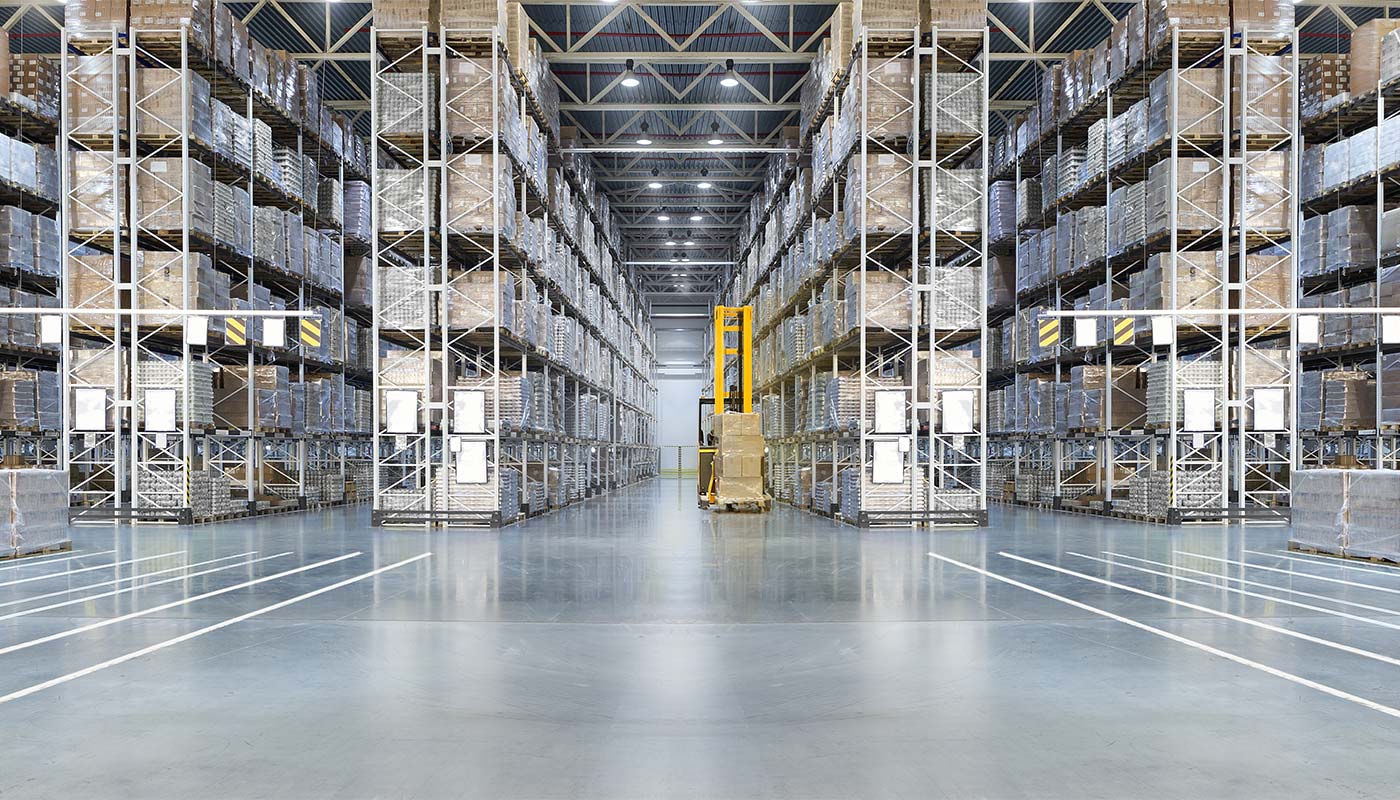
Automation boost for distribution logistics
An automotive supplier consolidates three parts warehouses into an existing fourth warehouse.
Three distribution centers of a company from the automotive industry were to be integrated into an existing fourth one. With the support of EFESO, the company mastered this task in eight weeks. For this purpose, it developed five solution scenarios with different degrees of automation ("minimal investment" to "fully automated") including layouts and monetary evaluation.
Challenge
A distribution company from the automotive industry is consolidating its distribution network following a merger. Three distribution centers are to be integrated into an existing fourth in a short time - during ongoing operations.
MOREEFESO approach
Based on a detailed bottleneck analysis, the EFESO project team developed five solution variants with varying degrees of automation in goods receipt, storage, picking and all other functional areas.
MORELessons learned
Flexibility in the implementation of the individual solution variants allows the degree of automation to be increased in the future.
MOREEFESO success model
For warehouse projects of this complexity, a detailed bottleneck analysis of all functional levels and professional preparation of the enormous amounts of data in a data center are crucial to success.
MORETwo large distribution companies in the automotive industry consolidated their distribution networks after a merger. The central challenge was to reunite three spare parts distribution centers in an existing fourth. A task with enormous dimensions, because the turnover of approx. 1.5 million outbound items per year will increase to around 7 million - an increase of approx. 300 percent in the outbound sector! Based on a bottleneck analysis on the functional level, EFESO developed a suitable solution concept within only eight weeks, including the layouts and an evaluation of the costs.
In just eight weeks, a concept was developed for consolidating four distribution centers under one roof.
Distribution networks in the automotive industry have often grown historically and are partly characterized by outdated or obsolete business models and strategies. However, inefficient locations lead to increased costs and inadequately exploited distribution potential. If companies with their own distribution logistics merge, this represents an opportunity for realignment in the face of such inefficiencies. In the case study described, three spare parts warehouses were to be dissolved and integrated into a fourth, already existing spare parts warehouse. The task was to develop a coherent concept including the concrete spatial design and layout of the warehouse as well as the processes. This concept ultimately made it possible to consolidate a total of four spare parts distribution centers in one location.
At the beginning, the main question was whether the integration of four sites could be achieved at all, both technically and in terms of processes, without interrupting operations - and, if possible, in a "minimum investment solution". In addition, the level of automation had to be defined in order to gradually optimize operations beyond 2023. Two special circumstances made these tasks considerably more difficult: Firstly, the capacity of the fourth warehouse was exhausted, and secondly, the project had to be implemented during Covid-19, i.e. remotely and without being able to inspect the situation on site.
Due to Covid-19, project implementation was done remotely.
Project work with a small time window
The EFESO project team therefore had to familiarize itself with the hall and infrastructure using CAD drawings and cell phone videos. On the customer side, the project team consisted of four colleagues. The solution had to be ready in only eight weeks. This demanding task was solved in the following steps.
Analysis
The project team planned a period of two weeks for the analysis phase of the current situation. After a "tour" of the premises via cell phone camera, an evaluation of the data pool with regard to processes and areas, material flow, planning and scheduling, and IT was to be completed in this time. For the strategic framework, different topics were scrutinized. These included automation, digitalization, technology innovations in the areas of warehousing, transport, IT, but also market requirements for future logistics, business prospects and growth scenarios. Since distribution logistics generates significantly larger volumes of data than in-house logistics, 7 million shipping items alone had to be analyzed. In order to be able to handle the enormous data volume of 12 gigabytes, the team brought the data into a professional SQL database base.
Seven million shipping items p.a. had to be analyzed.
Concept creation
Based on a bottleneck analysis, the project team created a complete range of proposed solutions with corresponding technology concepts. A total of five variants with increasing degrees of automation were designed:
- a "Minimal Invest Solution" that addresses the bottlenecks, but has a very low level of automation and numerous manual processes with high staffing requirements
- a "Critical Invest Solution", i.e., a viable solution for increasing volume with low investment while reducing labor, low automation, and high staffing levels
- a solution with step-by-step automation in the area of goods receipt, goods issue/shipping, while the warehouses remain unchanged
- step-by-step automation, including partial automation of warehouses, e.g. a fully automated small parts warehouse (shuttle storage) for materials that are used frequently and in large quantities, or an automatic packaging system
- a completely automated variant with automation solutions in all relevant areas of the goods receiving process, warehouses as well as shipping, including shuttle storage, automated pallet warehouse (retrofit), transport systems, staging area for automated shipping incl. pallet picking & loading
The company opted for the fourth variant.
Five proposed solutions with increasing levels of automation were designed.
Valuation and business case
The planning team developed a detailed layout of the real area with the business equipment in 2D/3D. This was subjected to a final evaluation according to monetary and non-monetary aspects. The current object and space situation as well as the requirements for the implementation with regard to the building and the technologies were taken into account. As a result, a complete report with cost estimates for the implementation planning and for tenders was available to the management for decision-making.
EFESO solution approach: automation of incoming and outgoing goods as well as the warehouse
Of the five solutions proposed by the project team, variants 3 to 5 differed in their degree of automation. Whereas in variant 3 only the inbound and outbound areas, i.e. goods receipt and shipping, were to be automated, variant 4 already provides for partial automation of the warehouses. In variant 5, the warehouses are completely automated.
As the degree of automation increases, so does the corresponding investment volume, from just under 3.5 to up to 17 million euros. The ROI for all solutions is around two years. This is because increasing investment is accompanied by a corresponding reduction in the FTE (Full Time Equivalent; time value that a full-time employee provides) and the costs are thus balanced.
Investment volume between 3.5 and 17 million euros depending on the degree of automation.
The company ultimately opted for variant 4 with a relatively high degree of automation. One of the reasons for this was that the consolidated warehouse was already limited to 250 FTEs in terms of space, but a lower level of automation would have involved disproportionately more manual processes. With variant 4, an FTE reduction of about 40% (-173 FTE) was ultimately achieved. The central elements of the EFESO solution are:
Automated goods receipt process
The layout of the chosen variant provided for a completely automated goods receiving process. The delivered pallets are either directly stored by conveyor technology or repacked into containers on breakdown tables or distributed on half pallets, separated into smaller sales units and transported to the respective container warehouse. Fully automated conveyor vehicles connect the goods receiving area with the breakdown tables or the warehouses. Employees remain at their workstations and everything is delivered automatically. Disposal is also automated. Whereas employees used to have to take their packaging waste to disposal containers by hand, this is now done automatically overhead.
Automated warehouse
In this variant, the warehouses are already automated, i.e. the pallet warehouses (retrofit), which were previously operated manually, can in future be controlled via storage and retrieval machines. Transport systems will then operate in the existing shelf warehouses.
Fully automatic small parts warehouse
While employees today still walk through the warehouse and collect the desired parts, in the future they will work permanently at a picking workstation. Small storage and retrieval machines (shuttles) travel fully automatically through the rack storage area, fetching the appropriate bins from which the employees remove the parts. The shuttle returns the totes to the warehouse. This is also of great advantage for the ergonomics and the strain on the employees.
Improved outgoing goods
As end customers order more and more components directly via the company's web store, outgoing goods are becoming increasingly small-scale. This is why automatic packaging and labeling are taking on greater importance. An automatic packaging system cuts and folds the cartons individually so that no further packaging material is required. The cartons are automatically closed, labeled and transported directly to the shipping department.
Extensive automation of all functional areas increases storage capacity by about 30% for cartons.
Lessons Learned
If the degree of automation is fully implemented in the selected variant, storage capacity can be increased by around 30% to 90,000 cartons and, in the case of pallets, by 40% to then 45,000 pallets.
Due to the increasingly small goods issue, one pallet in goods receipt will no longer be three items, but ten or twelve in the future - i.e. , the effort increases extremely, even if the total volume is not much higher. Here, the team found out that a certain flexibility of the individual solution variants makes it possible to increase the degree of automation at any time in the future, i.e. to migrate from variant 4 to variant 5 step by step, so to speak.
The total storage capacity for pallets can be increased by 40%.
EFESO success model
The key to the success of this project was certainly a very detailed bottleneck analysis at the functional level. Thus, all process elements - starting with goods receipt, putaway and picking, through the entire warehouses to staging - were analyzed in detail. What capacities exist? What are the relevant variables? Does it fit or does it need to be changed? Where are the bottlenecks and what solution elements could be used to resolve them?
Detailed bottleneck analysis as the key to success.
Another key success factor was that the analysis of the enormous volumes of data could be handled by transferring it to a professional database. The planning was also based on a fully equipped data center. This makes it possible to implement adjustments and changes quickly instead of having to make them manually. This meant that follow-up work could be handled with relatively moderate effort.
In the project described, it also proved very helpful to look at all viable solutions instead of focusing on one supposedly suitable solution at an early stage. In the course of the analysis, it turned out that the originally preferred, first solution variant was physically not feasible. The EFESO reference model and LogROM® helped to evaluate the individual variants.
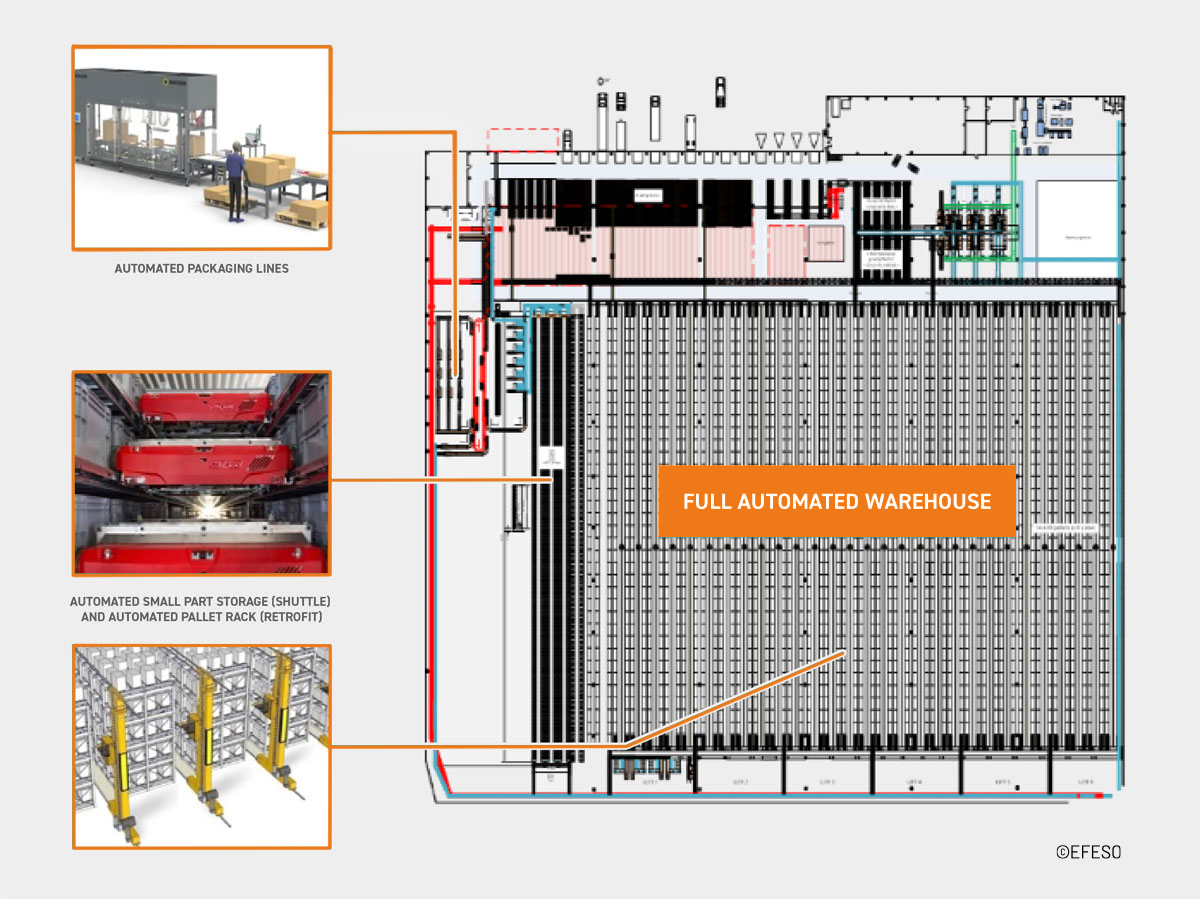