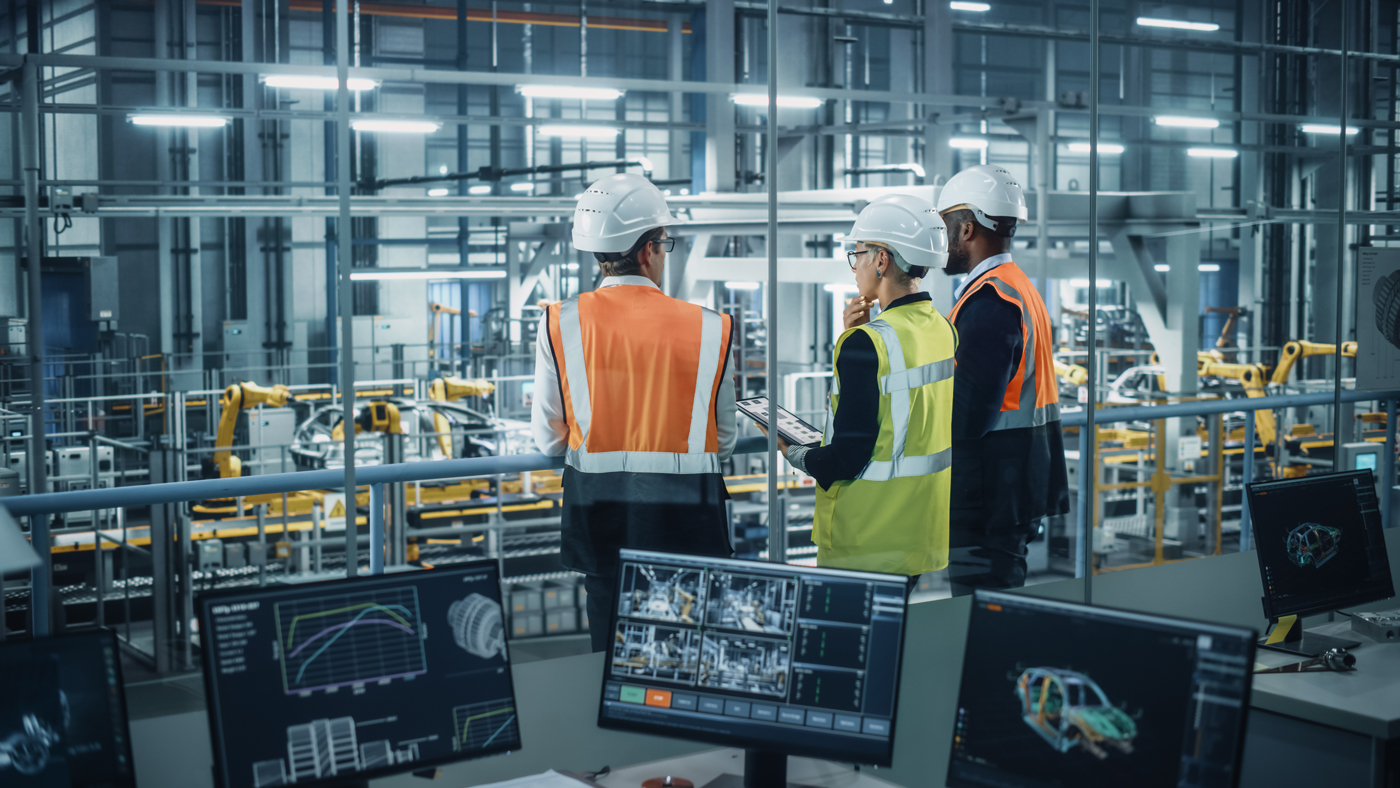
The clearer the goals, the better the planning
An automotive supplier takes its production planning and control to a new level of performance.
In ten production sites around the world, an automotive supplier harmonizes the sophisticated planning and control of its manufacturing processes. Before the joint project with EFESO, each site had developed its own methods and tools, in some cases over many years. A uniform planning software was now to provide structure and transparency - and expand the options for action in this important area.
Increasing planning quality and at the same time benefiting from uniform planning in all plants: with these objectives in mind, the company worked with EFESO to create the future planning strategies and methods as well as the target planning process. In addition, the project team defined the functional requirements as well as the essential planning parameters and restrictions. Another essential point was a structured software selection: Here, the company selected from over 20 potential solutions the one that best met the functional requirements of the defined specifications.
Challenge
Ten production sites of a global automotive supplier had developed their own methods for planning and controlling production. Simplified, software-supported and harmonized production planning for all plants is intended to increase planning quality and make production more efficient.
MoreEFESO approach
Identification of a demand-oriented software for production planning and control on the basis of a detailed analysis, conception and a selection process with providers of suitable software systems.
MoreLessons learned
Involving all those concerned in planning proved to be critical to success. It is equally important to use small, agile pilots to test whether the ideas and logic of the new production planning work.
MoreEFESO success model
The key to success lay in the detailed analysis of all conditions and weak points in the initial situation before a target concept was developed.
More"Self-knit" planning for a multi-layered and complex manufacturing process.
Challenge: complex manufacturing process and specific markets
Suppliers to the automotive industry are under enormous time and cost pressure. In order to be able to use production resources efficiently and flexibly, planning is necessary that synchronizes the individual value creation stages in the entire process chain as optimally as possible. In the past, however, planning and control processes at the supplier were mostly carried out in isolation, uncoordinated and with simple software tools such as "home-made" Excel solutions.
The company therefore set itself ambitious but realistic goals. With the introduction of differentiated but standardized planning strategies and methods, as well as the appropriate software, all plants were made to be
- More efficient in the manufacturing processes,
- With lead times shortened,
- Inventories reduced,
- Increased flexibility and
- Reduced production costs at the same time.
It should also be possible to carry out the long-term capacity planning of the plant group in the new software, or at least to supply it with uniform data.
Solution approach of EFESO: Conception of a planning and control method
The company commissioned EFESO with the conceptual design of a new production planning for its ten plants based on a suitable software solution, which was selected in a later step. The project team at EFESO consisted of the project manager and another consultant for specialist topics. On the company side, four employees formed the core team. Another 20 colleagues from all locations - two representatives from each production plant - worked together in the extended team.
Planning cannot be optimized without also optimizing production.
The first step was to create a new concept for the planning method that would enable the set goals to be achieved across all sites in the future. After all, planning is only ever an instrument that specifies how production should ideally function. However, planning cannot be optimized without also optimizing production. But how must production be designed in the future so that it functions efficiently and agilely with low throughput times? To be able to answer this question, the project team first carried out a detailed analysis of the production and production planning processes, the Product portfolio, the technological and organizational framework conditions, and the restrictions in the ten plants. Among other things, it took into account the planning principles and guidelines used at the time as well as customer demand patterns and customer requirements.
Employees are involved in finding solutions instead of having to implement a predefined concept.
Based on the results of this analysis, a rough concept with suitable planning strategies was now developed in close cooperation with the production managers of the individual sites. In regular workshops, at which other production managers from the individual plants were also represented, the consultants imparted method-related knowledge to the employees - for example, by evaluating their own production data and developing ideas for improving planning. After all, the employees on site usually know best the weak points and opportunities for improvement in the line or in the entire plant. Particularly in a step-by-step insight process like this project, it is reasonable to involve employees in finding solutions from the very beginning, rather than confronting them with a ready-made concept.
Different production planning for frequently demanded standard products and rarely demanded "exotics".
Lean, fast and software-supported: the new production planning process
In a variability analysis, the project team analyzed customer demand patterns at the product level to identify constant and regularly recurring requirements, e.g. frequently demanded products in a uniform design. These differ fundamentally in their planning and production from irregularly demanded products with high variability, for which a high degree of production flexibility is required. Thus, the respective sites could be classified according to suitable planning strategies based on current technologies, processes and assigned product portfolios. Two "plant clusters" were formed:
- The "efficient factories" that can efficiently produce large quantities over and over again
- the "flexible plants" which, as specialty plants, can manufacture their products very flexibly in small quantities and to the highest quality standards
In the absence of a concrete target image, the "as-is" state is cemented in new software - without any optimization.
Based on the analysis results and under the guidance of EFESO, these two plant clusters each worked out their suitable target picture, i.e. an ideal of what the corresponding planning for their cluster should look like in the future, without taking restrictions into account. In the second step, the restrictions that cannot be resolved in the short term were added back, thus determining the first feasible optimization step.
The project team derived the future planning and control methods for both clusters from this and described the target planning processes. It defined essential planning parameters and restrictions such as minimum and maximum lot sizes or setup-optimized production sequences as well as functional requirements, such as finite production planning and pegging functionalities. Finally, it recorded the target software requirements in a specification sheet.
Suitability test with show case: the software selection process
Only after these project phases did the actual selection process for the software solution start on the basis of the specifications. The credo from the very beginning was to keep this as simple as possible. The functional requirements for the software were defined. It turned out that, given the multi-layered production of the company with its differentiated Product portfolio, this was much more complex than initially expected. The conflicting optimization processes in individual production stages, for example, presented a particular challenge.
The project team compiled a long list of suitable systems for advanced planning and scheduling (APS) and for a manufacturing execution system (MES) on the market and initiated an initial selection process based on self-reports from the software providers and initial presentations. The result was a short list of four providers and three different software solutions. For the final selection, critical planning scenarios were defined, which the remaining providers should implement in their software solution. This selection was made on the basis of a beauty contest in which the providers presented their tender documents and demonstrated the critical planning scenarios in their software. The project ended for EFESO with the recommendation of two software solutions that best met the functional requirements of the specifications.
Lessons Learned: Structured approach is essential
It proved decisive for success to first develop a detailed analysis and a needs-based concept - and only then to tackle the project scope for software selection. It would be more than negligent to describe a requirements catalog or propose a software selection without these upstream steps. Above all, it is important that before the requirements for a software solution are defined, the future goal picture is outlined and defined as clearly as possible ("What is to be achieved and how?"). Answering the following questions is helpful in this regard:
- What supply chain and production strategy am I following?
- What do I want my production process to look like in the future?
- How should the planning logic work?
Before the requirements for a software are defined, a detailed analysis, clarity about one's own goals and a coherent concept are needed.
It saves no time and certainly no costs to start the process in the middle without such an analysis and conception. Otherwise, you find out later that something is missing or doesn't fit - and then you do loops that cause the overall process to take longer and be more costly. The project team also gained valuable experience in other areas:
- Involve stakeholders: The early and consistent involvement of all key operational stakeholders in the process gives them the opportunity to learn and gain a better picture of their future tasks. This strengthens the motivation of all those involved to work together to make the project a success.
- Use agile pilots: Small, agile pilots can be used to test whether the ideas and logic of the new production planning also work. To see if there is a problem somewhere, a real plan can be set up and run in parallel with the new logic for a few weeks. In this case study, this worked well, so that in the next step, the software requirements could be recorded on a concrete experience basis.
- Keeping organizational aspects in view: The topic of organization must not be left out, i.e., one must also keep an eye on the overall context. After all, you cannot introduce a new process and otherwise leave everything as it is. The associated organizational roles and responsibilities, interfaces, functional areas (silos!) must also be adapted accordingly, as must target systems, KPIs and incentive models. Failure to do so will result in "old behaviour in new shoes".
The greatest successes are achieved by those who also use the tools to change the mentality and behavior in the team.
EFESO success model: practical relevance and future prospects
The project was characterized by intensive cooperation, both between the management and the project team as well as within the entire shopfloor team in the lines. The EFESO team received feedback that they had provided valuable support with "practical relevance, social competence and experience". The implemented measures, in particular the higher cycle time of the filling lines, increased the output by up to 30% depending on the line. Shopfloor management routines and continuous improvement processes (CIP) quickly developed.
The analysis phase and the shopfloor also led to the identification of a whole series of fields of action and follow-up topics which, although not addressed in the project, are valuable points of reference for future improvements. For example, the topic of "paperless/low paper factory" developed into a preliminary study for the selection of a manufacturing execution system (MES) or a system for production data acquisition (PDA). The company can now activate further potential, for example, with the introduction of a software-supported production planning system (PPS), the digitalization of shopfloor management or the use of an MES.