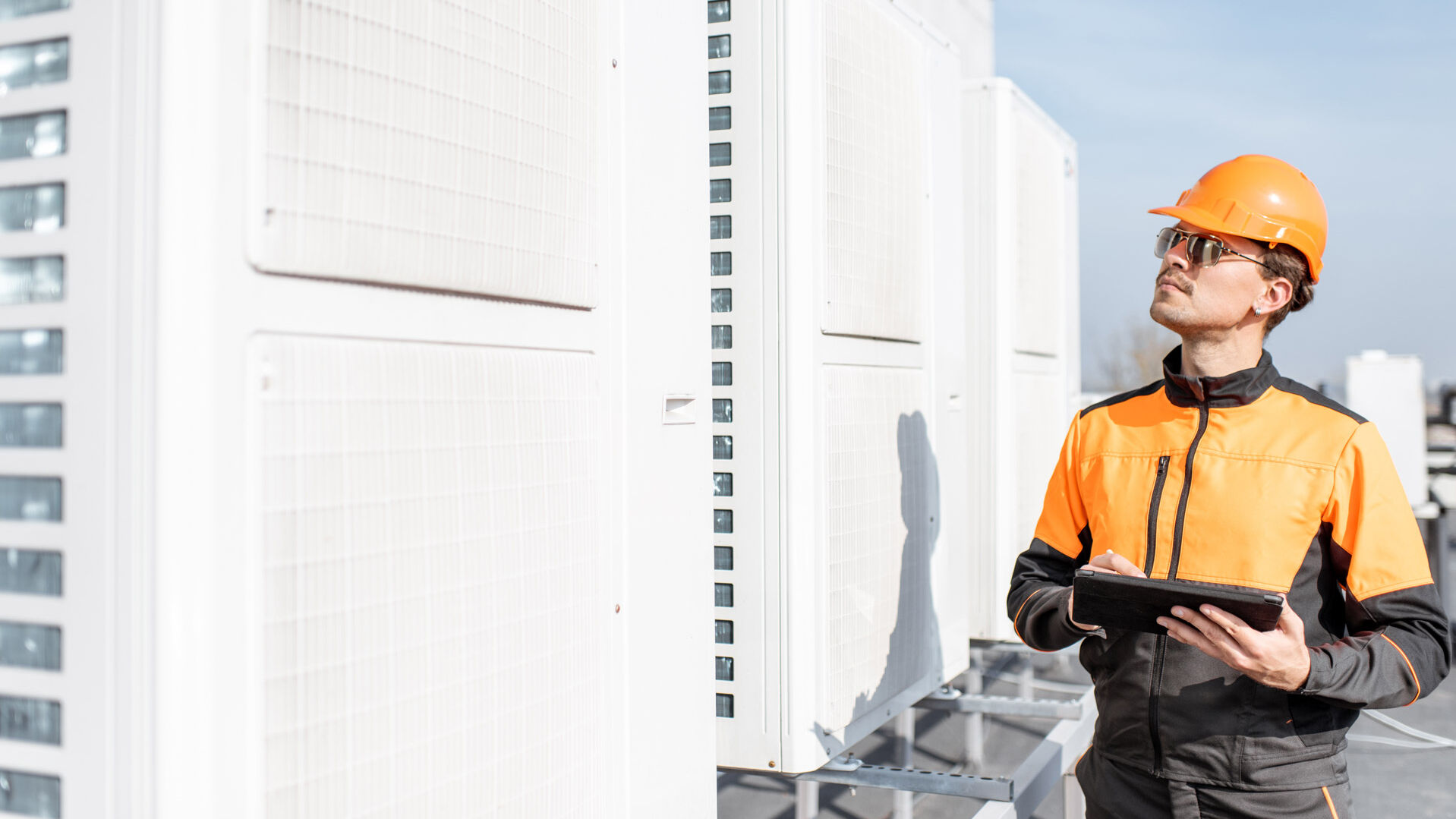
From zero to mass production
Production and logistics planning for the establishment of a state-of-the-art Gigafactory in the fast-growing European heat pump market.
The volume of the European heat pump market is expected to double from the current level of around 15 billion euros by the end of the decade. A venture capital company specializing in sustainable investments wants to participate in this growth and be a relevant supplier on the market with its start-up by 2030. The special challenge: So far, the company has not produced a single heat pump. EFESO supported the company in the production and logistics planning for Europe's first Gigafactory for the production of heat pumps. Thus, the project team laid the foundation for one of the most ambitious Klimatech projects in Europe.
Challenge
In just four years, a start-up wants to develop from a newcomer to one of the highest-volume manufacturers on the European heat pump market. To achieve this, highly scalable production capacities must be built up in a very short time.
MOREEFESO approach
Within twelve weeks, EFESO develops a complete production and material flow planning for the construction of the planned Gigafactory. A comprehensive smart factory concept ensures a growing degree of automation.
MORELessons learned
To safeguard the demanding schedule and provide the company and investors with the necessary security, the early equipment management approach proved to be a valuable tool for identifying and dealing with risks at a very early stage of the project.
MOREEFESO success model
With a production and material flow planning concept that was unusually detailed for this early project phase, EFESO provided the basis for a fast and low-risk ramp-up of the planned Gigafactory.
MORERapid build-up of highly scalable production capacities
The vision is extremely ambitious: in just four years, the transformation from heat pump start-up to one of the highest-volume manufacturers on the European market is to be achieved. To this end, the company plans to build a state-of-the-art Gigafactory in Central Europe with a production capacity that can be increased from an initial 40,000 to over 500,000 units per year – at manageable costs and high quality. In order to enable a rapid ramp-up and at the same time provide investors with the necessary planning security, the task was to set up a production and logistics concept that would enable reliable cost and capacity planning.
The goal: to go from a heat pump start-up to a high-volume manufacturer in four years.
Comprehensive production and material flow planning
Together with the company and the project partners involved, the EFESO team developed a complete production and material flow planning for the construction and ramp-up of the planned Gigafactory within just twelve weeks. In addition to a detailed description of the production and assembly processes, this also included comprehensive warehouse and intralogistics planning as well as the machine concept and layout planning.
To ensure the highest possible planning reliability, various scenarios were taken into account in terms of production volume, vertical range of manufacture and degree of automation. The result is a comprehensive and extremely detailed picture of the future factory, which ensures a high level of transparency at the level of production costs, capacities and personnel requirements down to the unit cost level.
The project team developed a complete production and material flow planning – within just twelve weeks.
Future Factory as the base for an end-to-end process chain
The customer's conscious decision to manufacture in Europe in order to save CO2 emissions during transport comes at the expense of higher labor costs. In order to nevertheless be able to realize competitive manufacturing costs with a high degree of vertical integration and at the same time enable a continuous increase in production capacities, the EFESO team relies on a comprehensive Smart Factory concept.
This is expressed in a growing degree of automation as well as various Industry 4.0 elements throughout the factory. These include a digital process twin, AI-supported tools for minimizing waste, and wearables for employees on the store floor. The Future Factory is based on an IT/OT architecture that is designed to enable an end-to-end process chain from ordering in the app and production of the heat pumps to delivery and installation at the end customer.
Integrated risk management and scenario-based planning
The launch of a completely new product is always associated with high risks. Especially when the time to the planned start of production is as tight as in the present project. In order to effectively meet these challenges, Early Equipment Management (EEM) has proven to be particularly promising. Firstly, because it allows a large part of the workload to be shifted to early project phases. Secondly, because EEM supports the identification and handling of risks at a very early stage of the project in the sense of integrated risk management, thus helping to safeguard the ambitious schedule.
Early Equipment Management (EEM) supports risk avoidance in a very early project phase.
Detailed production planning as basis for fast ramp-up
With a production and material flow planning concept that was unusually detailed for this early project phase, EFESO provided the basis for a fast and low-risk ramp-up of the planned Gigafactory. At the interface between strategic planning and operational implementation, the project team ensured a seamless translation of the vision into viable and highly scalable solutions at the store floor level and accompanied the customer from early conception to ramp-up of production on site.