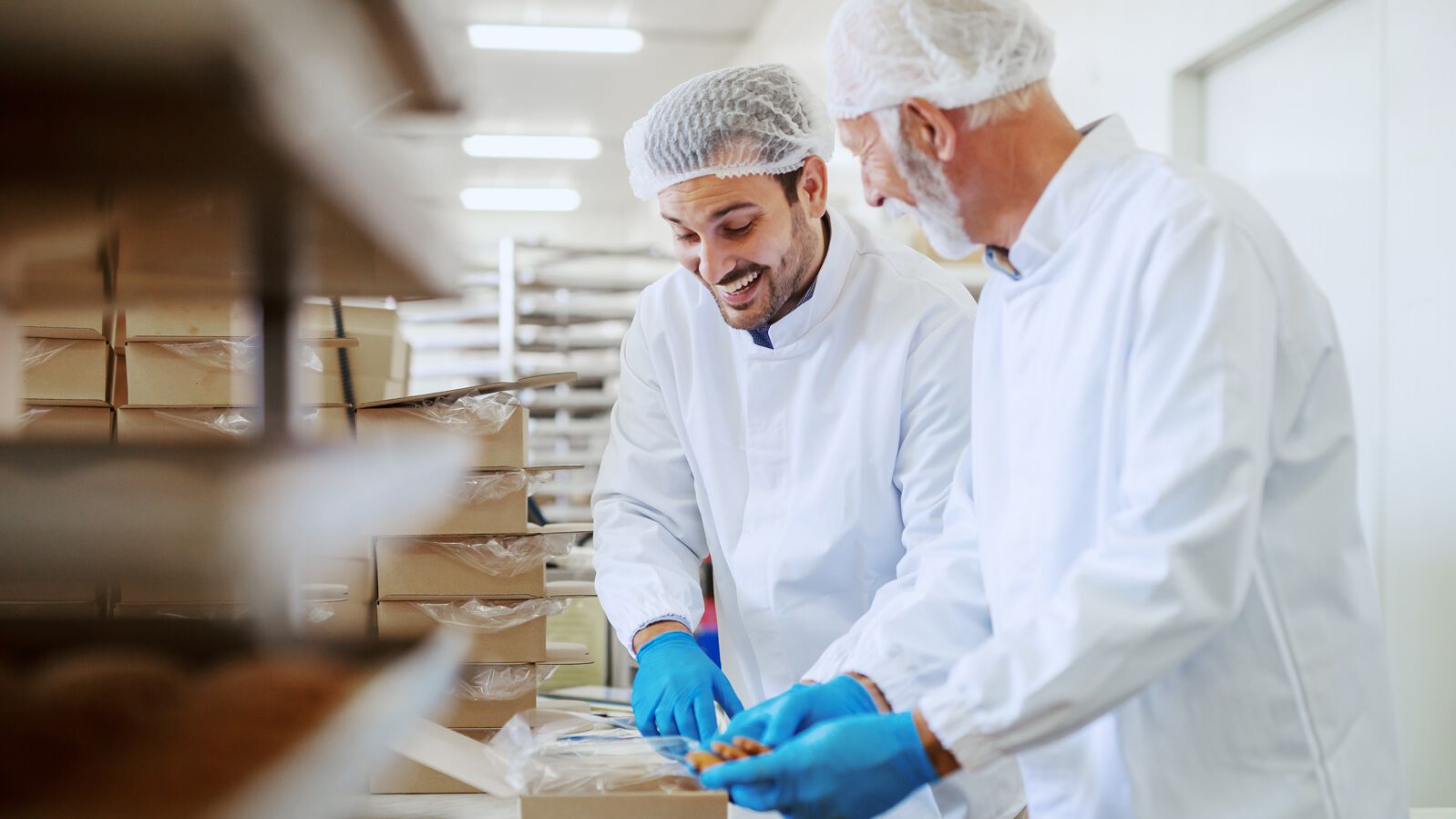
Digital transformation in the food industry
A confectionery manufacturer combines WCOM* and digitalization
A confectionery manufacturer is expanding its position in the European competitive environment with a comprehensive digitalization initiative. To this end, it is building on the successes already achieved by its WCOM (*World Class Operations Management) program – and expanding these further in the direction of a highly digitalized production.
Together with EFESO, the company is implementing a corresponding digitalization project tailored to its challenges. Its intention is to drive forward the digital transformation in ten areas of operations. Based on best-practice application examples from the industry, the project team developed a methodology that already ensured progress within a year: the confectionery manufacturer improved its WCOM routines by using digital tools and can now transparently present the performance of its manufacturing and production system.
Challenge
A confectionery manufacturer wants to use existing WCOM successes to drive forward its digital transformation. This requires IT / digitalization expertise and in-depth knowledge of operations processes in the food industry. With EFESO, the company has hired an implementation partner that is proficient in both areas.
MOREEFESO solution approach
With a use case-oriented solution approach, the project team selected industry-proven digitalization technologies according to the principle of "better tools deliver better results". It focused on three areas: Improving factory processes, increasing the efficiency of individual employees and establishing complete transparency on the performance of the production system.
MORELessons learned
WCOM and the Industry 4.0 pyramid are ideal for structuring and defining the use of tools in the company. It is also worth regularly looking beyond the production line to improve the entire production system.
MOREEFESO success model
The use of new technologies must not slow down the day-to-day running of production but should instead demonstrably improve it. In the project, EFESO promoted solutions that increased the maturity level of digitalization in all areas of activity.
MOREExpanding WCOM's success
The company is already established in the food industry with chocolate bars and biscuit mixes. It was formed in the 1990s from the merger of two confectionery producers from Italy and Germany and today sells various product brands in Europe.
In this case, several factories were already pursuing different, altogether progressive approaches to the further development of IT and OT. To unite these approaches, the management used a valuable lever: an in-house WCOM (World Class Operations Management) program with a lean focus, which had already brought classic production topics such as safety, quality control and plant maintenance to a high level of performance. With a view to future competitiveness, the aim was now to continue this success story with the digital transformation. The central objectives were:
- Cultural change: The workforce should not see digitalization as a burden, but as an opportunity to shape their day-to-day work more effective. At the same time, they benefit from the fact that the performance of the production system increases.
- Cooperation: IT and production must work more closely together in order to develop a common understanding of challenges and solutions more efficiently.
- Future orientation: The production system must be designed in such a way that relevant developments in digitalization can be kept in view and integrated as required.
Orientation towards best practice examples of digitalization
The first step was to record the initial situation in a plant as a reference point. This was done by a project team consisting of IT and production managers and EFESO consultants. As next step, the larger task was then to develop a concept for digitalization that would set standards throughout the company beyond the line and the plant.
The project team opted for a use case-oriented approach in order to work with concrete case studies from the outset, which could also be implemented quickly in practice. This involves identifying and implementing all process improvements in the company using best-practice application examples from the food industry and other sectors.
Furthermore, the project team recorded and evaluated the existing technologies: for example, the plant used smartwatches to directly alert employees on the line in the event of deviations in temperature values in the heating process, thereby shortening the response time. To this end, the "Industry 4.0 pyramid" was utilized as a reference model to ensure a uniform system for the evaluation and selection of existing and new use cases. This enabled the team to classify, at which level (e.g. connectivity, information flow or prediction) which tools are available with which maturity levels – and to identify corresponding gaps.
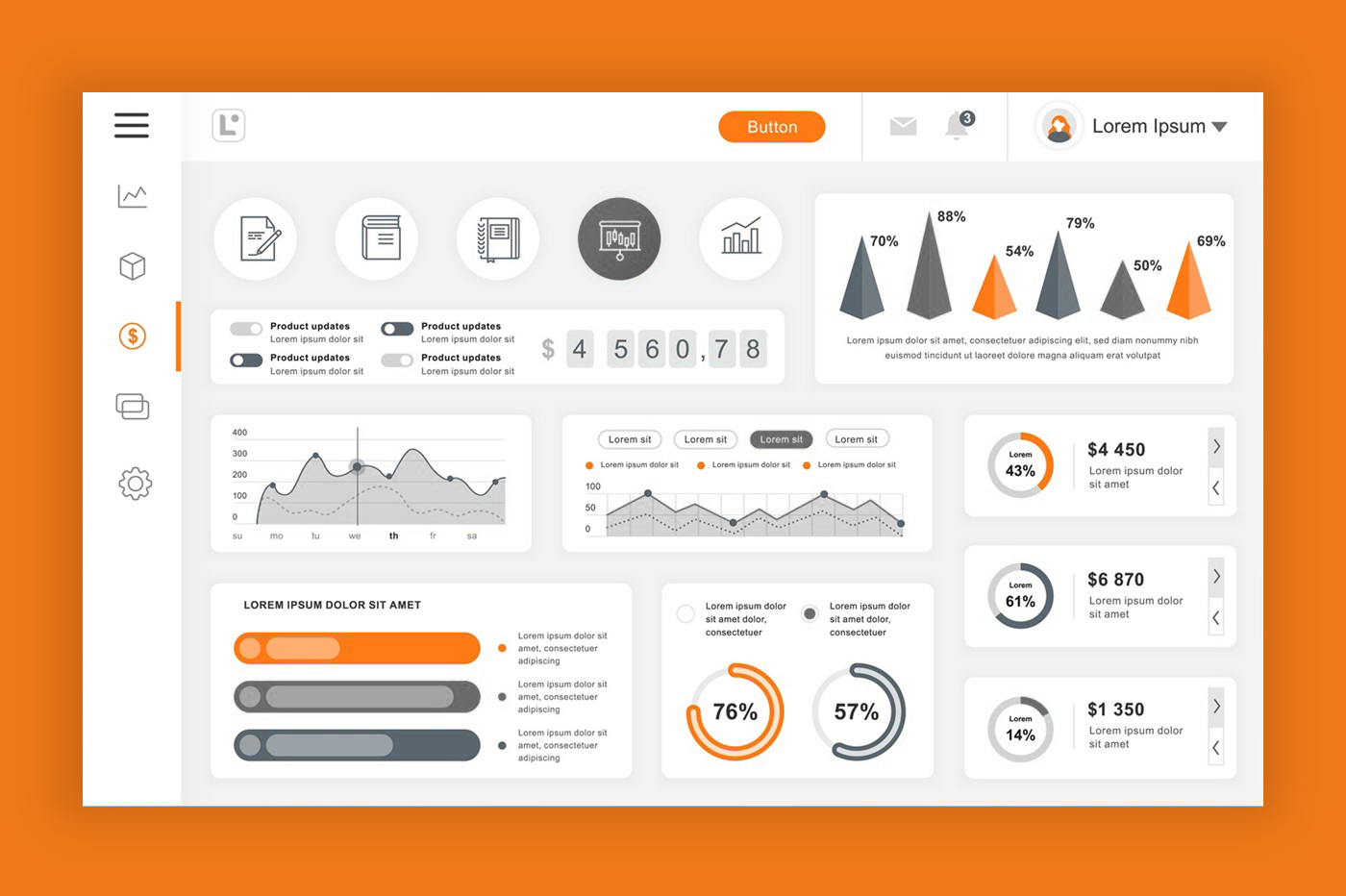
Cooking process – visualization
- Visualization of progress at the beginning of the line (upper level) and at the forming line (lower level).
- Use of the final weight measurement in the pre-coating area (430 kg container) for order processing release.
Results:Transparency of progress and pending tasks, increased productivity.
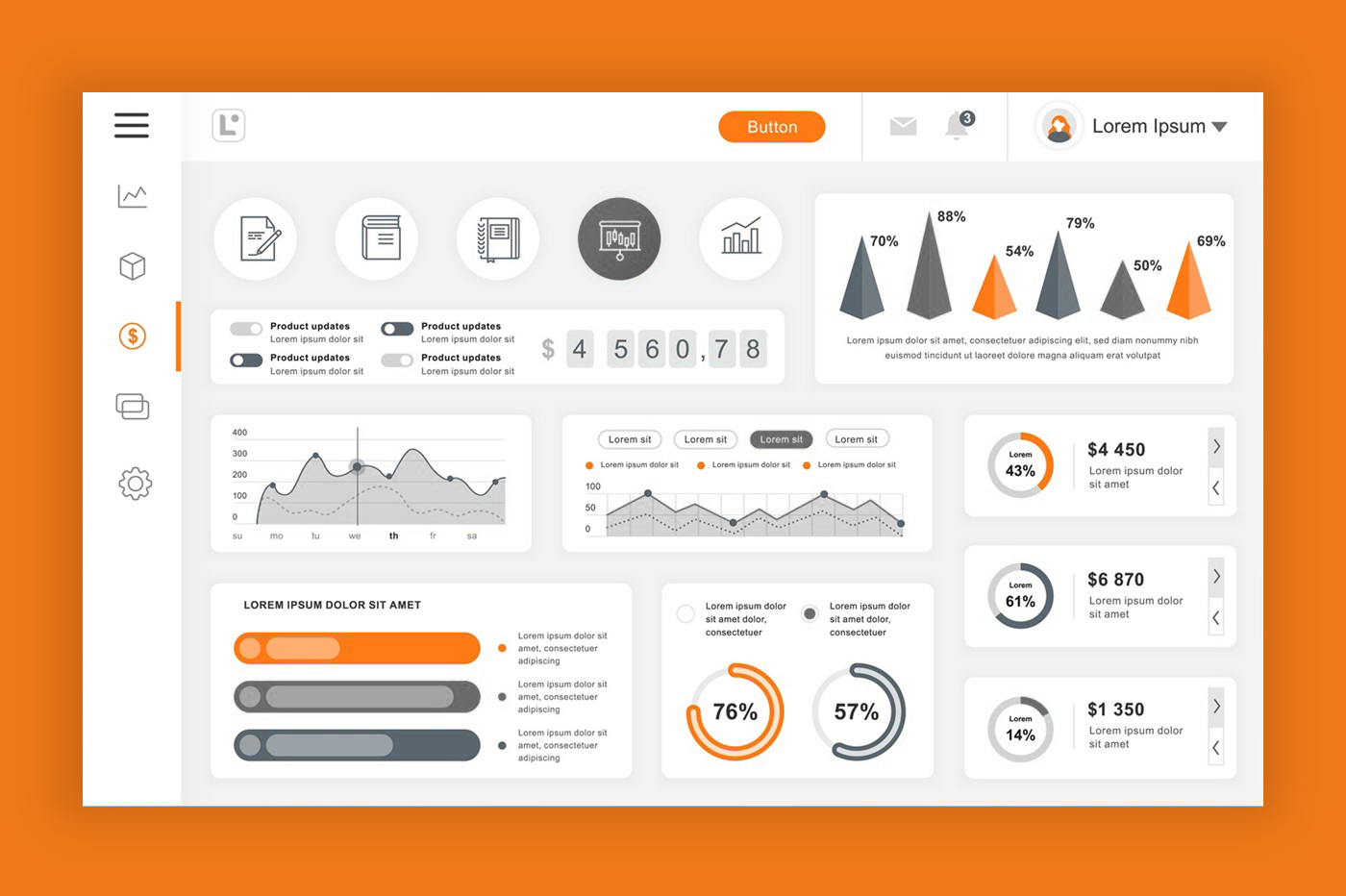
Cooking process – machine control
- Evaluation of the current level of autonomous machine control.
- Use of the process data history to investigate faults / irregularities.
- Operators record material losses and thus supplement the database.
Results:Reduction of the reject rate and continuous process optimization.
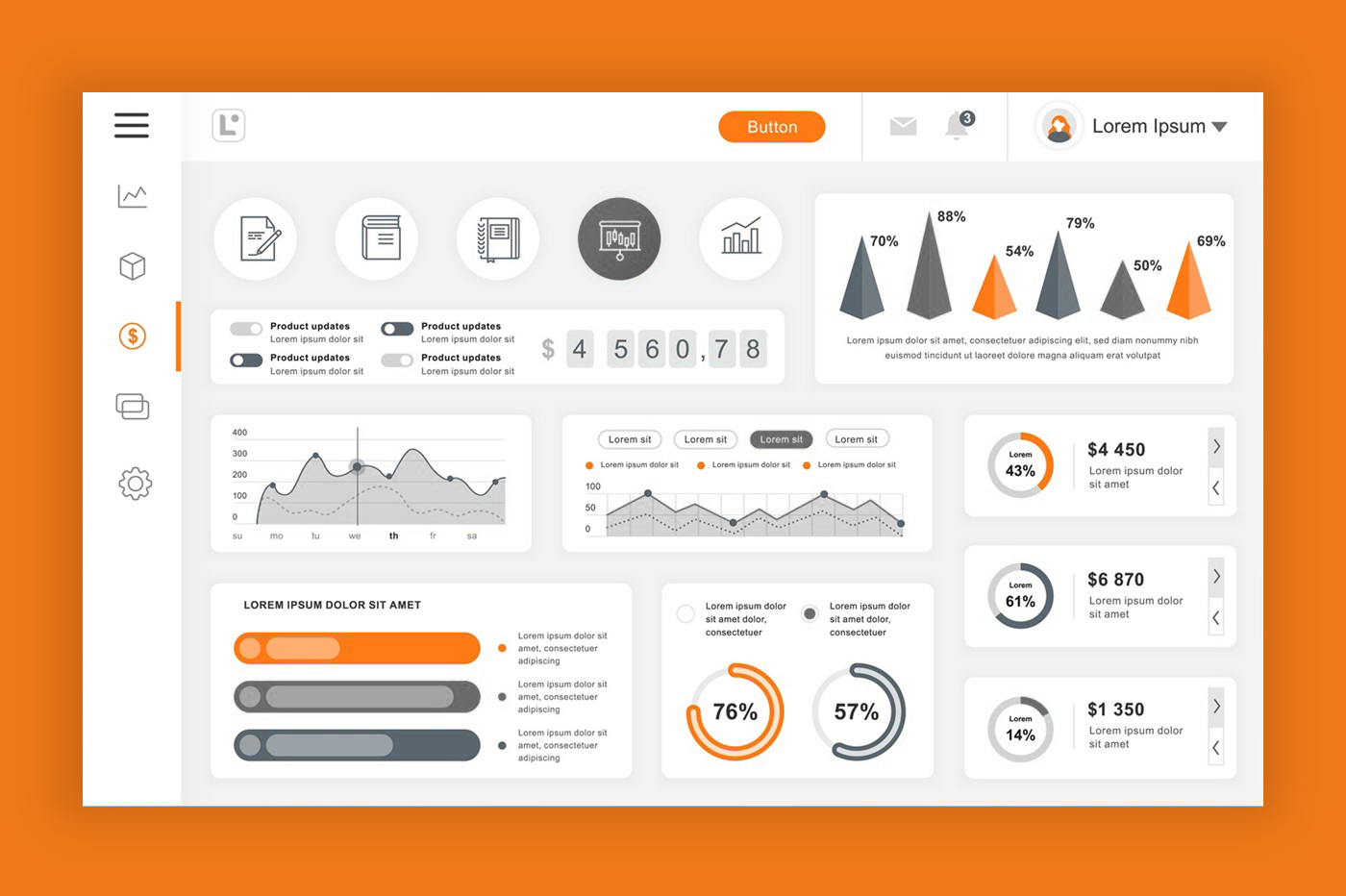
Coating – digital logbook
- Creation of a digital logbook that records incidents during a shift, e.g. machine settings or missing persons.
- Linking the logbook to the machine; each incident automatically leads to a new entry.
Results: Shift handovers are more informative and simplify root cause analysis for incidents.
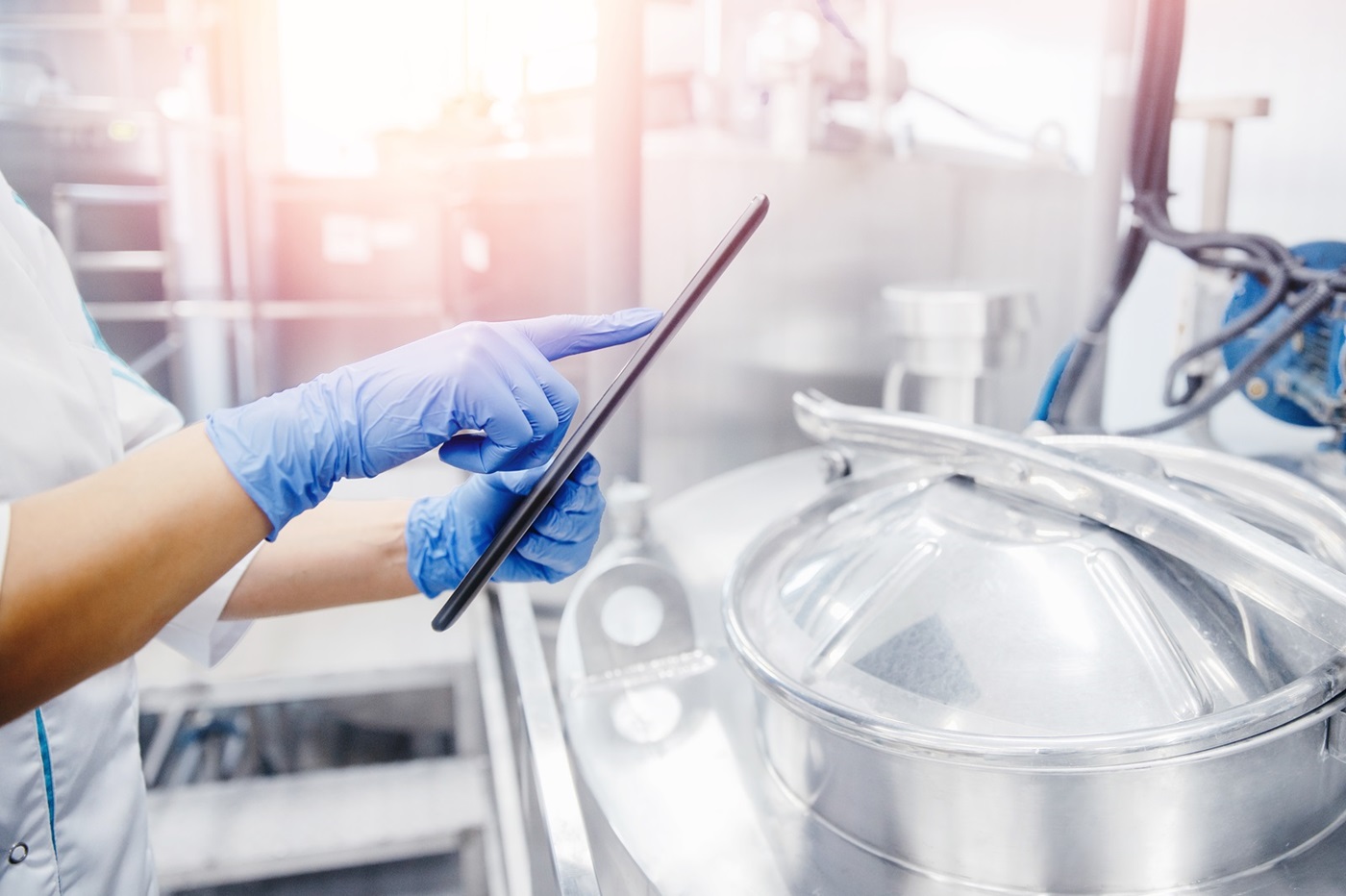
Planning – KPI visualization
- Visualization of KPI data and automated reporting with Power BI.
- Creation of individual dashboards with drill-down options that can be shared with team members.
Results:Reduction of manual effort for reporting.
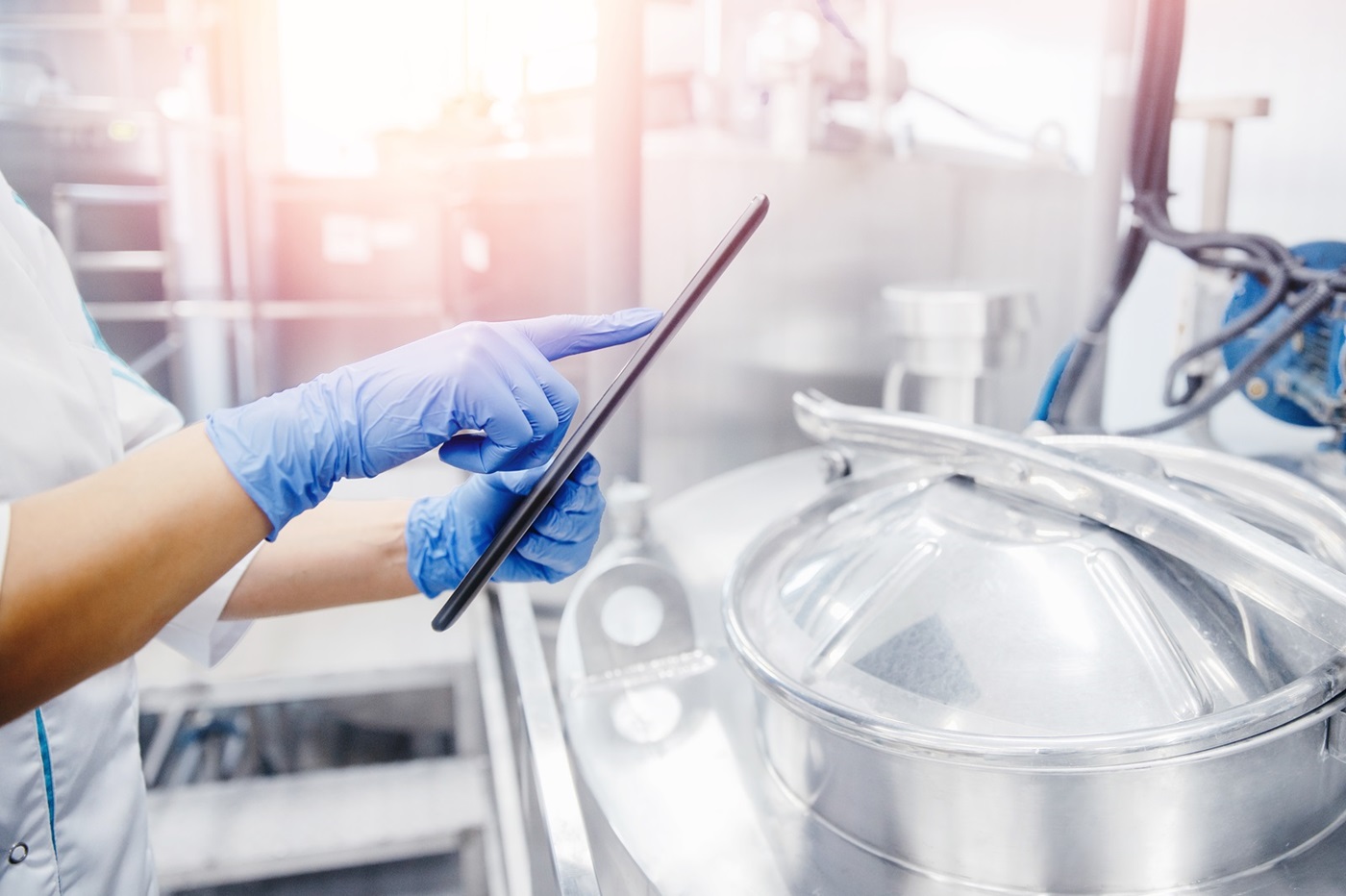
Maintenance – documentation
- Recording maintenance data with a smartwatch or tablet.
- The alarmed smartwatch can record how long technicians have been working on problem solutions.
- Via tablet, technicians can add further data directly after the incident.
Results:Use of data to improve WCOM activities in the maintenance organization.
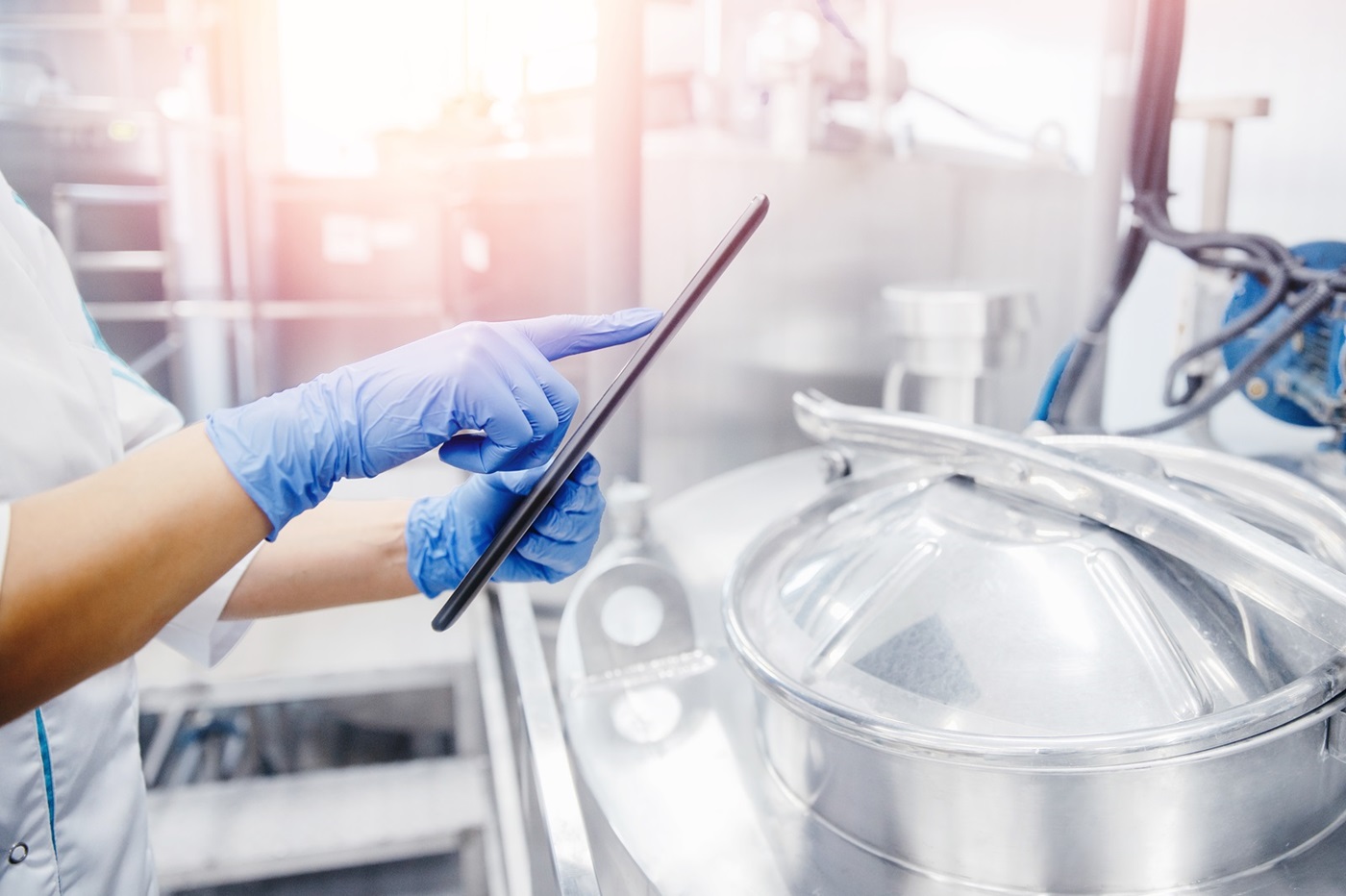
Quality control – Deep Learning
- Use digitally captured data to detect patterns or irregularities in quality control.
- Eliminate manual effort, such as collecting quality control sheets.
- Reduce manual search time for quality incidents in the field.
Results:Increased transparency and improved process knowledge of employees.
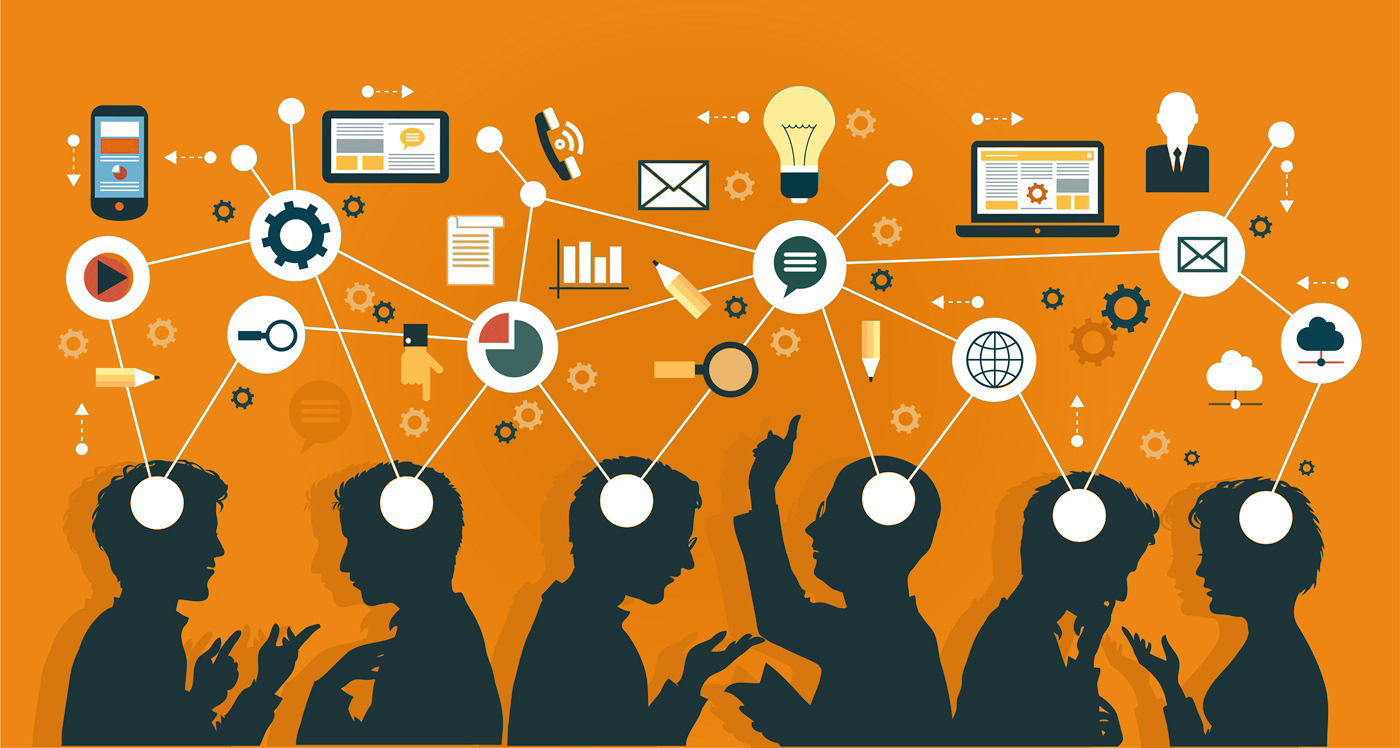
Qualification – Web Based Trainings
- Establishment of a training plan to support plant operators.
- Use of interactive e-learning modules to track learning success.
- Creation of individual, needs-oriented learning videos and training plans.
Results:Structured digital training, deeper and faster learning effects.
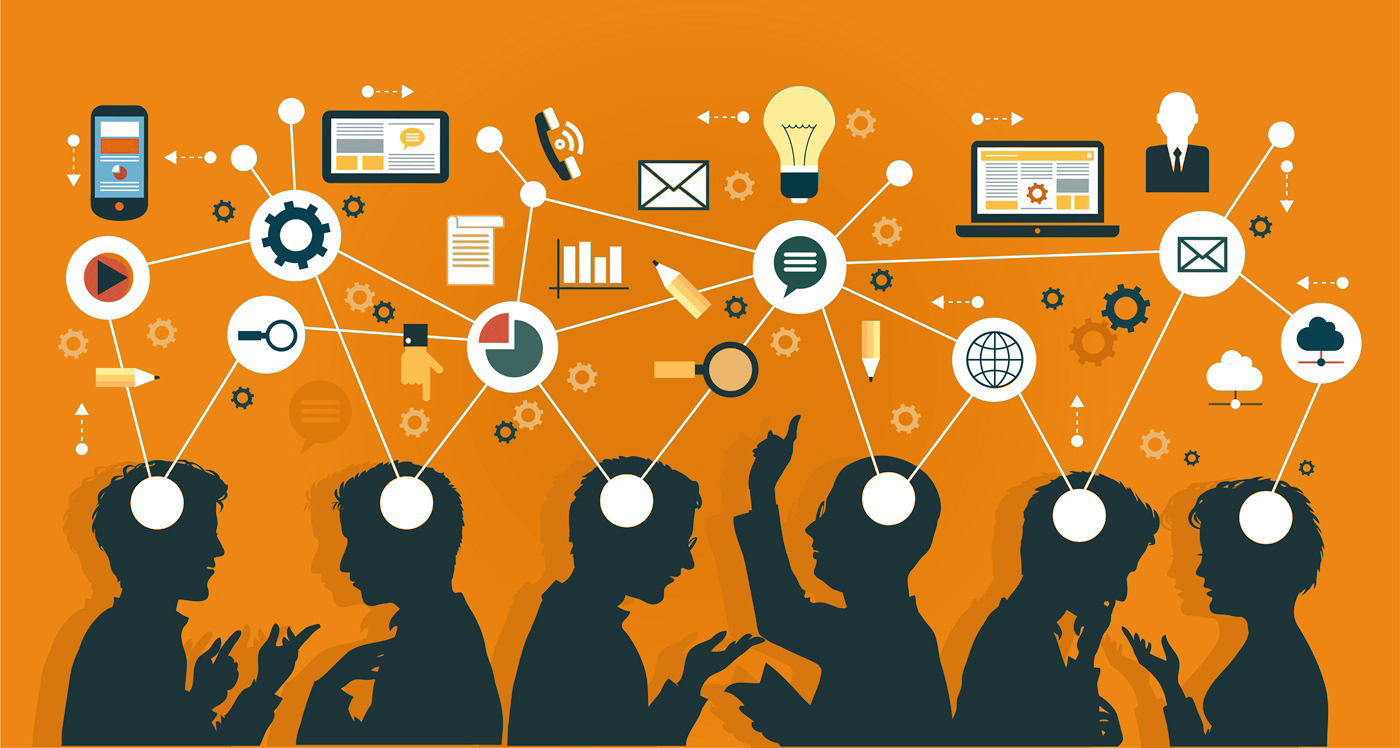
Project management – virtual cockpit
- Visualization of the status quo and upcoming process steps.
- Control / intervention by the plant manager is possible.
- Team members can confirm the start and completion of their tasks.
Results:Complete transparency about the status quo of work processes in the respective area.
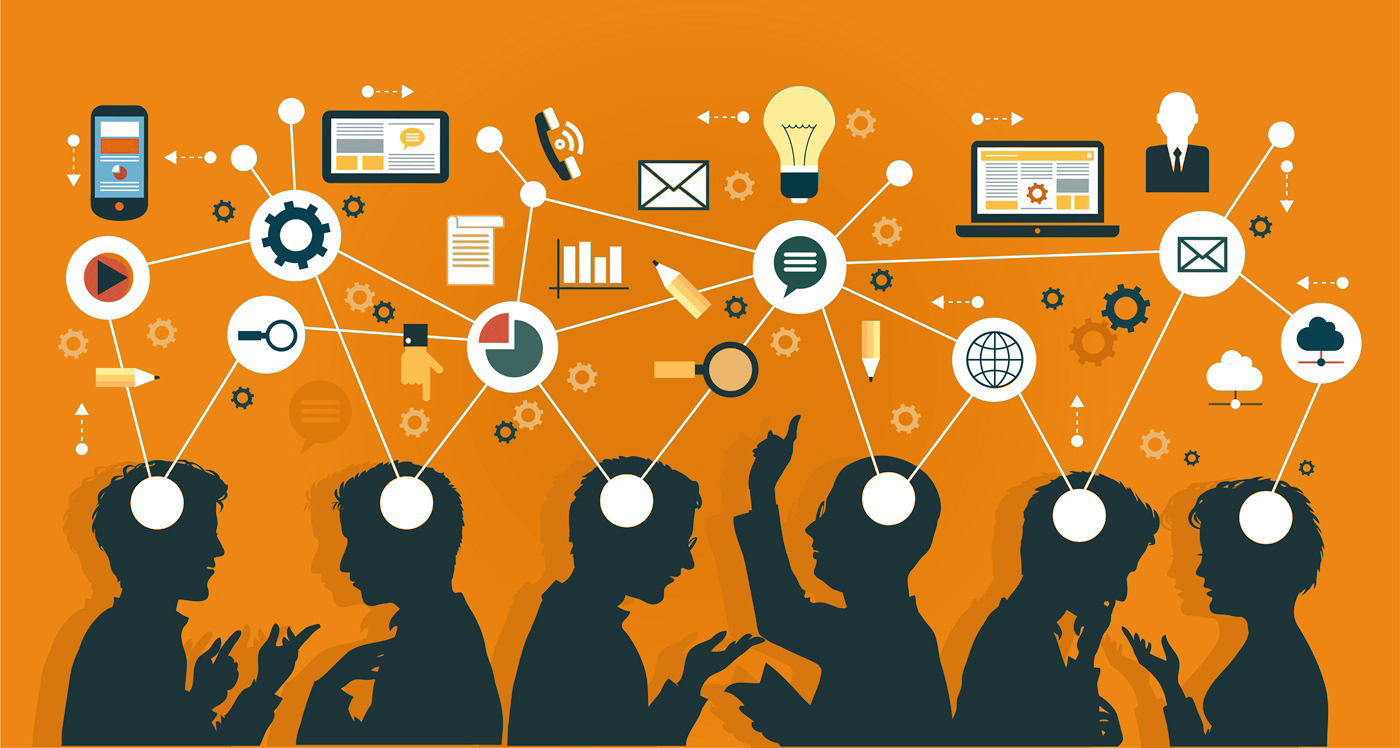
Qualification – best practice know-how
Monthly news update for all team members; contents are e.g:
- New learning materials.
- Exceptional work results / KPI.
- Best practices for the use of digital tools and other technologies.
Results:Knowledge sharing between employees, teams, departments and factories.
Focus on three fields of action
According to the principle of "better tools produce better results", the use cases were selected to ensure that tasks are not only solved "fragmentarily" on the line or in the plant. By using them, the company should also be able to clearly record and continuously improve the performance level of its production system as a whole.
The project team mapped these objectives by using two reference points for the digital transformation: the plant level and the system level, both connected via an own WCOM program (see graphic). The use cases of the program were assigned to three focus areas:
- Focus area 1: Improvement of factory processes – the digital solutions support the processes on the shop floor.
- Focus area 2: Application of production system tools – employees are empowered to work more efficiently with the help of digital tools.
- Focus area 3: Achieving full transparency – the digital tools provide clarity on the performance of the production system and enable WCOM managers to continuously develop the WCOM framework.
Change of perspective from the individual case to the “big picture”
During the implementation of the project, the following empirical values proved to be particularly critical to success:
Detach yourself from the individual case!
Individual technologies such as AI tools or digital twins do not accelerate a digital transformation on their own. The aim must be to structure and systematize these individual elements and bring them "into the breadth" of the application. WCOM and the Industry 4.0 pyramid model are ideal maturity models for this. This combination ensures, that progress in the production system "moves along" in parallel with the progress of digitalization.
Expand your view beyond the line!
The confectionery manufacturer experienced that the employees at the production line were proactively involved in improvements, for example in the conversion of quality documentation from an Excel to an image-based application, which reduces the workload and input errors. Such successes are important starting points for looking “beyond the line” to improvements in the entire production system. In this case, the company integrated the documentation into a digital KPI dashboard that presents the information appropriately for each user group, from plant operators to management.
Use modern knowledge management!
In this particular case, the company attached great importance from the start of the project to ensuring that its "corporate digital excellence" also took into account the flow of information throughout the organization: how do the teams in the factory side learn from each other? And how can sample solutions be shared quickly within the plant network? The use of modern qualification tools such as digital learning platforms with use case-related training ensures significant progress here.
Production system as a promoter for digitalization
With the described approach, the confectionery manufacturer was able to integrate his IT experts more closely into production. The whole team developed a common understanding, which use cases / tools are suitable for use. This combines the joy of experimentation with a realistic view of the desired added value.
In addition, the collaboration with EFESO ensured that the digitalization of the shop floor did not slow down the day-to-day business in production, but instead accelerated it and transferred it to connected operations fields. As a result, the company now uses its production system as a vehicle to drive forward the digitalization successes already achieved – the combination of WCOM / Lean and Industry 4.0 elements continues to form the orientation framework. Four aspects were decisive for the success of the project:
- A common understanding of the initial situation and requirements; in addition to the IT and production perspective, employees from quality management were also involved.
- The targeted improvement of the WCOM elements and the elimination of losses, for example in the use of additives or the production of base materials.
- A clear elaboration and communication of the "core" of digitalization, in particular through the creation of use cases and their economic benefits.
- Empowering employees to continuously develop the production system. This relates to both the content of the training measures and the training tools used.