Supply Chain
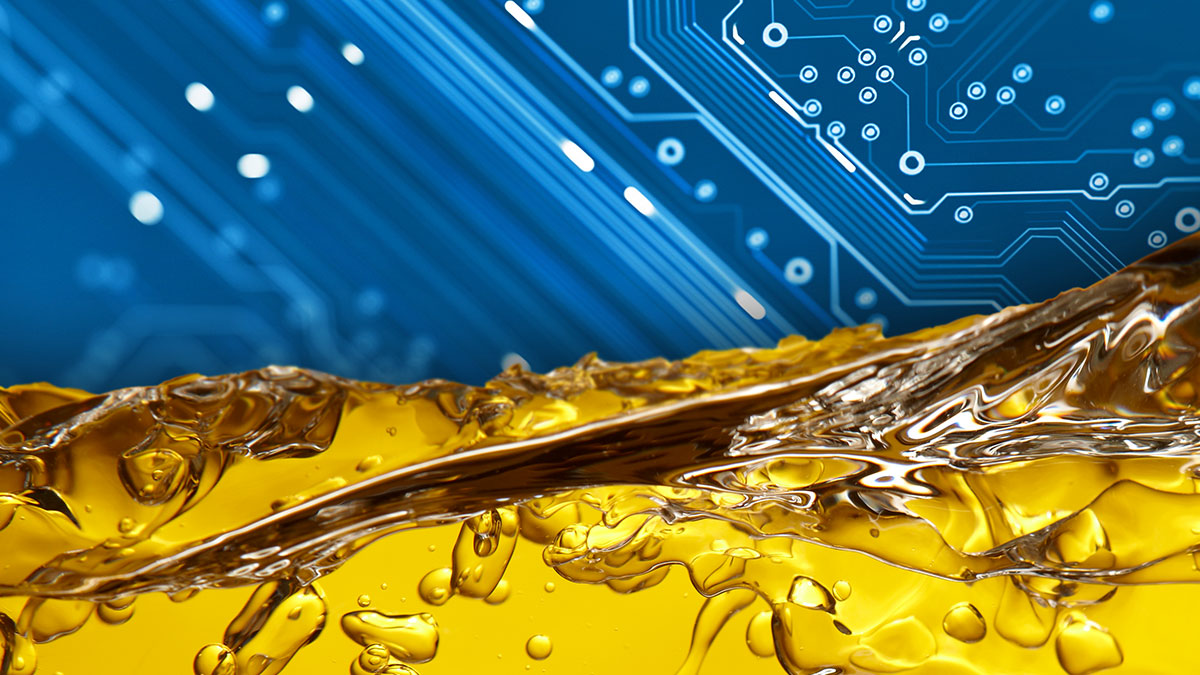
Will forecasting replace planning in supply chain management in the future?
Planning is one of the central tasks of supply chain management. Among other things, it determines which production resources must be available when, in what quantity and at what location. However, given current global supply chain risks and increasingly volatile customer requirements, traditional planning methodologies no longer do justice to the dynamics of many industries.
As a result, supply chain management and planning may have to be thought about differently in the future, with a move away from static planning. Instead, predictive forecasting of customer needs and flexible adaptation of supply chain management to dynamic developments will likely become the norm. The basis for this is provided by new tools that include the likes of demand sensing, which combines artificial intelligence with real-time data to predict short-term changes in consumer demand with high accuracy. This enables companies to respond quicker to market fluctuations, minimize planning errors and significantly reduce waste.
Who will win the race for low-carbon resources?
The ongoing drive to lower Scope 3 emissions means that the need for low-emission precursors - low-carbon resources, ranging from raw materials to highly processed components - is daily increasing in the manufacturing industry. Today, the demand for ‘base‘ materials such as green steel or recycled plastics already exceeds the available supply on the world market.
It‘s clear that companies will have to develop new strategies to secure reliable, long-term access to low-emission raw materials and other materials. The focus here will be on building closer partnerships between companies and their suppliers. Together, they will be able to develop roadmaps for expanding the supply volumes of sustainable or low-emission materials and actively support them (e.g. by providing financing assistance for new production facilities or helping with the switch to renewable energy supplies).
How do you apply ‘in-house’ optimization methods to the entire supply chain network?
Production and logistics processes in most manufacturing companies have been developed over many years and optimized according to well-known principles such as lean management or ‘just-in-time‘. As a result, they have helped to maximise efficiency and operate value creation processes in a more sustainable way. That‘s why most process ‚breaks‘ and inefficiencies (e.g. due to downtimes, empty runs and other forms of waste) occur when the processes of different supply chain partners are out of sync. Those glitches are often accompanied by a lack of data transparency and quality.
In order to minimise the resulting negative environmental impact, a careful analysis of the main waste drivers at these interfaces is required, which allows measures for a more sustainable process design to be developed. Typical starting points are in the areas of transport and packaging design. For example, the number of empty runs can massively be reduced by optimizing loading and bundling trips as well as adjusting delivery rhythms.
Is supply chain instability becoming a sustainability killer?
The numerous crises the world has endured over the past few years have massively shaken up global supply chains. As a result, the trend toward streamlining supply chains has been partially reversed, in favor of larger inventories and planned redundancies along the supply chain. This shift comes at the expense of sustainability, as buffer stocks are invariably accompanied by greater storage requirements and energy consumption, as well as higher transport costs and risk of obsolescence.
To resolve the tension between increasing resource efficiency and maintaining supply chain stability, companies need to find new ways of increasing the resilience of their supply chains without neglecting sustainability aspects.
One possible way forward is to realign procurement strategies for global, regional and local sourcing, something that has already been increasingly implemented in the wake of the current crises. Not only can this effectively reduce global dependencies, but it also brings down transport-related emissions.
Furthermore, the instruments for identifying and assessing supply default risks need to be improved. In this way, companies can stockpile individual components or materials with a high availability risk or difficult substitutability, while the other supply flows can be streamlined.
Is the traditional supply chain now becoming a circular supply chain?
The embedding of circularity principles across industry means that companies are no longer just responsible for products, per se, but for entire product life cycles. This means that the return of products or materials to the value creation process, through repair, reuse or recycling, is becoming considerably more important.
This isn‘t just for the sake of enhancing sustainability: increasingly, it also makes sense from an economic perspective as it allows for the recovery of strategically important raw materials (e.g. for battery production).
This creates multiple new challenges for supply chain management: on the one hand, an efficient reverse logistics process has to be established to facilitate the return of products, which in itself must be designed to be as sustainable as possible through optimized transport and route planning.
On the other hand, it is necessary - especially in the case of highly engineered and variant-rich products - to understand which specific components or raw materials can be extracted and reprocessed or reused, and which need to be disposed of properly and in what form. Addressing both challenges necessitates better traceability of the products, not just in terms of knowing which products were delivered in which form to which customers, but also in what condition. In short, when considering the entire life cycle, it‘s vital now to take the requirements of the entire supply chain – extant and future - into account as early as possible during the product development process.