FIELDS OF ACTION FOR THE DATA AGE
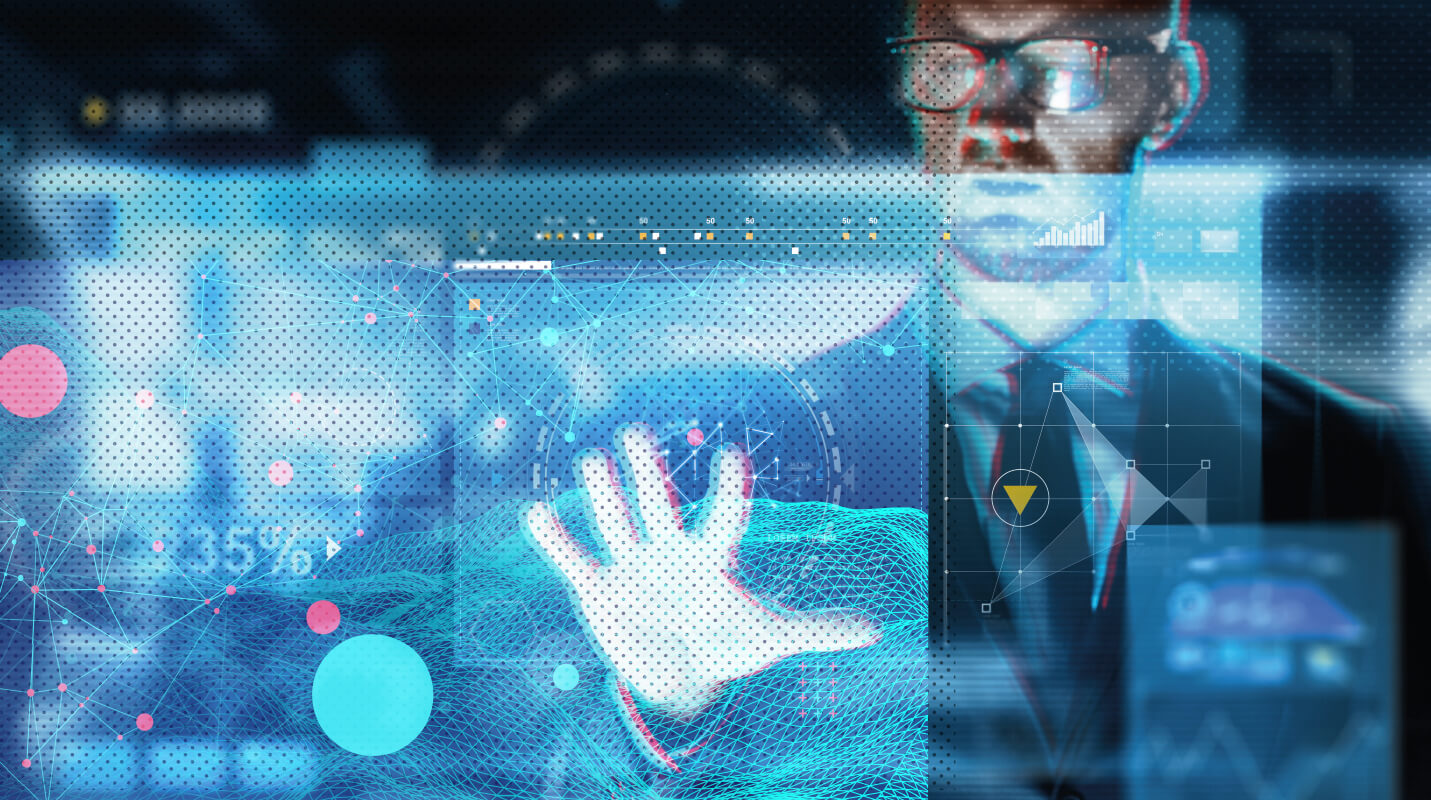
THE TRIUMPHANT MARCH OF ANALYTICS TOOLS, IIOT PLATFORMS AND AI SOLUTIONS HAS BEGUN.
But what exactly does the industry‘s entr y into the data age mean? Which developments will be par ticularly formative in the coming years and generate the greatest pressure to adapt? We have compiled ten fields of action that companies will have to deal with.
1. GLASS BEADS
THE ESCALATION OF TRANSPARENCY
Optimisation processes can only be initiated if there is comprehensive clarity about the state of the production network. In supply chain risk management, access to all relevant indicators at the meta, macro and micro levels can lead to a significant increase in forecasting accuracy and also to the potential disruptions in the supply chain being identified at a very early stage - if the data from the entire supply chain is available. The use of data analytics tools helps here in particular to define early indicators and integrate them into an overall picture that enables cross-company optimisation.
However, this development has a dark side. Because “cross-company” also means that the upstream partners in the value chain must lower their protective shields to a very high degree and grant their customers insights into their processes.
The interest in turning the supply chain into a string of transparent glass beads decreases the further down you go in this chain - for understandable reasons. Because the transparency created in the context of digitalisation exacerbates the already existing power differentials - which in turn are brought into play when transparency is created.
Can the tension between the optimisation potential that can be raised for all partners and the concern about exposing oneself too much to the customers be resolved? Finding convincing answers to this question is one of the most important tasks of the coming years.
2. THRUST REVERSAL
THE NEW DIRECTION OF INFORMATION FLOWS
Factors such as data availability and the use of AI tools have a direct impact on management structures in companies. This affects both established management routines and daily interaction. The main reason for this lies in changed framework conditions: Information and knowledge are no longer the exclusive knowledge of a few managers and experts. Rather, they are omnipresent in the organisation and can be accessed by anyone at any time on any device.
This changed structure leads to a change in the direction of communication and information cascading. Impulses for problem identification and for problem-solving sprints come from the team. In particular, the use of AI-supported analytics tools helps to identify weak points very effectively. However, this reversal of thrust does not mean that expert and management roles lose their relevance. After all, information is initially only a description of the problem. Background knowledge and process expertise are still indispensable, as is the ability to prioritise issues. New expert knowledge is also required, for example on the deep interpretation of data. And finally, original management tasks are still critical: Focusing on the goal, taking responsibility for results and decision risk, orchestrating and motivating the team. So the data economy is not turning corporate structures upside down. But it does change the nature of communication and process design in a serious way and therefore requires new leadership and management techniques.
3. VELVET REVOLUTION
THE SENSORISATION OF THE VALUE CHAIN
The ability to ensure comprehensive connectivity and networking within production, to acquire more and more data and to interpret it using AI, opens up completely new efficiency and risk management potential. This development is gradually changing our entire perspective on industrial value creation - what we perceive as evolution today will very likely appear as a revolution in retrospect. However, AI solutions can only have their effect if they have data - and far beyond their own company, all the way to the digital synchronisation of the entire value chain and the integration of all functional areas. This type of networking, however, requires very profound networking of sensor technology - so that it is recognisable throughout the entire chain if, for example, a critical production line at a supplier could become a bottleneck. With a shared, cloud-based data reservoir and an integrated data model, such early indicators can be used to detect potential problems in real time using AI.
An exciting future perspective is the use of semantic interpretations, so that even unstructured information can be automatically evaluated and used for qualitative forecasts. For example, the knowledge filtered out from social media that part of a supplier’s team is flirting with switching to the competition can lead to appropriate risk measures being taken. However, the hurdles here are not primarily of a technological nature. This is because comprehensive sensorisation of the value chain requires a governance model that is trustworthy for all partners involved and that protects against both (power) abuse and external attacks.
4. INFINITE LOOP
PRODUCT DESIGN IN DIGITAL ECOSYSTEMS
In terms of the total product life cycle, manufacturing is only the executive, accounting for about one-third of the costs. Engineering and design phases contribute the rest. Errors and deficiencies that are already inherent in the product design have a disproportionate impact on production costs and can only be corrected at a later date with great effort. For decades, people have therefore been working on digitalising product development and exploiting more and more simulation possibilities. The path leads from a two-dimensional drawing to virtual crash tests. But the exponentially increasing availability of computing and storage capacities, access to more and more data and the power of AI and analytics tools offer completely new possibilities for simulation and prognosis.
Product behaviour, life cycles and, above all, the performance of products in the market can be mapped by digital product twins. Algorithms help to understand which usage scenarios lead to failures and errors, which product features are particularly successful, and in which areas an overload occurs. Which product features are particularly successful, and in which areas overengineering can be prevented. The structures and patterns that are recognised over the entire life cycle can flow directly into the further development of the products and prevent cost drivers and quality problems. Product design thus becomes a cluster in a recursive control loop supported by AI and analytics - and changes the perspective on the entire manufacturing process.
5. DECODING THE MATRIX
POTENTIALS OF THE SEMANTIC WEB
The more data available, the better AI solutions work and the faster insights can be gained. But where does this urgently needed information come from? The data-driven economy requires access to heterogeneous, unconventional sources - only then can processes be substantially accelerated. What is needed is data from the market - from customers, suppliers, competitors, research institutions and potential users. In this way, valuable experience can be incorporated, mistakes do not have to be made more than once and some wheels do not have to be invented twice.
However, a large part of the data needed for this is not in structured databases with standardised interfaces and authentication concepts - especially not if you want to recognise trends at an early stage. Rather, this data is not available at all - it flows through threads in social media, posts on community boards, communication platforms, publications in magazines and blogs. The automated perception of such signals requires the use of intelligent solutions and filtering algorithms based on semantic web technologies that detect with high sensitivity when signals combine to form relevant patterns and flows.
The ability to use the semantic web effectively and creatively will become one of the most important levers in the coming years to differentiate oneself from the competition and to develop business models quickly and effectively. It goes without saying that companies that have gained early experience with the use of corresponding logics and tools over many years and are particularly good at exploiting the potential of the solutions will have a strong advantage.
6. PROCESS ENGINEER 4.0
DATA COMPETENCE AS BASIC KNOWLEDGE
Profound changes in the Smart Factory are also reflected in the communication between companies. The exchange of process- relevant information and documents via traditional EDI solutions is reaching its limits for various reasons. On the one hand, an integration of IT between the value creation partners causes high harmonisation efforts. On the other hand, with the current status quo of technologies, a full digital integration of the IT worlds is enormously costly.
Blockchain technology and its core application, smart contracts, offer a way out. These are programmable scripts that ensure the automated flow of business logic across company boundaries, control partner interactions and document them in a forgery-proof manner, as well as manage data access rights. The use of quickly implementable and scalable smart contracts thus reduces the costs of data exchange, optimises tracking and data transfer, for example in order entry, and creates the basis for new, token-based business models such as pay-per-use. The first resilient experiences gained with the use of blockchain technology also show that smart contracts can provide benefits not only between the individual partners in the supply chain. More and more companies are discovering valuable application possibilities within their own production landscape as well.
7. DATA VALUE
INFORMATION AS AN INDUSTRIAL PRODUCT
Production data is only valuable if it is used. Data is particularly valuable when its use offers advantages not only for the company itself. At the same time, however, data are also critical assets. They affect the core substance of a company as well as its operating and business models. In order to realise the potential of integrated, data-based industrial value creation, marketplaces for data will therefore have to emerge in the coming years. These Industrial Data Spaces, which are also the focus of several public research projects, will become hubs of secure, rulebased data exchange. Different models are likely. In addition to the pure sale of data, business models will also emerge in which data is delivered together with the core product or temporarily released for inspection. At the same time, it can be assumed that customers will increasingly demand that their suppliers provide data on their solutions in real time. Regardless of which scenarios take effect, one thing is certain: Companies must build technological infrastructures and organisational models in order to collect product and process data in real time and process data in real time, process them in high quality and then be able to exchange them in a process-safe manner.
8. COLLABORATIVE SYSTEMS
THE NEXT WAVE OF AUTOMATION
Automation has been a defining theme in production for decades. However, advanced tools and the digitalisation of almost all are - as of the company are opening up new directions. On the one hand, with approaches such as Robotic Process Automation (RPA), more and more indirect functions, for example in the administrative and commercial areas, can be automated with a reasonable expenditure of resources and know-how. On the other hand, in the direct area, the trend towards collaboration with intelligent assistance systems is increasing - and is leading further and further beyond the boundaries of the factory. In these scenarios, which are designed to have a broad impact, AI and analytics systems show their pragmatic side above all, in that they are both clearly measurable economic contribution as well as compensating for resource and personnel bottlenecks. At the same time, the first resilient use cases are emerging today for automation solutions that aim for a “vertical” effect and extend the limits of human performance. In the medium term, however, such systems will mainly be used in other areas, such as surgery.
9. AI MANAGEMENT
PROCESSES AND STRUCTURES FOR INTELLIGENT SYSTEM LANDSCAPES
Study results and project experience show that companies see the greatest potential of AI systems in increasing productivity and efficiency. However, these goals can only be achieved if the use of AI is not seen as a project, but as a learning, permanent process that encompasses more and more company functions. This poses the task of organising the industrialisation of AI solutions and constantly developing them further. This is pioneering work, because it is becoming apparent that conventional IT processes and structures cannot be directly transferred to the management of an AI landscape. A key buzzword and focus of research initiatives in this context is “Explainable AI”. Typically, decisions and conclusions of neural networks are difficult to understand, which leads to a dilemma with implications for numerous service processes. One example is release management: how can an AIbased software product be tested, verified and released whose functionality cannot be traced line by line of code? Processes are required that differ significantly from classic software development and that can also deal with the fact that some aspects cannot be explained.
Last but not least, the applicable liability guidelines remain in force, so the question of which processes, services and products may be outsourced to an AI system also gains legal explosiveness.
10. DIGITAL BACKSOURCING
THE RETURN OF TECHNOLOGY TO THE COMPANY
In the course of digitalisation, companies are also changing the way they look at the management of digital technologies. More and more processes are taking place within the company - conception, development, operation. This is a consequence of the dramatically changed importance of data for operating and business models. Data are core assets and handling them should increasingly take place within the company’s own sphere of access - a remarkable trend reversal, after decades of outsourcing technology issues to external service providers. How robust this development is and whether we are at the beginning of a new paradigm of technology management remains to be seen. What is undisputed, however, is that the classic architectures, whose backbone was formed by powerful ERP and MES systems for decades, will not shape the digital future of industry. Modular platforms as the basis for scalable individual production worlds are better suited to the growing importance of data. And they fuel the return of technology competence to the company, where it has become an essential part of value creation.