and question the processes, tools, procedures and planning. In addition, manual processes had to be automated, data collected, linked and analyzed. The team examined existing software solutions for adjustments and established an appropriate analytics platform for the proof-of-concept.
Verifications with Digital Process Twin
At the same time, the development of new competencies was necessary. The project team removed the previous isolation of the respective production and process data and identified the tools required for the future production process. With the help of a Digital Process Twin, the first verifications could be carried out - independent of the running production, but already with real-time data. As the next development stage in the project, the company plans to use artificial intelligence in a Smart Factory in the future to ensure a decisive competitive advantage.
Predictive quality and manufacturing
Forward-looking evaluations and analyses proved to be the key to the success of the project: The project team used the Digital Process Twin to map influencing variables and developed processes digitally by varying and optimising them. As a result, the analyses were successively refined and the quality of the predictions became more and more precise. In addition, the team linked the existing data for the first time, so that they can now be evaluated directly as real-time process data.
Meaningful process model
From the more than 200 variables, it identified the decisive influencing variables and used them to create a meaningful model for a process that had not yet been properly understood. The knowledge about the existing challenge, the identified parameters with the greatest influence on the process and the historical data as a basis guarantee a good accuracy regarding the need for action. Another decisive advantage of this approach: for each process area, the project team visualized the relevant data in dashboards, depending on the user or user group. This significantly supports the secure handling of process-oriented data by employees.
Predictive process development and control
The very good data quality of the data generated so far but not used proved to be an ideal basis for the predictive control of the production process. Step by step, the team determined the data relevant to the process and correlated them using algorithms. On the one hand, this brought them closer to the best possible processes and production regulations, and on the other hand, the step-by-step implementation of the new production processes ensured that the employees were involved in the new procedure from the very beginning.
A further central project objective was to extend the described procedure in the sense of a modular application to other production lines already in operation. This was achieved by planning and using a continuous digitization platform and a scalable IoT architecture.
Future-oriented solution
All in all, this project was not about seeking and establishing a specific solution. On the contrary, together with EFESO, the automotive supplier developed and established a completely new, complex, scalable and thus future-oriented solution for process optimization and control. The new tools are not only applicable to a specific plant, but can also be rolled out to all existing production units in all plants. Accordingly, the company can now quickly and flexibly integrate necessary changes into existing production and quality management processes - above all due to technological advancements and the resulting requirements.