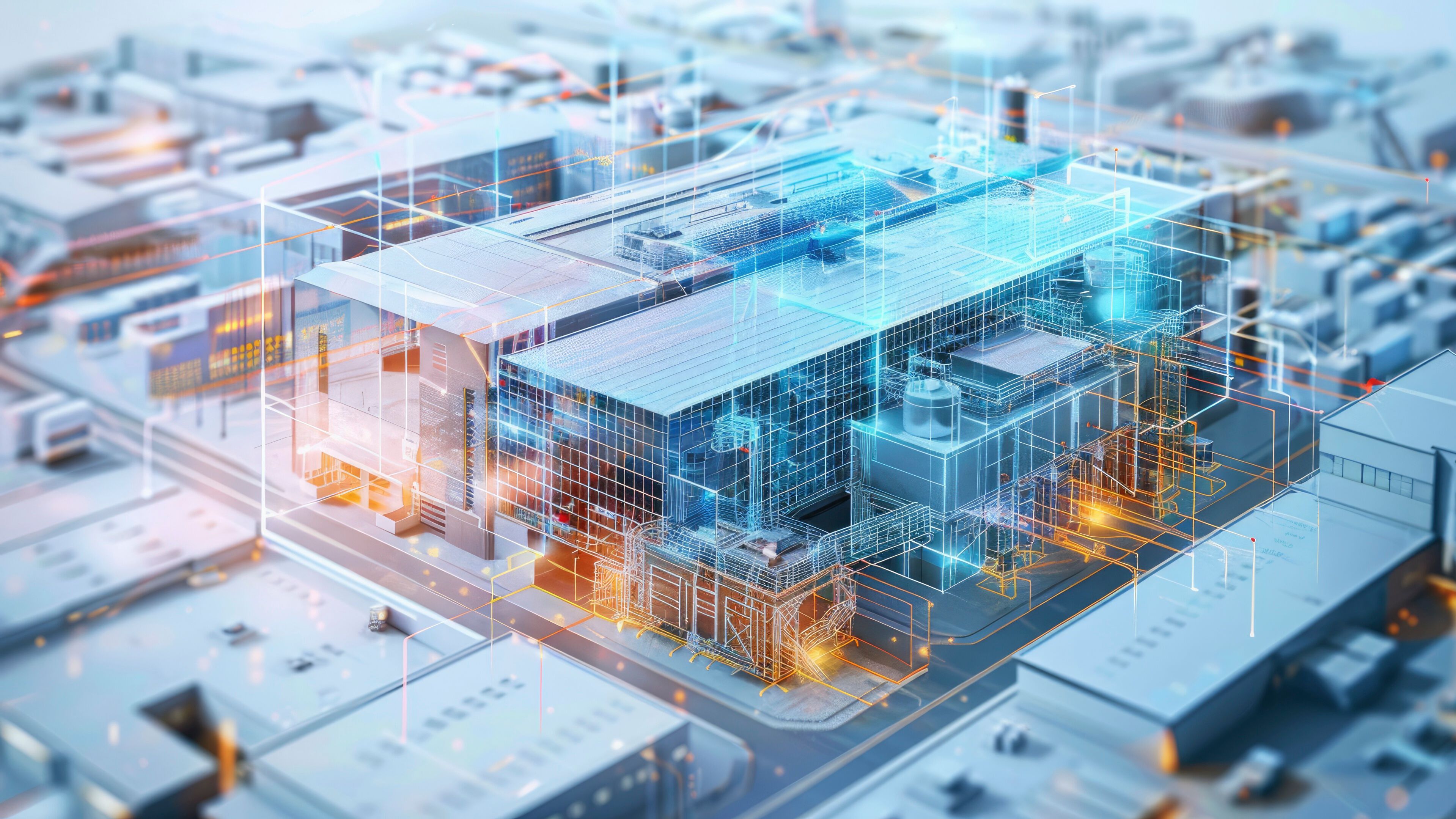
RESTART FOR GREENFIELD PLANNING
An electronics component manufacturer reassesses the design of a multi-story factory – and lays the foundation for an optimal production start in a short amount of time.
In the race to tap into future markets, time is a critical success factor. This was also the case in a project in the Middle East, where a company from the electronics industry aimed to secure a top position in a new market.
Together with EFESO, the company questioned the previously developed concept and factory layout for the greenfield construction of a new plant – and did so under extreme time pressure: construction of the foundation was already underway when the original planning concept was revised. Thanks to a focused approach and the visualization of the future factory using a digital twin of the building and its processes, the planning phase was successfully restarted.
Challenge
An electrotechnical manufacturer is expanding into an untapped market in the Middle East. Together with EFESO, the company fundamentally improves the concept and factory layout for a greenfield plant. The task force operates under an extremely tight timeframe.
MOREEFESO solution approach
With a one-stop-shop approach, EFESO integrates all planning streams. The project team also visualizes the future factory as a digital building and process twin, rapidly uncovering significant potential for improvement in space utilization, material flow design, and other key aspects.
MORELessons learned
A thorough preparation enables effective and clear decision-making under time pressure. In addition, all project stakeholders should be involved in the work of the carefully assembled project team as early as possible.
MOREEFESO success model
The one-stop-shop approach quickly revealed improvement potential in the factory layout of the new site. This allowed the company to identify planning inconsistencies early on while ensuring a clear flow of information between all project participants.
MORENew plant location to accelerate expansion
The demand for specialized electronic products for smart city applications such as energy supply, building technology, and mobility continues to grow worldwide. A manufacturer of electrotechnical products has been expanding in these and other markets for several years. With around 10,000 employees, the group is already active in the Middle East, Asia, Africa, and Europe. In response to the increasing demand for low-/high-voltage systems, e-mobility charging technologies, and other electrical engineering solutions, the company is expanding its network of plants by adding a new location in the Middle East.
As part of its greenfield project, it is building a new multi-story factory including a highly automated raw materials warehouse in an industrial city. Originally, the factory was to cover 45,000 square meters across three floors and house several production and assembly lines. A new adjacent administration building is also planned.
The company had developed a complete concept for the factory layout that appropriately addressed general production and intralogistics requirements. However, the management team identified further optimization potential in the layout planning at the right time. To make the most efficient use of all available space in the finished building for highly flexible manufacturing, the management commissioned a dedicated EFESO task force to comprehensively review all planning elements – including the building and infrastructure design as well as feasible operations and logistics processes. In this case, two specific framework conditions raised the bar for project success significantly:
- Time pressure: In October, the task force gained its first on-site impression of the status quo – but the start date for construction work had already been firmly set for January of the following year. The project kicked off while the excavation work was already underway. This left only a very limited window to implement changes to the concept. In similarly time-sensitive projects, even a tightly scheduled timeframe ranges from six to ten months, with an average of ten to twelve months being the norm.
- High-level production start: In contrast to the tight schedule, budget was not a limiting factor. To kick-off with the “best of the best” in terms of workplace design and technological equipment, the electronics manufacturer placed high value on a fast transfer of know-how from equivalent global best practice projects.
It was precisely this expertise that the EFESO team contributed: to successfully realize a project from concept development through to the implementation of optimal operations processes in the new factory.
In just four months, the task force must establish clear structures and guidelines to improve the concept.
“One-stop-shop” solution captures all planning streams
At the beginning of the project, the task force grew to around twelve members: EFESO’s experts in production, logistics, and factory design were now joined by the corresponding decision-makers from the client’s functional departments. The work packages and objectives for this joint team were defined as follows:
- Analysis and evaluation of the existing concept, including current workflows, material handling, and building design.
- Review and identification of planning inconsistencies across different value streams.
- Development and assessment of improvement alternatives with a focus on space utilization, cost impact, and process optimization.
- Design of the manufacturing concept and factory layout, along with a clear definition of site requirements.
- Identification of ideal storage systems and material supply components.
Virtual factory reveals new possibilities
To achieve the set goals within the given timeframe, the task force had to ensure a shared understanding of the spatial and design elements among all project stakeholders as early as possible.
Given the varying and often interconnected spatial and process characteristics, the team created a detailed visualization of the future factory: a digital twin of the entire building was developed, including workplace equipment and the warehouse. Based on this model, the team was able to accurately simulate all planning scenarios and assess the impact of even small changes on the workflows across production and logistics. At this early stage of the project, the simulation revealed that the available floor space did not meet the required space demand for the production volume of a key product group. The simulation demonstrated how the space requirement could be reduced from 52,000 to 45,000 square meters.
This visualization played a crucial role in enabling the task force to analyze and coordinate all planning streams – building, administration, warehousing and logistics, manufacturing processes – using a “one-stop-shop” approach with minimal interfaces. Special attention was given to the following three workstreams:
Across 45,000 virtual square meters, the team simulated precise manufacturing and logistics processes.
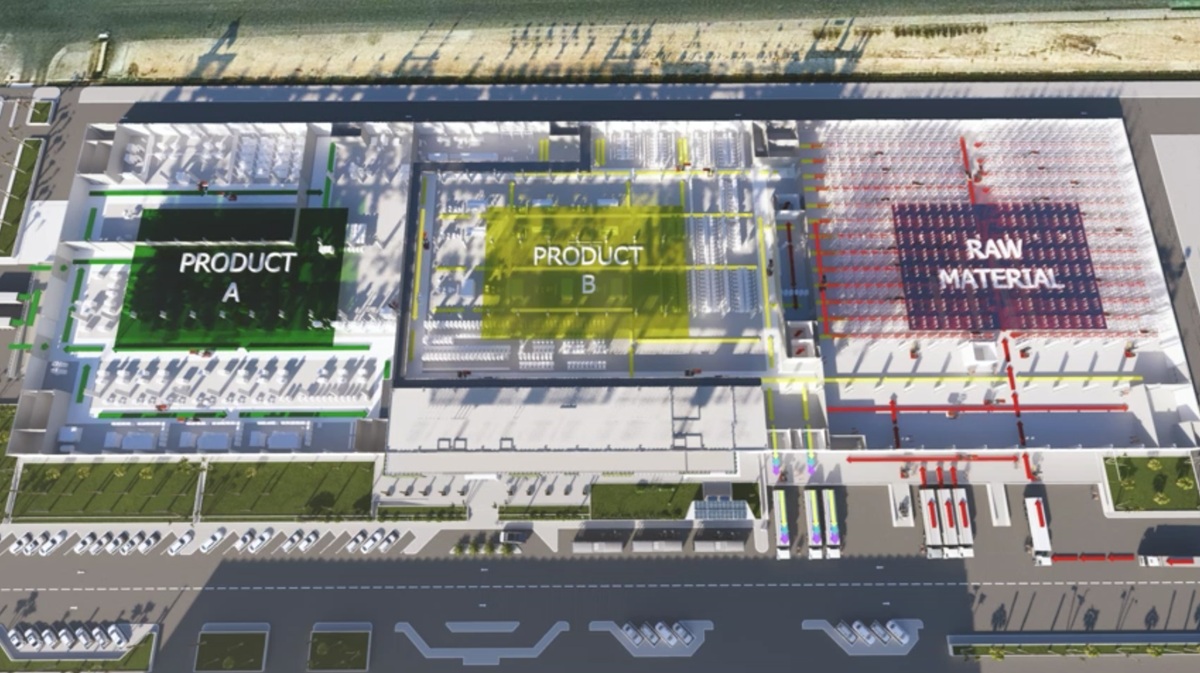
Workstream 1: Operations Excellence
- Improvement of the operations footprint.
- Identification of suitable Industry 4.0 technologies for the plant.
- Simulation of material flow to optimize the layout.
- Identification of future-oriented assembly concepts.
Key focus areas in the simulation of future operations processes:
- Mapping a comprehensive value stream design.
- Defining an intralogistics concept including modern equipment.
- Visualizing interfaces within production, e.g., for container design and machine layout adjustments.
Workstream 2: Building Excellence
- Development of energy-efficient MEP (Mechanical, Electrical and Plumbing) concepts.
- Designing a sustainable building in line with ESG requirements.
- Creation of a flexible and modular building layout.
- Focus on CapEx-optimized (Capital Expenditure) solutions.
Key focus areas in the simulation of future operations processes:
- Requirements for the building, such as floor slabs, sprinkler systems, etc.
- Infrastructure requirements.
- Characteristics and load capacity of the electrical grid.
- Compliance with energy efficiency and sustainability standards.
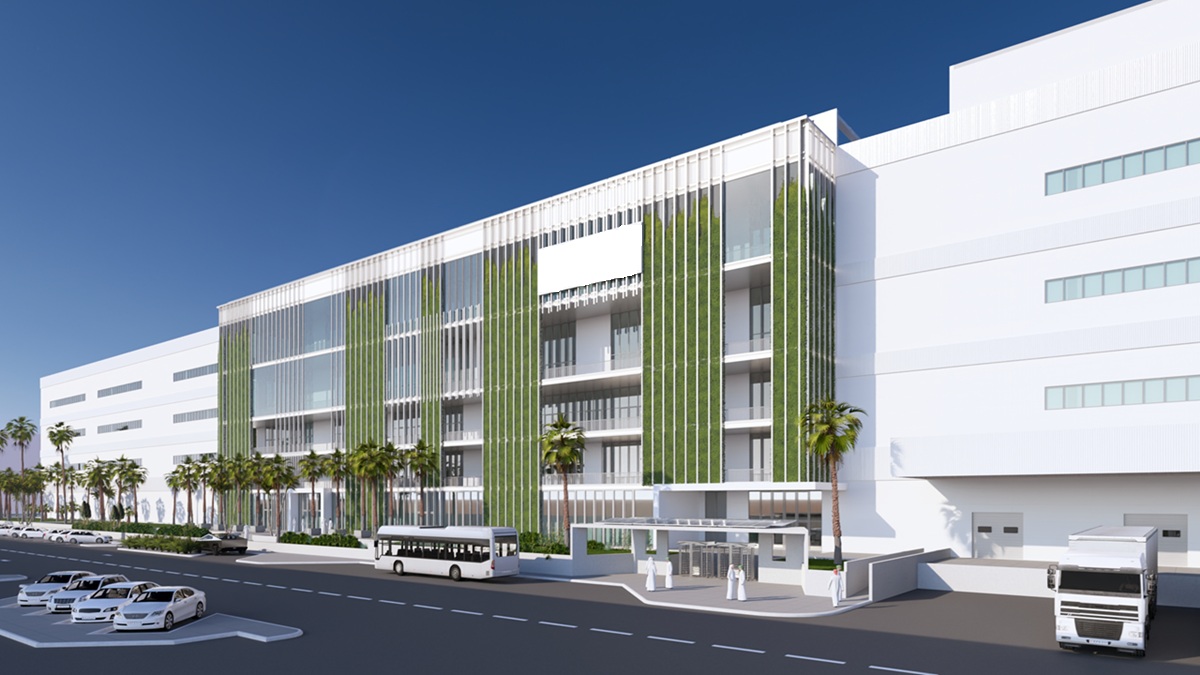
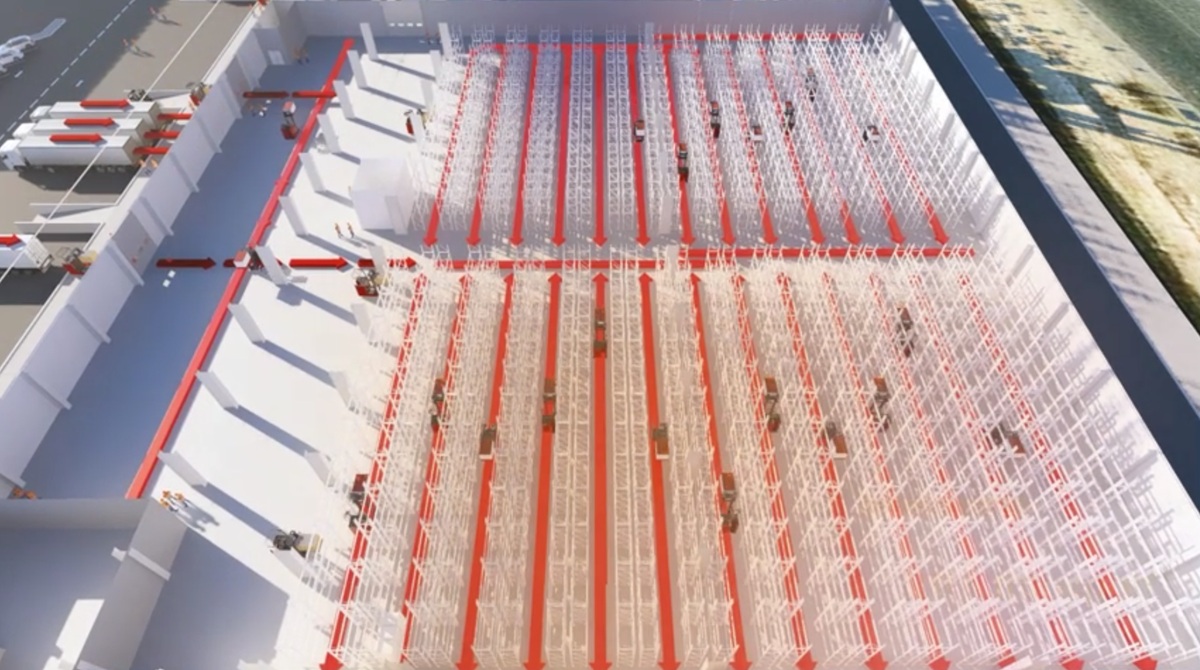
Workstream 3: Warehouse Excellence
- Identification of needs-based and CapEx-optimized warehouse technology
- Development of a hybrid material distribution system to ensure high flexibility in the face of change
- Integration of these elements into the overall production concept
Key focus areas in the simulation of future operations processes:
- Visualization of the logistics concept and selected technologies
- Mapping and verification of infrastructure requirements
- Visualization of the interfaces between building, infrastructure, and production
Fast and effective action thanks to thorough preparation
The following aspects proved to be critical success factors in the implementation of the project:
Empower project management to make clear decisions – from day one!
Making effective decisions – especially under time pressure – requires thorough preparation and the ability to quickly process consistent and comprehensive information. This should be supported by a valid data and information analysis. Sketching out scenarios is particularly helpful, as it shifts the discussion from abstract concepts to specific actions. In addition, clear priorities and decision-making criteria must be defined in order to act swiftly and with purpose.
Assemble the ideal team!
Even with an ambitious timeline, it is well worth investing the time to put together the right team of experienced professionals. A well-casted team can respond quickly to unexpected challenges, develop creative solutions, and ensure that project tasks or problem areas are handled efficiently and successfully.
Get all stakeholders on board!
All project participants should be involved in the task force or project team’s work as early as possible. Clear communication and the inclusion of relevant teams and stakeholders promote understanding and acceptance of decisions. This can be achieved through regular meetings and updates, as well as by establishing feedback loops. Early and continuous collaboration with key parties also ensures that everyone pulls in the same direction and pursues shared goals.
At three best-practice sites in Europe, employees gained inspiration for the factory design.
Knowledge transfer during plant tours
With its one-stop-shop approach, the project task force quickly identified improvement potential in the factory layout of the new site. It uncovered planning inconsistencies and, by acting as the sole point of coordination, ensured a clear flow of information among all project stakeholders. This approach prevented discrepancies during further construction phases that could have led to inefficiencies or increased costs.
Another key success factor for the continuation of the project beyond the planning phase was a "best practice tour" conducted by the task force. Within just a few days, they visited three manufacturing sites in Europe, where employees of the electronics manufacturer experienced exemplary production and logistics processes in action.