PROGNOSTIC RELIABILITY WITH HUMAN AI
How Artificial Intelligence and Gamification empower a global, agile Industry 4.0 supply chain.
There are not many comparable industrial products whose smallest components are measured in the order of nanometers. On a semiconductor component, for example, a single "cube" that provides on and off switching is placed a million times. Each cube is lithographically structured and etched from layers of copper, aluminum and silicon oxide. In addition to other logic units, this creates a microcontroller that performs control functions in electronic products.
Components that can easily be hidden behind a human hair are thus in a league of their own in a global value chain. In addition, semiconductor solutions from Infineon are now essential in many products around the world, especially in the automotive and consumer goods industries. Responsive supply chain management is necessary to meet the following challenges: In addition to high capital requirements for equipment and fabs, intrinsically long manufacturing lead times, and high demand volatility, there is also the short life cycle of products with semiconductors, as the next semiconductor already enables better products. Our global team of a thousand employees with a smart Industry 4.0 supply chain solution that is continuously being developed masters this.
Our supply chain business ecosystem is based on physical make flexibility and its daily optimization in a highly automated planning process. To further increase the performance of our Industry 4.0 supply chain solution in these areas, we have launched digitalization projects that guarantee better forecasting and higher flexibility
Digitization in two directions
The projects pursued two digitization initiatives: "Digitization for Input" focused on demand-oriented aspects. In addition to the optimal use of available data, the focus here was on employee competence and change management for the implementation of measures, as well as a gamification approach for the integration of AI-supported planning.
At the same time, "Digitalization for Execution" should create the infrastructure for a global, flexible, virtual factory, further establish automation in the company and improve responsiveness to a changing order situation on a daily basis in the global production network.
This approach enabled us to further expand our supply chain as a competitive advantage and, at the same time, to bundle the empirical values from our sites, for example on Big Data analyses in manufacturing or in the traceability of errors in quality management. The following elements proved to be particularly important for the success of our Industry 4.0 solution:
COB (Customer Order Behavior)
Our project team visualizes the ordering behavior of customers in heat maps on a weekly basis over a period of 26 weeks. The two-dimensional representation generates images that experts can use to assign predefined categories (e.g., over- or under-scheduling) to customers. Once a sufficient number of such images have been assigned (labeled), this assignment can be passed to a deep learning (DL) machine. This enables a reliable and fast analysis of the customer's ordering behavior, which in turn allows a better understanding of the customer's needs and allows changes in ordering behavior to be identified.
DFC 4.0 (Demand Forecaster 4.0)
A forecast accuracy that is better by machine than by human is implemented in the DFC 4.0. The DFC 4.0 uses historical time series data and "future data" and works with a mix of statistical and DL/KI tools optimized for the best forecast accuracy for the individual product.
HAI Game trains interactions between humans and software
In order to support change management during the introduction of DFC 4.0, we use two tools: in regular so-called espresso mails, a member of the management team introduces certain functions of DFC 4.0 and their advantages, and offers employees the opportunity to obtain further information on the subject via videos, articles, etc.
In addition, we developed a game with HAI (Human & Artificial Intelligence) to improve the collaboration with our "digital colleagues" in a playful way. Although an AI usually delivers better forecasts very quickly than humans, it cannot explain them and is occasionally grossly wrong if information is missing. In a half-hour game of 20 rounds, you learn to trust the machine quickly - without intervening - because the AI simply usually "forecasts" better than the player, who also sees the time series and could predict for himself. But why bother if the AI is better? This applies both in the case when you are in your "comfort zone", but also when you have more information as an employee and can therefore make your own forecast. An “aha moment” comes at the end: Here you learn how many savings you could have made for the company if you had relied on the information provided by AI on the one hand, on the other hand it is also important to do the calculation yourself (and then accurately) in certain situations.
Global supply chain as a virtual factory with GPN (Global Production Network)
Global supply chain planning generates a daily ATP (available-to-promise) from tens of thousands of demand elements and thousands of global bottlenecks. It considers on a product-by-product basis what is available in the distribution center or will arrive there on a daily basis. This ATP is then in turn used daily by around one million order elements to either confirm or improve on the previous day's commitment. Improve here means to commit closer to the customer's desired date than the day before. This "best of breed" IT tool of a supply chain planning and execution system, which has been in place for years, was complemented by the GPN in our digitalization project. The GPN provides a holistic view of production, quality control and material allocation across the entire supply chain. The delivery or use of faulty lots can now be stopped globally within minutes, for example.
The fact that the combination of these technologies and measures is bearing fruit can be seen in all the areas mentioned: The complete traceability of goods or products from the front end to the back end in the GPN also reduces errors due to manual handling and achieves significant savings. In addition, supply chain planning with the GPN improves physical flexibility and thus overall capacity utilization by several percentage points.
To solve the global chip shortage, however, it is not enough for only the semiconductor supply chain to work; the semiconductor supply chain must also work seamlessly. Just-in-time methods that operate with minimal inventory and control replenishment by range will not work in pandemic situations when there are partners like the semiconductor industry that cannot further reduce its intrinsically long lead time of up to six months for a component despite 365/24. With range of coverage control, replenishment is only initiated when the stock falls below a certain range. Example: If stock is 1,000 and requirements are 500, the range of coverage is 1,000/500 = 2 (for example, two weeks). If the demand then drops to 250, the range of coverage is four weeks and nothing is ordered for two weeks - and the bullwhip effect (i.e. the amplification of fluctuations along the supply chain) is already created. In the SCM working group of the ZVEI, which is headed by Infineon, there are already good approaches on how to get a sustainable grip on this problem and the bullwhip effect.
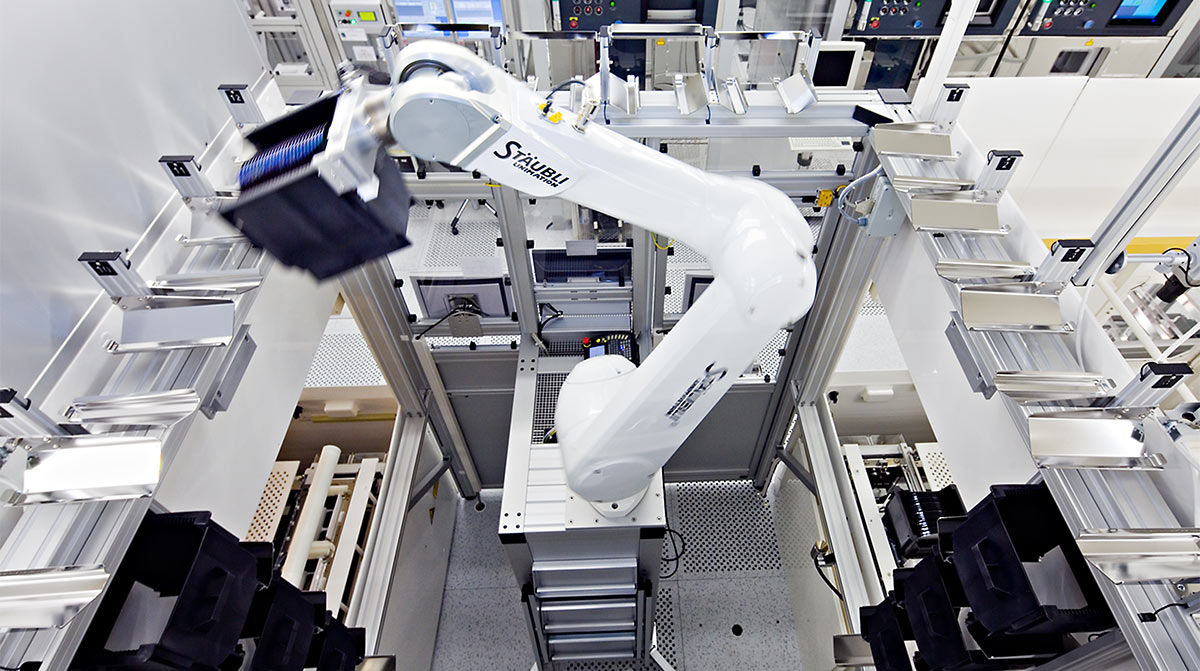
Field of application: High-tech/electronics industry
Challenge
Further develop an Industry 4.0 supply chain solution via digitalization initiatives to strengthen the company's resilience to volatility and order fluctuations
Solution
Combination of smart technologies that address improvements in several areas of action in the global supply chain, especially in customer-oriented demand planning and through physical flexibility that is optimally utilized on a daily basis through planning tools; improvement of customer order commitments