- Holistic evaluation of existing planning processes and organization (end-to-end), including demand planning, supply planning, demand supply balancing, executive meetings.
- Development of a consistent and valid database as a basis for planning.
- Deriving suitable scenarios for achieving operational and financial performance targets.
- Definition of SLAs (Service Level Agreements).
- Creation of an organizational concept for cross-interface cooperation within the framework of S&OP.
- Introduction of company-wide KPI systems to control process quality.
Sales and Operations Planning, Integrated Business Planning
Clear planning enables companies to adapt their value creation processes to volatile sales and procurement markets. End-to-end operational planning (S&OP, Sales & Operations Planning) has proven itself as a management process to guide the corporate functions involved towards joint, coordinated and therefore effective action.
S&OP objectives vary from the overall alignment of the organization with financial targets to supply chain network management. However, there are often recurring challenges to be solved, such as the following:
- Which customers are served first in the event of capacity restrictions?
- What measures can be taken to cope with exceptionally high incoming orders?
- How much stock is absolutely necessary to cover customer requirements?
Combined sales, production, and financial planning
With EFESO, companies create holistic supply chain planning. This combines strategic alignment with budgeting and operational planning. The focus here is on:
- Central organization of S&OP: consolidation of sales, production and financial planning with rapid decentralized execution.
- Designing S&OP in the context of Integrated Business Planning (IBP): preparation and visualization of data with the S&OP/IBP Digital Cockpit from EFESO.
- Safeguarding planning: process coordination of all departments involved, joint forecasting and establishment of a transparent data model.
- Achieving a measurable value contribution from operational planning - for the operational processing of customer orders and for efficient corporate management.
Framework conditions and IT infrastructure for S&OP/IBP
The consultants at EFESO have the knowledge and implementation experience to realize end-to-end functioning S&OP processes. Together with our clients, we solve these and other tasks in S&OP/IBP:
Review and further development of S&OP/IBP processes and organization
Development of a suitable IT infrastructure
- Definition of supply chain planning requirements for IT support.
- Comparison of existing IT tools and their use in the planning process with the requirements (selection of supplementary tools if necessary) - independent of the provider.
- Identification of patterns and trends in market and customer behavior by advanced analytics and AI.
Transformation support
- Development of an implementation roadmap including time and resource planning.
- Skills development through supply chain training.
- Comprehensive support in day-to-day business during the implementation phase.
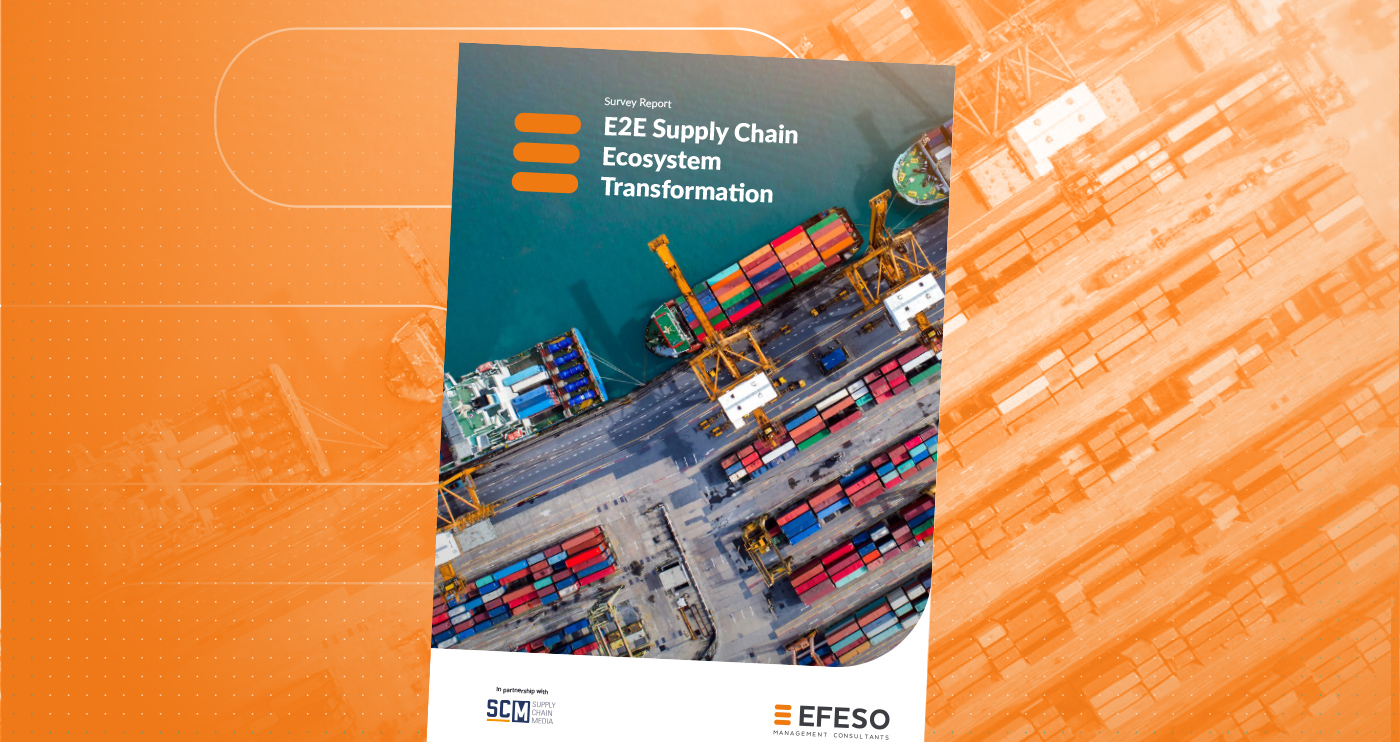
EFESO-STUDIE: E2E SUPPLY CHAIN ECOSYSTEM TRANSFORMATION
How can supply chains be transformed in times of global uncertainty? The EFESO study “E2E Supply Chain Ecosystem Transformation” shows how over 100 SCM executives are focusing on resilience, agility and digitalization until 2027 - and why looking beyond your own company is becoming a success factor.
Learn more ›
S&OP/IBP Digital Cockpit by EFESO
IT tools that visualize S&OP/IBP processes can improve the flow of information along the entire value chain. With AI support, the predictive accuracy of business-critical forecasts can also be increased.
However, to achieve valid and useful results, the right technological "adjusting screws" must first be known. For example, to be able to distinguish important process data from unimportant data, record it, analyze it and prepare it for each employee. After all, there is usually not a lack of data sources, but rather a lack of analytical expertise or technological tools to make the complexity of the masses of data manageable.
AI-based decision support
The S&OP/IBP Digital Cockpit from EFESO automatically prepares and visualizes data. This enables employees to make better decisions faster, whether in their own area of work or across teams and departments. An AI provides direct information about anomalies, deviations, and changes in ongoing business processes, creates forecasts and provides experience-based recommendations for action.
EFESO’s S&OP/IBP Digital Cockpit – features
- Central data source for all participants in the value chain.
- Drastic reduction in decision-making time.
- Customizable S&OP/IBP cycles, from monthly to daily.
- Simulation of potential future scenarios.
- Provision of details for a multidisciplinary, solution-oriented approach.
- Choice of customized data views by management level and/or functional responsibility.
- Detailed drilldowns to any level of data granularity, such as by region, product, brand and/or product group.
- Full integration of core KPIs and drivers.
Customized implementation with industry know-how
With EFESO, industrial companies successfully implement S&OP/IBP cockpits and thus improve the transparency and effectiveness of business-critical operations processes. In contrast to data science consulting, we don't just provide technical advice. We also support our customers in establishing new processes, roles, and responsibilities – also in training their employees.
EFESO services for the establishment of S&OP/IBP cockpits
- Development of a customized algorithm based on data science methods.
- Creation of a customized AI solution.
- Selection and implementation of suitable mathematical methods for customer-specific tasks and forecasts.
- Vendor-independent selection of a market solution or alternatively development of your own company solution, depending on requirements.
Fields of action for data visualization in S&OP/IBP projects
Companies should examine the extent to which data visualization can be worthwhile in four IBP dimensions - regarding demand forecasts, the demand situation within their market, their supply and inventory planning and the balancing of supply and demand. For a successful S&OP process, several conditions must be considered:
Success factors for the S&OP process
- Supply chain management orchestrates the S&OP process.
- Sales and product marketing coordinate demand planning and collect all relevant market information. Sales controlling uses the output of demand planning as input.
- Inventory, purchasing, and production planning coordinate the demand for raw materials and production capacities. Simplifications such as "Rough Cut Capacity Planning" are used.
- Strategic purchasing is also closely involved in the S&OP process and is a partner in scenario planning.
- Controlling supports selective decision-making processes based on actual figures, but not in the sense of a comprehensive P&L simulation.