FROM SCAN TO AWARD - THE PERFORMANCE BUNDESLIGA
In order to prepare the component plants of its German manufacturing network for competition from external suppliers, the Group planned to introduce a comprehensive efficiency program aimed at continuously improving productivity and quality in a total of nine German factories. To this end, ROI not only determined the current performance status of the individual locations, but also made it the basis of a unique competition:
In a kind of “Performance Bundesliga”, the component plants competed in five predefined evaluation categories, such as plant and assembly efficiency. Each plant had to enter a certain number of lines and areas. The absolute and relative improvements on these lines were then measured over six months. The plants with the largest development leaps are the gold, silver and bronze winners within the category.
The main prerequisite for this form of internal competition was comparability between the different locations. To this end, a uniform calculation logic for the basic key figures was defined in advance. In addition, a scan specially developed by ROI for each category was used to record the methodological competence.
The data obtained in this way was published in all plants as in a Bundesliga table. The employees responded very positively to this competition, so that the idea quickly developed with great dynamism and yielded successes. After only a short time, there were significant improvements in productivity in assembly as well as in logistics and maintenance. In order to promote not only the idea of competition, but also mutual learning, ROI organized additional networking events and introduced a special category “Networking” in the competition, which took into account knowledge transfer and best practice sharing.
The translation of the standardized assessments into an internal competition provided for an unprecedented dynamization of the rigid plant structures and work routines. The program is currently being expanded at an international level in the third round with a total of 25 plants. The Performance Bundesliga will thus become the Performance Champion’s League.
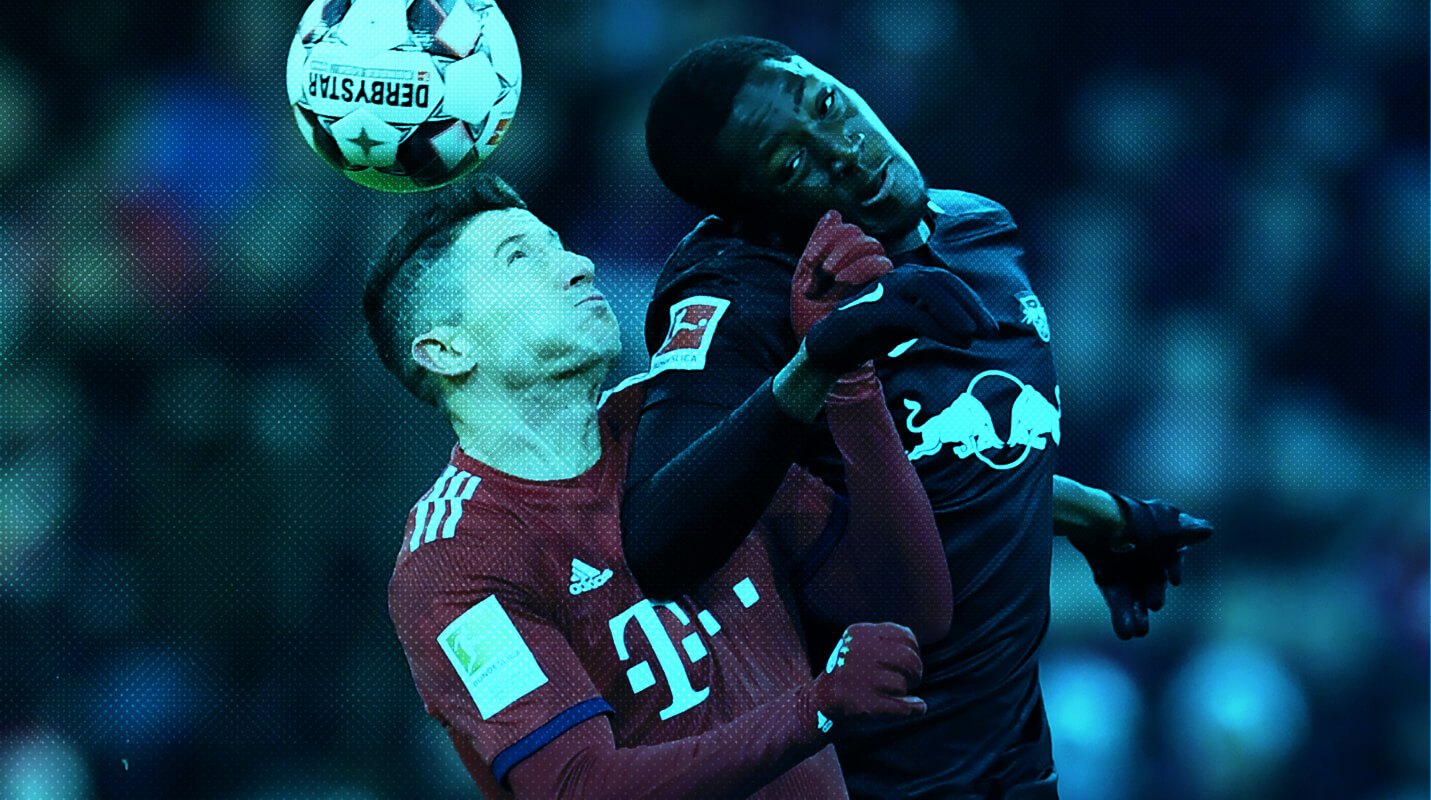
MODULE 2: STRATEGY ALIGNMENT AND TARGET IMAGE
The chicken or the egg?
Numerous lean initiatives fail even before they have started in the company. The reason: unrealistic target images, a lack of linkage with the corporate strategy or an incomplete picture of the value-adding activities in the company.
However, how sustainable and holistic Lean Manufacturing is introduced and implemented in a company depends primarily on where the starting point for the planning of Lean measures lies: Is it just a matter of achieving a certain result, such as a cost target, with the help of lean tools?
Or is the focus on the process itself, the improvement of which is intended to achieve sustainable further development of the entire manufacturing system? This chicken-and-egg problem is decisive for whether lean manufacturing is merely seen as an instrument or toolset or whether it is understood as a management approach leading to action.
Three elements are therefore decisive in ensuring optimal target picture development:
Strategy alignment
Lean projects should not only be oriented towards short-term key performance indicators, but should also be in line with corporate strategy and market requirements. Goals, requirements and framework conditions must therefore be derived in a systematic strategy comparison from the corporate and manufacturing strategy and translated into concrete lean principles.
Target image development
From these strategic requirements, a target image is then developed in the sense of a future state, which provides information about the structure of the value stream, the lean, technology and digital concepts used, the integration of the indirect areas, organization and management systems as well as qualification requirements. They are derived from the previously defined strategic requirements of the market. If, for example, the company has to move faster towards the market, this means a shortening of throughput times; if the ability to deliver is to be increased, this requires measures in the area of quality.
Management attention
In addition, it is crucial in this phase to create the necessary conditions for the implementation of the Lean project at management level. This involves first of all generating attention for the lean initiative and attracting supporters at decision-maker level. In addition, lean and digital initial training for upper and middle management to ensure the sustainable anchoring of the lean concept across all hierarchical levels in the company.
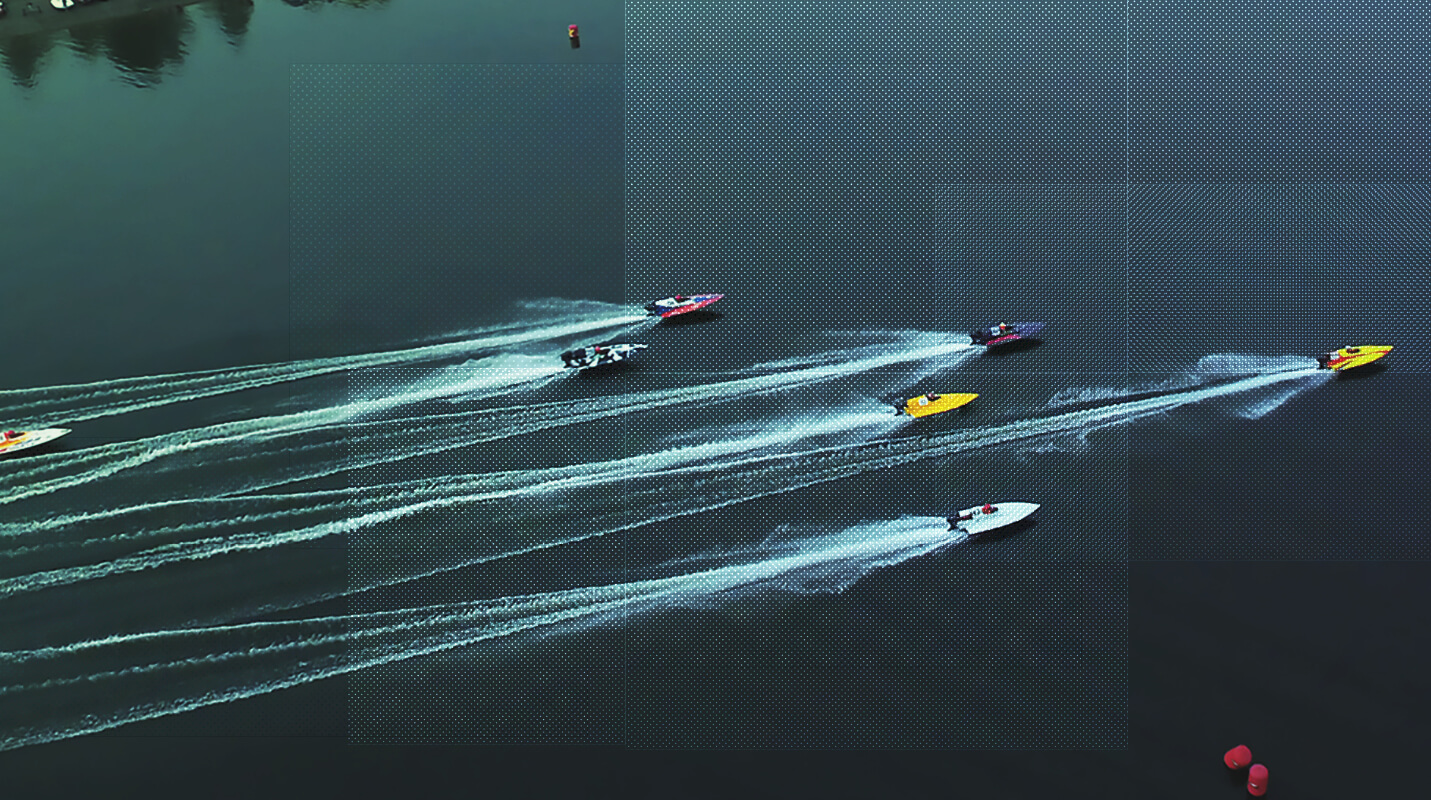
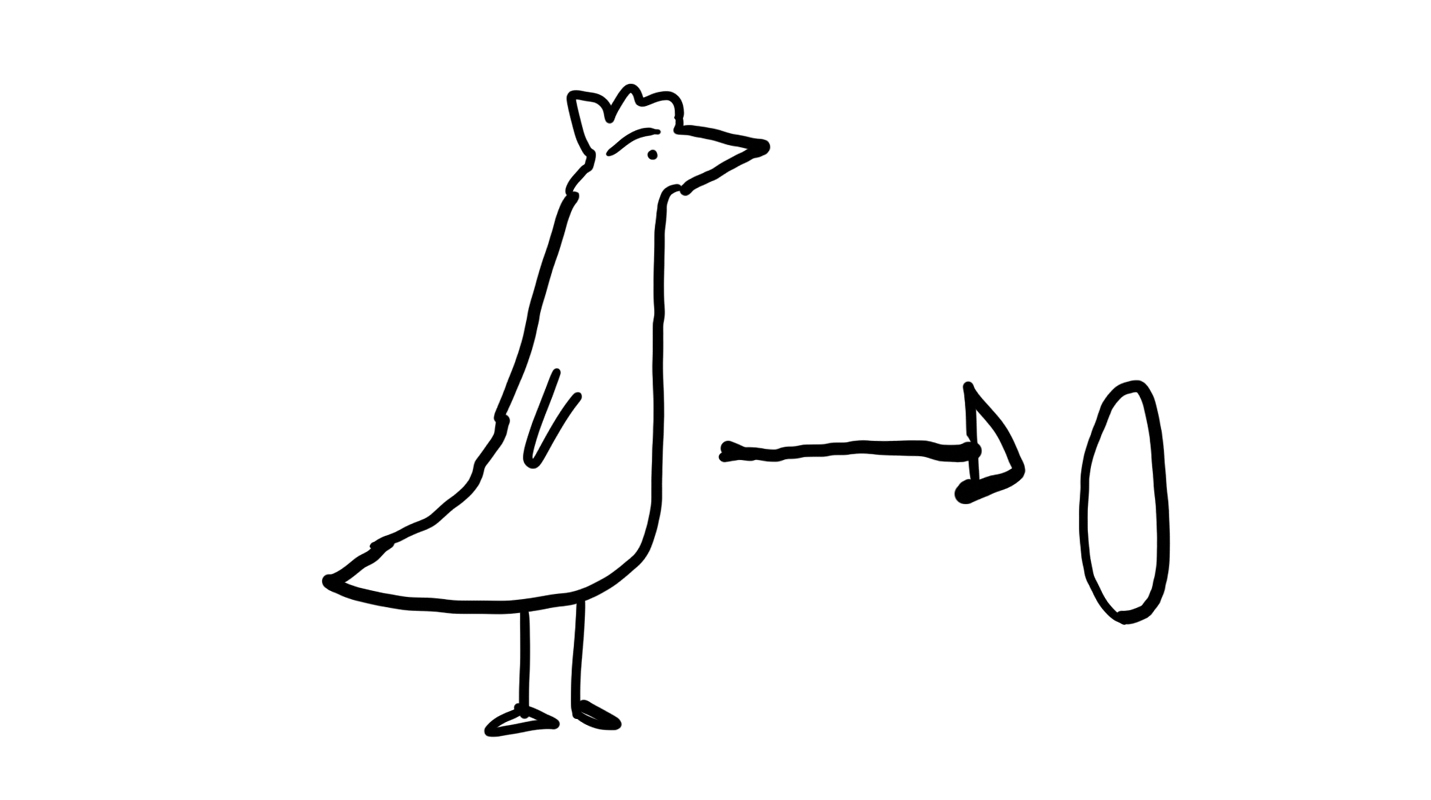