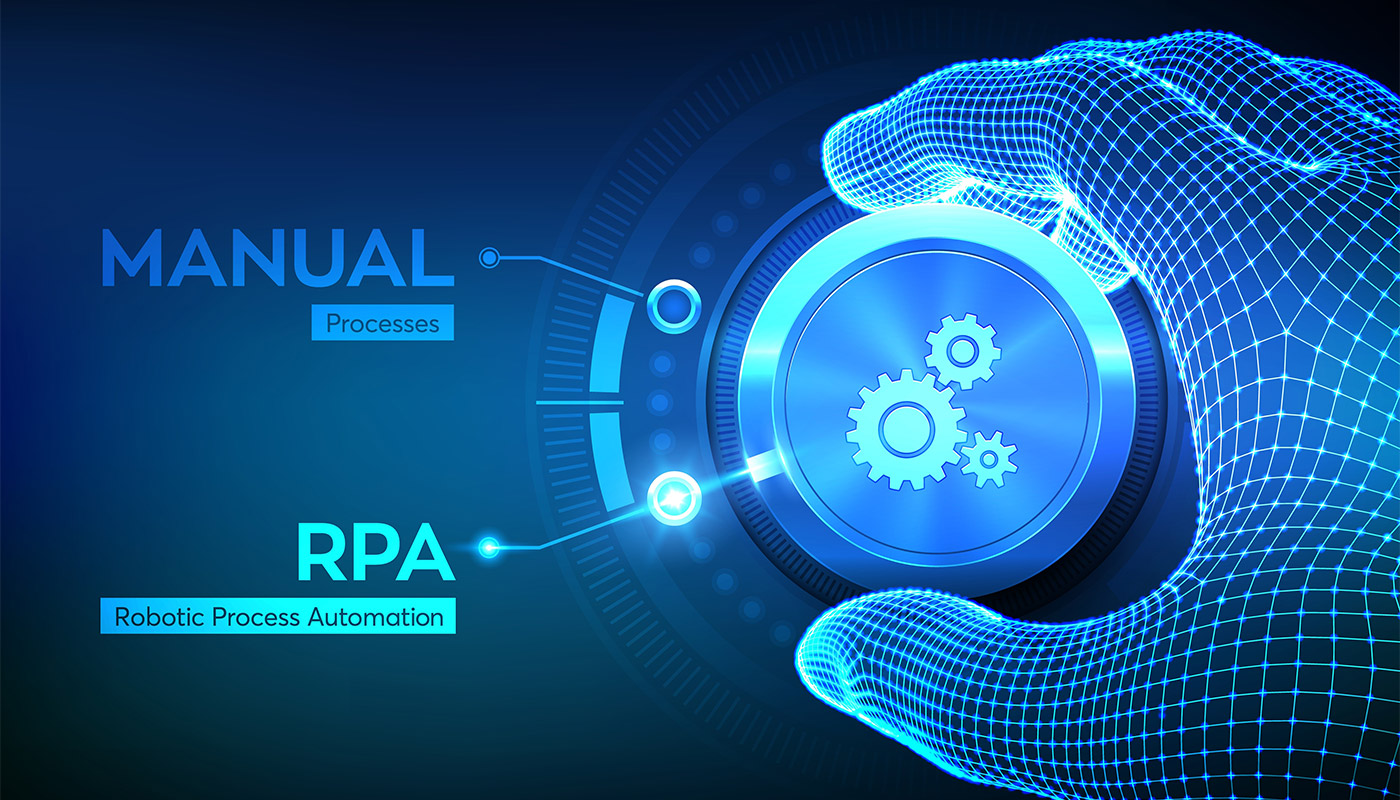
Software bots - Smart assistants for value creation
A mechanical engineering company redesigns its process landscape with Robot Process Automation
A manufacturer of machinery and special machines has already achieved a high level of automation in its production processes. Now the company is setting its sights on further, cross-departmental goals for process automation. Together with EFESO, it is defining fields of application in the operations area in which Robot Process Automation (RPA) tools are to ensure time savings and relieve employees. The software already passed the practical test in the first project phase: after only three months, RPA is already handling 14 processes in eight business areas of the company, such as R&D, HR, controlling or quality management.
EFESO approach
After a cross-departmental kick-off event, EFESO deployed software bots via detailed recording, development and testing in all involved departments of the company. During the test phase, the previous, "real" process and the automated process ran in parallel according to the "tandem" principle.
MOREAfter only three months, RPA is already handling 14 processes in eight departments.
Reclaiming resources for value creation
In "Robotic Process Automation", software robots take over work tasks that are very repetitive, time-consuming and error-prone. Typical examples are data entry in master data management, updating Excel lists in controlling or time recording in human resources. "Desktop automation" has been simplifying IT processes for 25 years, but it is only in the context of digitalisation and Industry 4.0 that RPA is conquering a broad spectrum of tasks in operations.
RPAs are in demand here as assistants that provide relief for simple but time-consuming work processes and also support in complexity management. In this project, one objective was to centralise the accounting from five locations at the company's headquarters without hiring additional employees. Instead, bots were to take over tasks such as invoicing, dunning or the preparation of data from different sources for reporting - from the first day of the changeover. The strict focus in the selection was on regular activities that are so specialised that their automation in systems such as SAP is not worthwhile, but which also tie up considerable time resources.
The second objective and special challenge of the project was to extend the change from manual to RPA-controlled work processes to the operations area, R&D, production and logistics in just a few months. The main questions were: Where is classic process optimisation at its limit? Which simple, "tedious" work processes can be automated so that the employees regain time for value-adding activities? And - last but not least - which RPA tools are so intuitively designed that they can be introduced, maintained and further developed without in-depth IT know-how? Together with EFESO, the company quickly implemented the appropriate bots. Only two weeks after the start of the project, the first bot was already saving half an hour per day in a previously manual stock correction of missing quantities in SAP.
After two weeks, the first bot provided savings.
Tandem of testing and applying
The project kicked off with an information event at which all involved employees of the company got to know how RPA works and what it can be used for. EFESO also explained the limits of the technology very clearly - after all, the functional areas involved should be able to develop a realistic picture of the effort required to introduce RPA to its benefits. In addition, the kick-off conveyed that RPA facilitates work by taking over tedious activities but not value-creating tasks.
After this kick-off event, the project team collected ideas or suggestions for work processes that the employees thought RPA tools could take over. In the following days, they selected 14 suitable processes from over 40 ideas in individual discussions. A detailed analysis was then carried out for each one, including video evaluations of the work steps or a detailed documentation of the clicks / actions in the input masks of the IT system.
From around 40 ideas, 14 automatable processes emerged.
Potential analysis and software selection
Based on these findings, the project team created an automation concept for all areas involved, prioritising the most attractive processes according to a potential analysis (Pareto principle). The selection of the RPA software that matched the company's requirements took little time. This is because a few leading providers currently dominate the RPA market, and the EFESO consultants are familiar with their range of solutions in detail. The selection of the software and the allocation of authorisations were already completed within two weeks in coordination with the IT department - directly afterwards, the implementation of the identified processes began.
Tandem principle as a success factor for implementation
The project team now brought - department by department, process by process - the RPA into everyday life, always via the stations of detail recording, development, testing. In the test phase, the previous, "real" process and the automated process ran in parallel according to the "tandem" principle. In this way, errors could be corrected or problems solved without causing delays in the day-to-day business. Once handed over, every work process finally ran via the RPA and directly relieved the employees.
Within a week, the selection and purchase of the RPA software was completed.
Key users ensure further development
However, RPAs are not "self-running" in the sense that they automatically adapt to future changes in the process - this control or maintenance must be taken over by the employees. Therefore, the project team trained so-called "key users" in the use of RPA so that they can make minor adjustments themselves. For example, when passwords change or the specifications in Excel files with which RPA works. In addition, the function of a "Head of RPA Excellence" proved valuable in other projects. As internal RPA process consultants, they are permanently on site, support in case of problems, automate further processes and thus ensure continuous improvement.
"Head of RPA Excellence" ensures continuous improvement.
RPA Use Case: Quality Management
RPA has had a significant effect in quality control, specifically in the inspection and reclamation of defective goods. Until then, the company had been checking incoming goods from its suppliers on a spot check basis and invoicing defective goods. However, the manual effort of a complaint proved to be too high in relation to the value of the goods in the case of many defects. The complaint is now handled by an RPA - with the result that the selection limit for goods subject to complaint fell from a goods value of 50 EUR to 15 EUR.
RPA Use Case: Controlling
The company's controlling department validated and consolidated the reports of 20 subsidiaries on a monthly basis. If errors or incompatibilities occurred, they were checked according to certain logics. Transferring these logics into the existing IT system would have cost a six-figure sum. Now the company uses a software bot that checks the exported reports in the IT system - for a five-figure investment.
If you hate it - automate it!
In the project, three experiences proved to be particularly valuable for the implementation of RPA projects:
"Identify "processes in the middle
The maxim "If you hate it - automate it!" is a good starting point for RPA projects. However, RPA should not be seen as a panacea. It is important to first correctly classify the intended use: Is the intended task (very) complex? Then an RPA deployment might be too expensive and a solution with a specialised system might be better suited. Are there use cases that are so simple that the programming effort for a system adaptation is not worth it - but automation is? Softwarebots are intended precisely for these processes in the middle, and this is where the greatest leverage for savings lies.
Utilise software bots 24/7
The licensing model of most RPA providers is designed in such a way that a software bot is available around the clock on every working day and public holiday. As with employees, payment is made per bot. If the bot is not busy with tasks, the bill is still due. Therefore, you should continuously look for other processes that it can take over. This is where the key users and the function of the "Head of RPA Excellence" are required.
Manage expectations
RPA is not "ready-made" software that does all the enhancements on its own after purchase. If the process that the software bot has taken over changes, this change must be adapted by the employee or key user. This should be clearly communicated in RPA projects in order to achieve a realistic expectation of what the bots can do.
The greatest leverage for savings lies in simple processes.
Combination of technology and methodological expertise
In all RPA projects, the EFESO team attaches great importance to a balance between process design consulting and technological implementation. Here, both the expertise in the selection of technology for the case of need and the methodological experience in the procedure play important roles, i.e. at stations such as an initial workshop, kickoffs, sprints, follow-up or the observation of how these processes can be sensibly continued.
In addition, the team calculates the ROI of software bots not only for one or two pilots, but also for the sum of all use cases if required. In RPA projects, it looks beyond FTE savings to other potential benefits such as speed, quality, errors avoided or customer satisfaction.
Another key success factor of EFESO's RPA projects is the parallel control of the previous, manual process alongside the new, automated one. This is the only way to compare whether the targeted results are achievable. At the same time, special cases and sources of error that were not yet present in the process start-up become visible as "start-up support". With this start-up support for each process, the RPA implementation does take a little longer - but the bot that is handed over then also functions more reliably than if the implementation is too fast. Experience shows that errors that have to be corrected afterwards cost significantly more time and money.