(Kopie 1)
Warning Signals in the Management Cockpit
How e-mobility is altering the balance of power in the automotive industry
By Michael Jung, Member of the Management Board, ROI Management Consulting AG
As the automobile has evolved, one small detail has remained unchanged for decades: the ominous red glow of the warning cockpit light signaling possible engine damage. Although carelessly underestimated by those not in the know, the oil warning light is considered equally prophetic. Ignoring its signal sets off a disastrous chain reaction. No oil pressure means no piston lubrication, which leads to piston seizure and, in turn, serious engine damage.
But the days of this horror scenario seem numbered, provided the all-electric drive variant actually prevails in automobile production over the medium or long term. This is because an electric powertrain eliminates the highly complex constituent parts of the combustion engine. Besides the engine housing, many other system components set for redundancy include all those used for the air intake, fuel supply, ignition and lubrication. They will be replaced by an electric motor and drivetrain; alongside new components like the battery and charging system, power electronics and special air-conditioning / heating systems (see diagram pp. 5) totaling around 210 parts. This represents a huge reduction in complexity compared to the average combustion engine and its 1,400 or so parts.
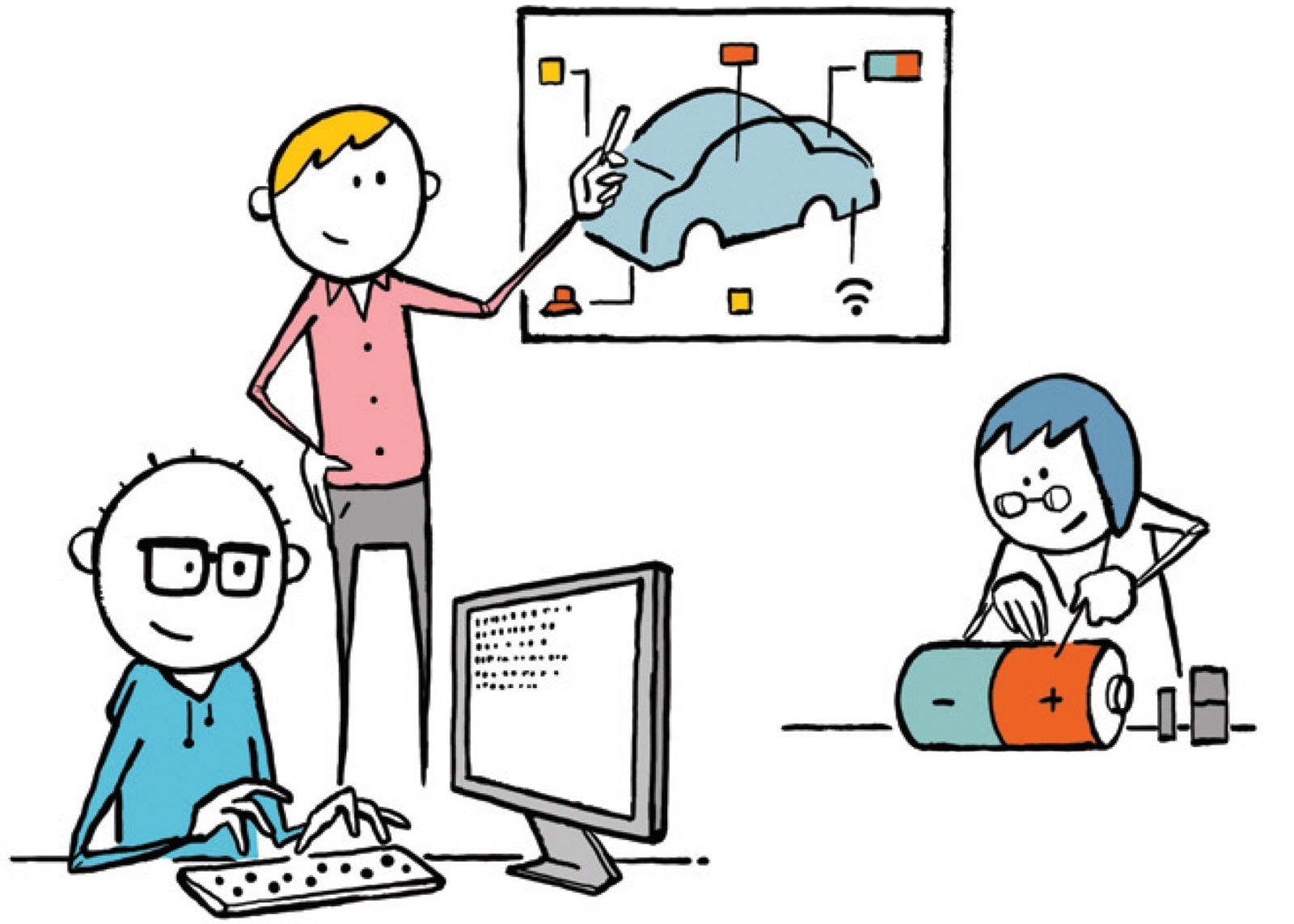
This development marks a decisive watershed for the automotive industry, which to date has been able to adapt technological innovations and customer requirements within the relatively clear framework of the development cycles of their model ranges. The vehicle life cycle – from development and production to use and ultimate disposal – will be turned on its head (see diagram p. 7) and with it, the corresponding value chain structures and power relationships that have been fostered for over a century. Changes in the following three areas will hit particularly hard: the supplier structure; the manufacturer / supplier relationship; and the development of new IT- and software-driven competences in R&D.
Suppliers: Specialists under pressure
In recent years, many automotive suppliers faced few electromobility and innovation challenges, given the sluggish market demand for all-electric vehicles as well as the willingness of their customers to make any significant change to their model preferences in favor of this drive variant. Innovations were instead applied in areas such as “downsizing”, i.e. boosting the efficiency of the traditional combustion engine, which even resulted in sales growth for a number of engine manufacturers and engine-related suppliers. However, this focus on improving an existing product is what poses a considerable risk in the medium to long term. This is because specialist suppliers in particular will come under extreme pressure if the share of all-electric vehicles increases significantly, as industry experts predict, between 2020 and 2040. If they fail to devise alternatives to products like camshafts, turbochargers and fuel injection pumps, their business will shrink substantially or even vanish. However, forecasts setting out the concrete developments the German automotive supply industry should actually expect have fluctuated between two extremes for years. While one camp sees thousands of jobs at risk and bemoans the head start of Asian rivals in battery technology, other market studies conjure up visions new jobs opportunities emerging in the manufacture of new e-components.
One thing is certain: a reduction in complexity will hit employment prospects in car manufacturing. Some of the new components could generate significant market volume, like the “electric machine” at the core of the electrified powertrain. The report “Strukturstudie BWe MOBIL 2015” forecast market volume growth for this component alone to almost 21 billion euros by 2025 and at least 38 billion euros by 2030 compared to 2013. The principal drivers here could be increasing hybridization and the growing proportion of battery-powered vehicles in global sales (cf. Strukturstudie BWe MOBIL 2015, p. 55). The example also clearly illustrates that structural change in the automotive supply industry will not happen overnight but in gradual stages. Production and assembly plans already exist for the highly relevant parts of the value chain of the electric machine – but efficiency in implementing low-cost production still needs to be improved.
“Employment prospects in car manufacturing will be impacted by a reduction in complexity.”
Michael Jung
E-Cooperation: A Shift in the Value Chain
From the car-buyer’s perspective, e-models may still have something exotic about them – but attitudes within the automotive industry towards the electric powertrain have already transformed since batteries have become ever more economical and better-performing. The example of Tesla in particular shows how all-electric cars can be developed, manufactured and sold for a mass market. The electrification of the powertrain thus looks set to shift the goalposts considerably in the value chain between car manufacturers and suppliers. While the relationship between OEM and supplier for the combustion engine was on a clear “buyer-seller” basis, car manufacturers can now choose between two strategies: a) consolidate development competence in electric drive systems in house, or b) buy in all the components from suppliers and focus on system integration.
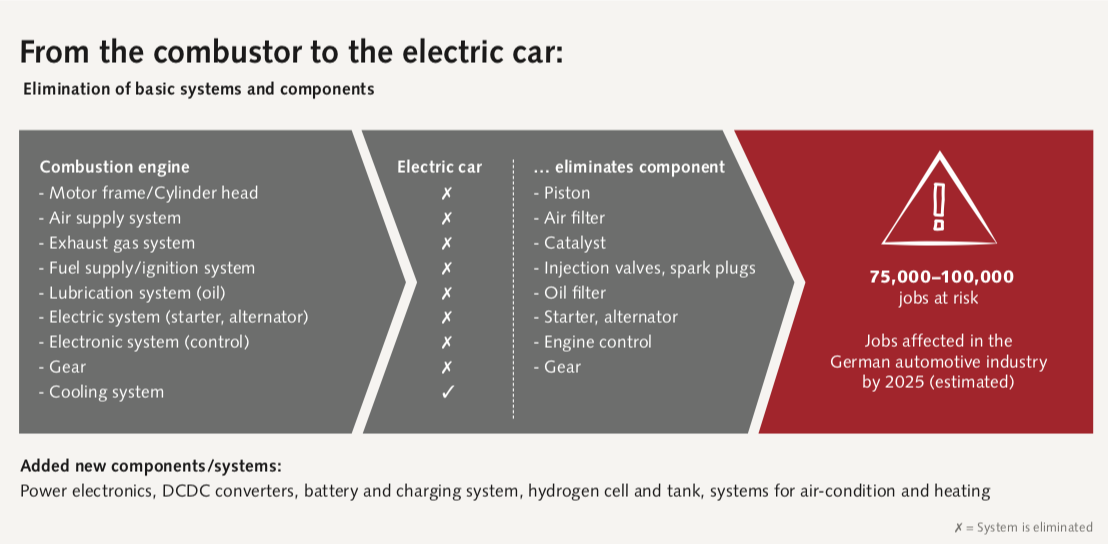
Software instead of Self-ignition: New R&D Competences
Apple’s vision of the “iCar” should in no way be dismissed as a minor incident in the history of the automobile, where the IT company experienced temporary delusions of grandeur or flights of fancy. In fact, it is not a question of whether a Silicon Valley giant like Apple can produce its own car but at what point it actually wishes to do so. At the end of the day, established OEMs like VW already manufacture their car models on the modular principle. Just as for mobile phones or computers, they order components, assemble everything in house and then handle marketing – a business that can be run with about 25 percent of in-house value added. Enhancing the combustion engine with hybrid technologies or replacing it long term with an electrified powertrain will make it easier for new entrants from outside the industry to take up car manufacturing.
This has several implications for automotive suppliers. They can share in this development of competence, for example, by developing partnerships and commit themselves to their previous customers on the manufacturer side in the process. Long term, however, carmakers may follow the General Motors example and build up their own inhouse competences for batteries and electric motors to enhance their independence. GM has been investing considerable sums in inhouse battery and electric motor production for seven years, the fruit of which has been between 58 and 158 electric vehicles a day produced in Detroit, depending on demand, some of which already have a range of up to 500 kilometers.
Whatever happens, automotive suppliers need a “plan B” to avoid becoming over-dependent on the electromobility strategy of their OEM customers, i.e. cooperative partnerships with battery producers and mechanical and plant engineering companies. Targeting not only reciprocal knowledge transfer but also the development of common products and services relating to the electric powertrain, with a special USP enhancing their appeal as a longterm partner for OEMs based on this “e-competence”.
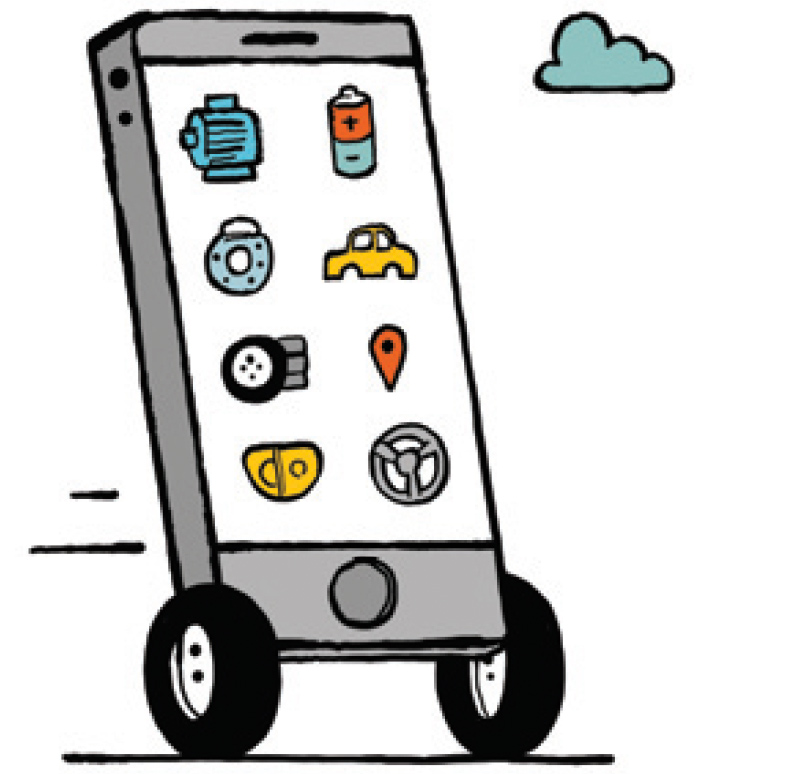
“The all-electric vehicle has more in common with a smartphone than a conventional car.”
Michael Jung
Furthermore, the automotive industry is already competing with the IT sector for the best candidates, especially IT and electrical engineering specialists. A situation which will further intensify for OEM and supplier R&D departments over the next few years given that electronics and software are continuing to merge, for example for (semi-)autonomous cars, which require sensor technology from the electronics field and software to process the captured data. This is why the all-electric vehicle in particular has more in common – at least in development engineering terms – with a smartphone than a conventional car. The software-controlled management of power consumption in elements ranging from infotainment and driver assistance systems to heating, lighting, etc, in combination with progress in battery technologies, is what will underpin success in range and performance and thus boost the appeal of the vehicle for end customers. The automotive industry must quickly realize that it is in competition with the IT sector when it comes to recruitment – and must now launch and fund university and training initiatives to meet the demand for technical specialists. Anyone ignoring these developments is in danger of seeing their business model come to a clunking halt.
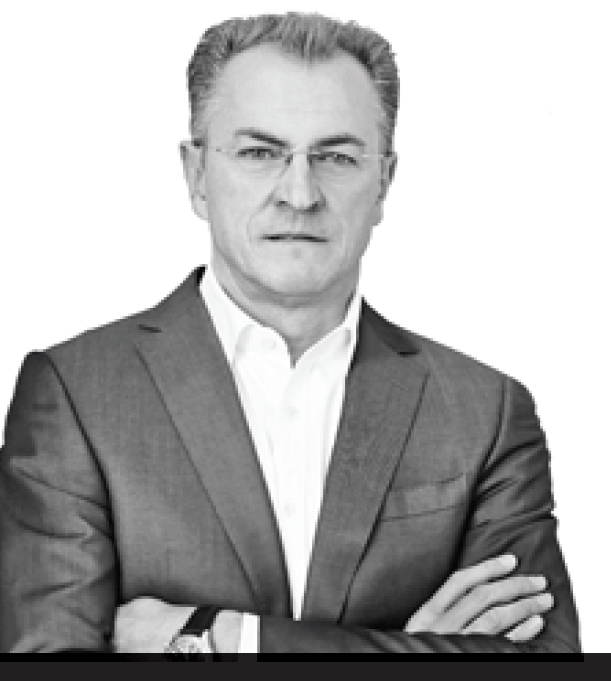