Digital Twins (Process Simulation)
Digital twins are virtual, dynamic models that represent a physical object completely and in real time. Their use is particularly worthwhile for cost-intensive, critical and long-lived products such as complex industrial machines. With precise predictions about their performance, weak points, material fatigue or other risks, they provide manufacturers and operators with valuable insights for product optimization and maintenance.
With digital process twins, companies analyze not only products, but also complete value creation processes and networks. With a virtual simulation of the entire value creation cycle, they make hidden inefficiencies visible. They also quickly identify critical situations in production processes and open up starting points for continuous process improvements.
As the leading consultancy EFESO has extensive content, technological, methodological and industry-specific experience in designing and building Digital Twins for products, plants and processes. Our service portfolio includes the following topics in particular:
- Analysis and conception of business cases for the use of digital product and process twins (Digital Twins)
- Vendor-independent technology selection and deployment
- Descriptive, predictive, and prescriptive data analytics
- Implementation taking into account the process-related and organizational specifics of the respective company and its suppliers and customers
For companies in the manufacturing industry, we realize this in two areas of application in particular:
- With Digital Supply Chain Twins, we create a virtual mirror image of a supply chain or supply network that integrates suppliers and customers in real time.
- With digital twins of production and logistics (Digital Factory Twin), we capture and improve the working environment and value creation processes within the factory walls. This also supports digitization/automation initiatives and the further development to a smart factory.
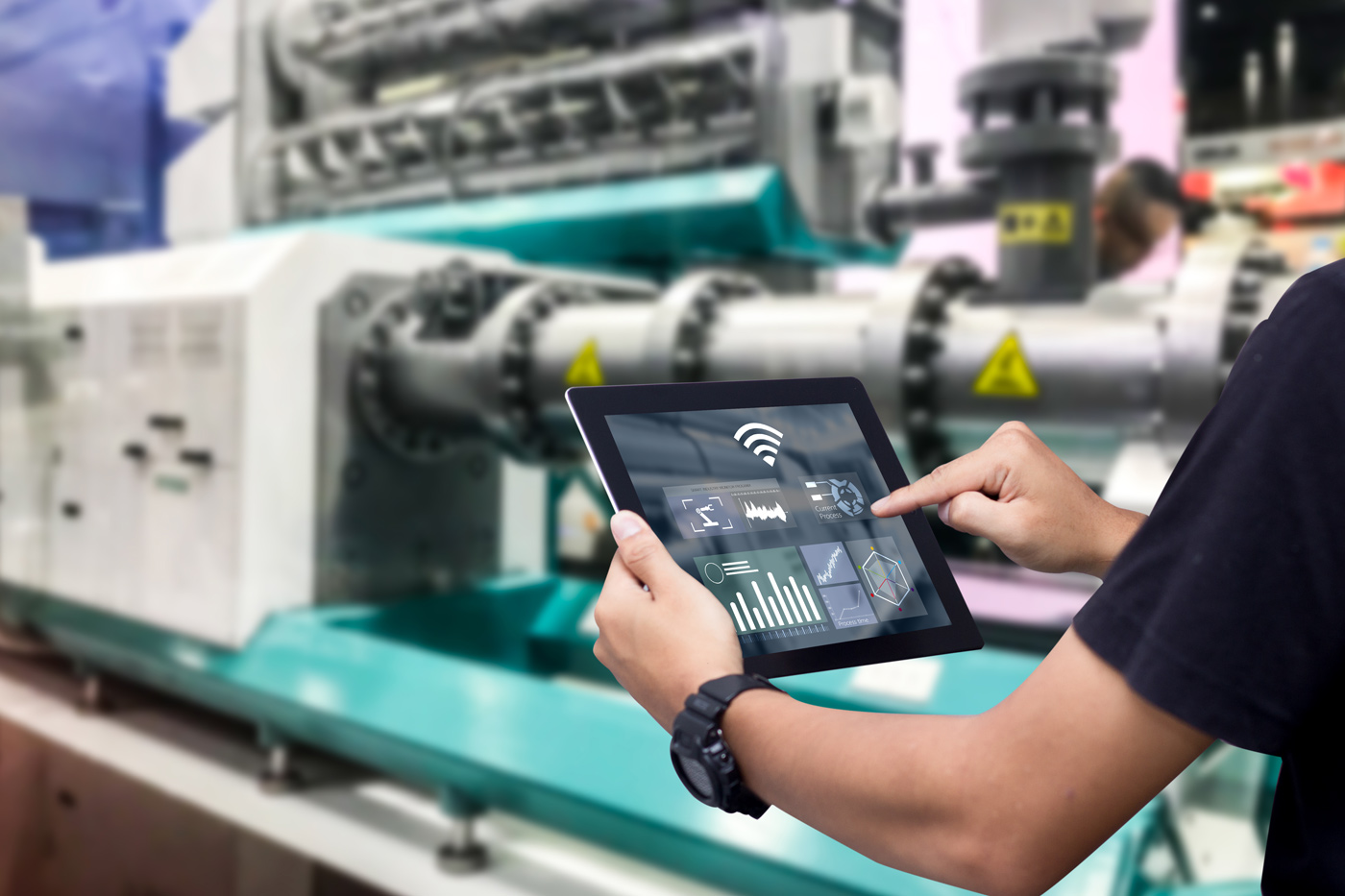
Project: Conception of a sustainable production and distribution network and consideration of cost and robustness / flexibility criteria.
Procedure: Use of a digital twin / dynamic simulation model with several variables such as
- Vertical integration
- Structure and role of plants and suppliers
- Personnel requirements in direct and indirect areas
- KPIs at network and location level
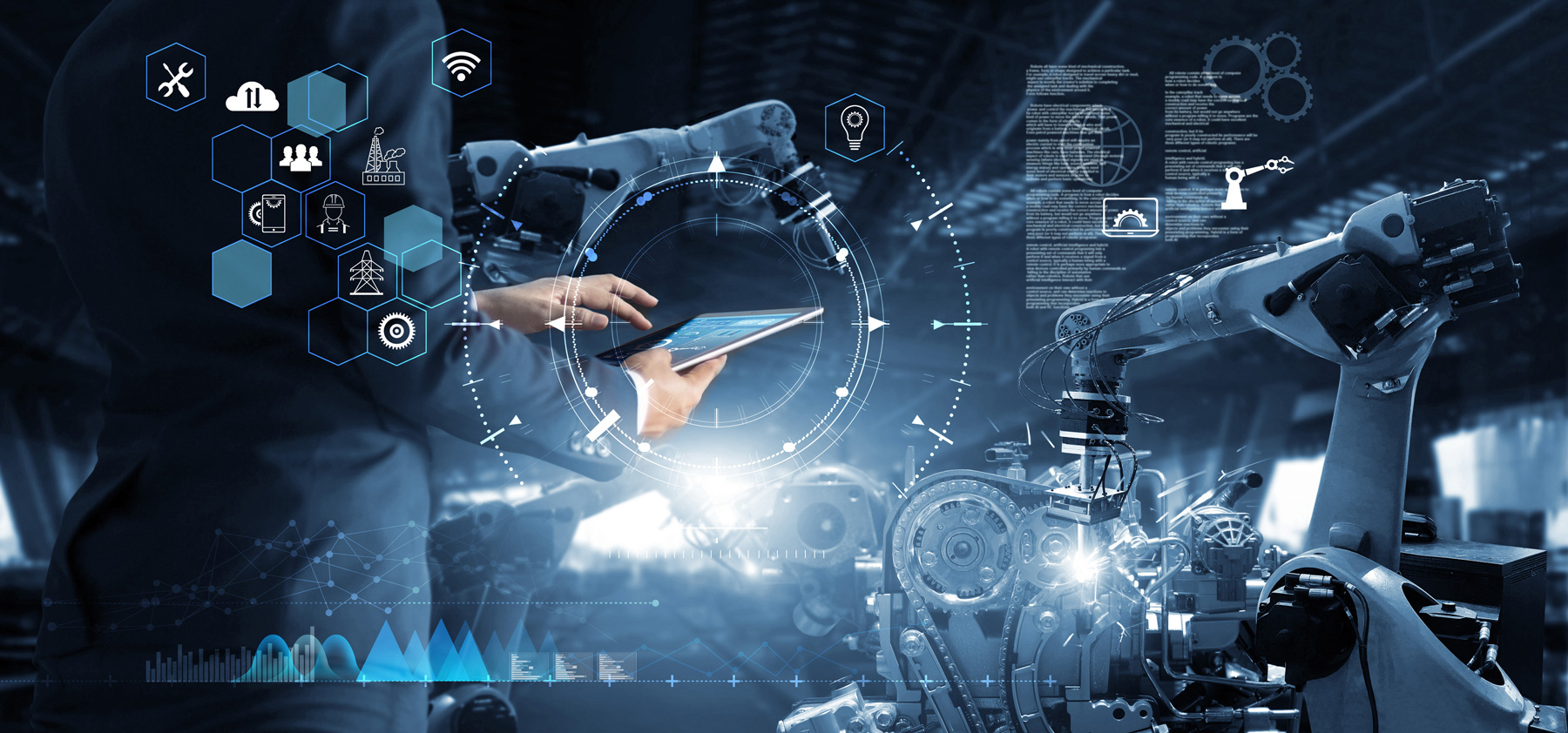
Project: Material flow improvement in a location with complex conveyor lines and expensive buffer times; evaluation of alternative system investments with regard to their effects on the material flow.
Results: The use of a digital twin / dynamic simulation model resulted in a
- Reduction of buffer and storage investments by 30% compared to the static approach
- Use of the model for decision-making in production planning / control
Use of a Digital Process Twin with EFESO
When setting up a Digital Process Twin - for example in the context of digital store floor management - we first work with the client to determine which process parameters have an influence on the performance of the processes or systems in focus. The next step is to correctly record the existing process data. If necessary, we supplement this with additional data, for example from sources such as IoT sensors or edge computing systems. The collected data is then combined and analyzed in a cloud application.
In this way, we create the foundation for building a virtual model that maps the process-relevant parameters, their interactions and critical values in the entire process chain as accurately as possible. The Digital Process Twin developed from this enables the company,
- Perform descriptive, predictive, and prescriptive analyses in real time;
- integrate the model with other technologies such as machine learning;
- sustainably improve the quality, efficiency and transparency of processes.
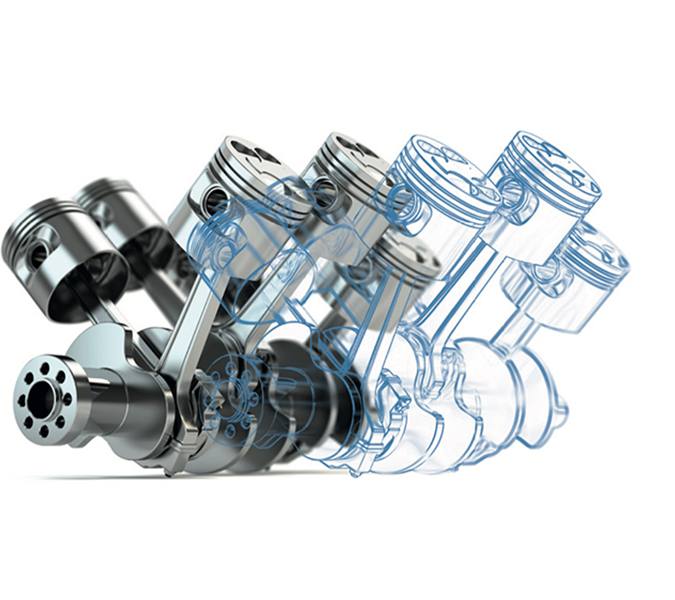
How can companies benefit from mapping a value stream completely as a Digital Twin? How do you build a Digital Process Twin - and which basic rules should be observed for its further development? These and other aspects are summarised in the expert contribution by Robert Benacka, CEO of ROI Management Consulting.
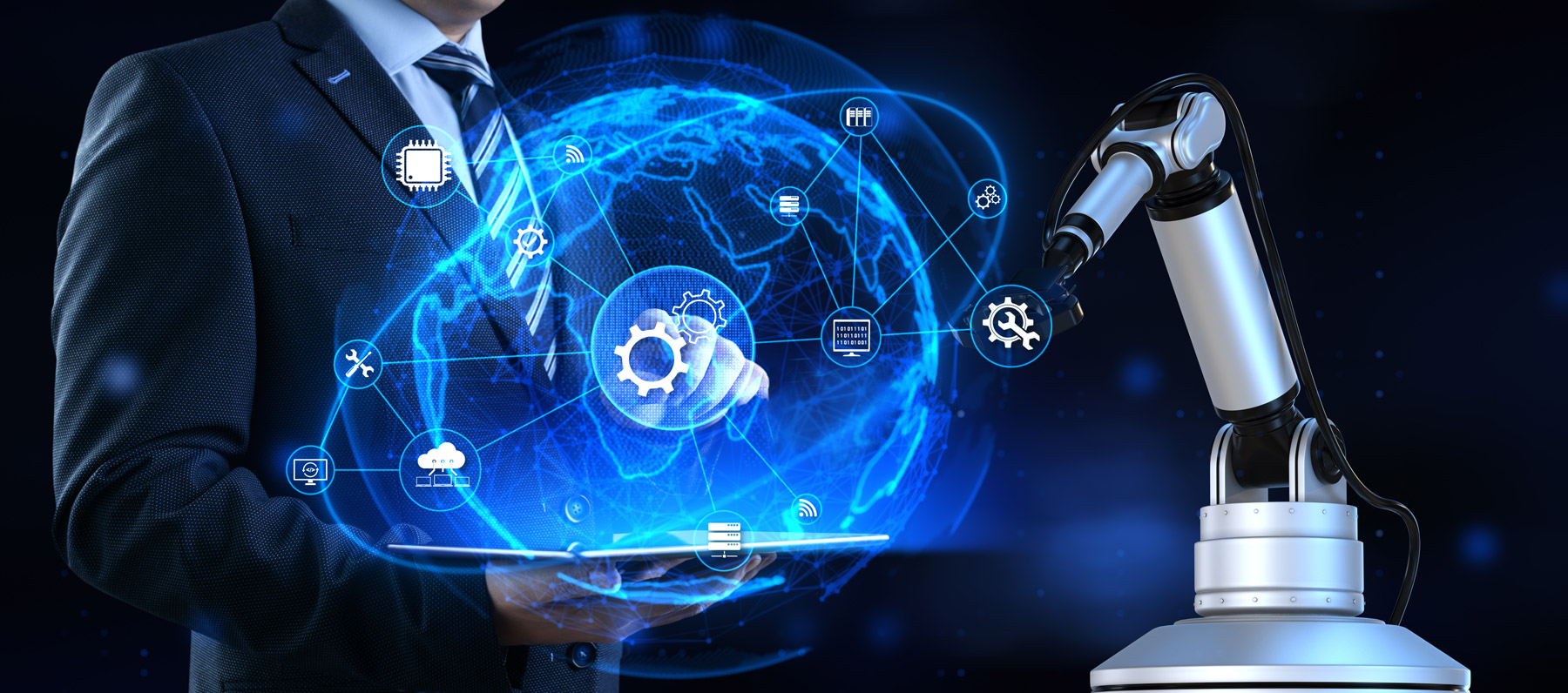
In this interview, Dipl.-Ing. Martin Höller, Technical Manager at Biohort GmbH, describes how his company uses the technology to modulate manufacturing in real time, what implications this has for data management, and where the limits of digital twins might lie.
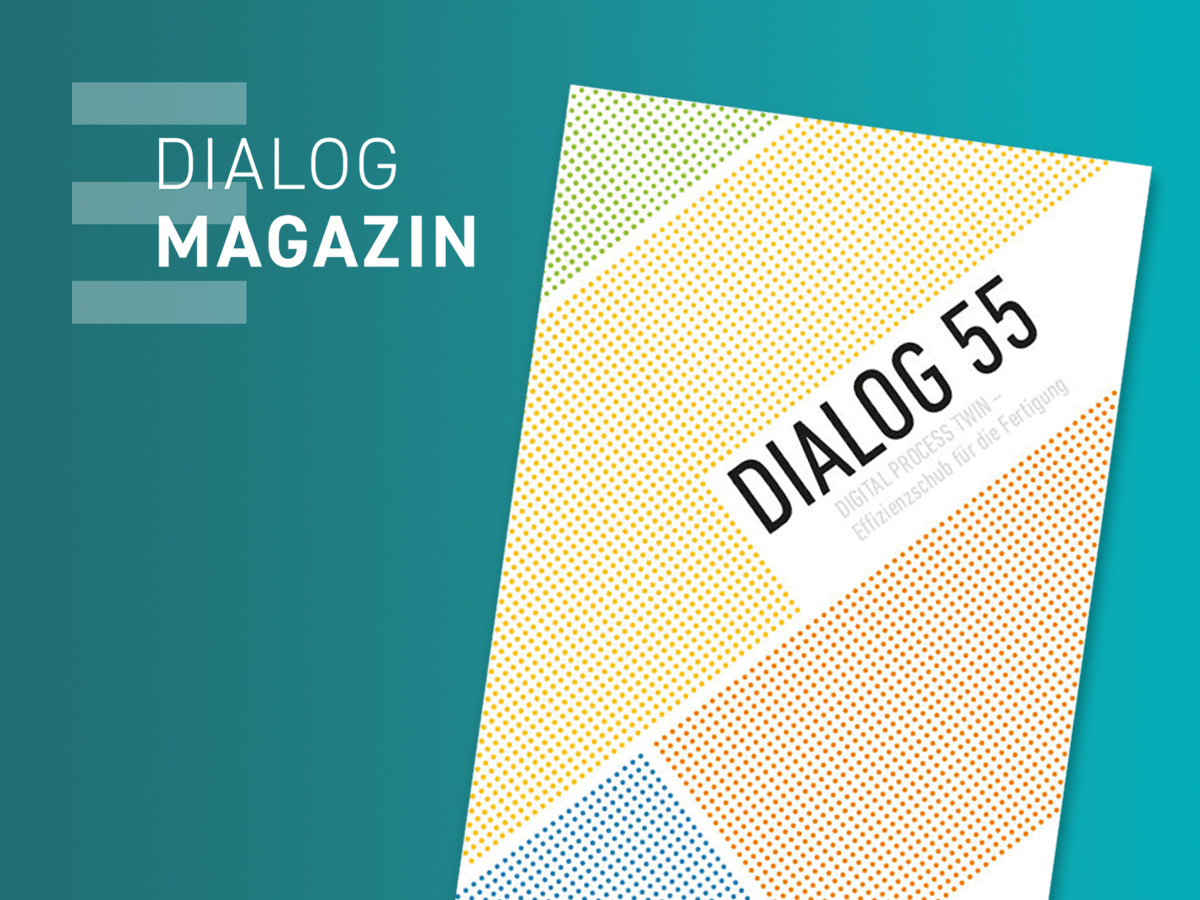
In addition to an increase in efficiency and quality, the Digital Process Twin approach offers new possibilities in the evaluation, control and qualification of suppliers. In issue #55 of our DIALOG magazine, we present the most important starting points for companies.
Taking value creation processes to a new level of performance
For these and other application goals, Digital Process Twins can map all stations of a company's value chains and networks, from purchasing and supplier qualification to logistics and production to customer-specific delivery or maintenance planning. This enables companies to perform a meaningful simulation of different scenarios such as:
- How does the shutdown of a line or plant affect the supply chain - for a day, a week, a month?
- How quickly is the ability to deliver restored in these cases?
We make the potential of the technology tangible with visualization tools, for example in digital 3D models of warehouses or production lines, in which all processes are shown in detail and changes are easily simulated:
- How do production KPIs change in a different shift schedule, for example?
- What are the consequences for logistics when more employees or forklifts are used in the warehouse?
- What design variations are possible in the available manufacturing/storage space to make workflows more efficient and ergonomic?