(Kopie 1)
Silent Revolution
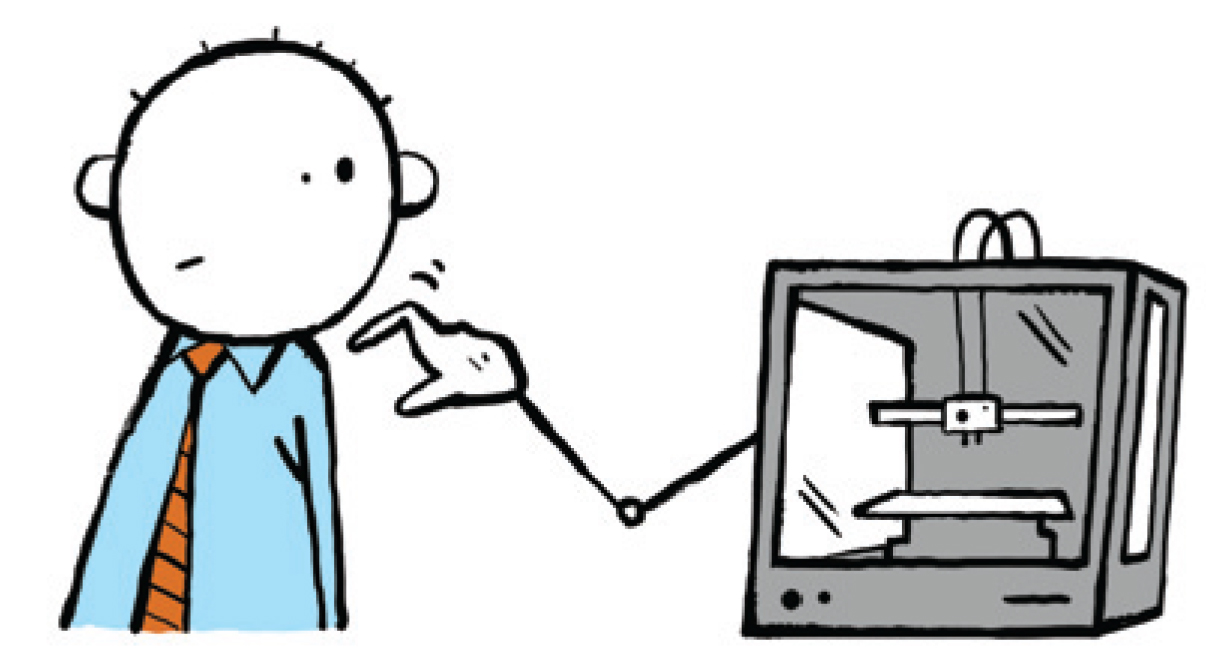
3D printing has already started to change industry. Ignoring it is not an option
Numerous studies forecast that global expenditure on 3D printing will double or even treble over the next four years, with hardware, powder materials and software accounting in equal parts for this growth. Industry analysts and leading manufacturers of industrial 3D printing equipment and materials like metal powders are feeling the growing demand and expect the integration of additive and traditional manufacturing to increase. After all, 3D printing only requires one tenth of the raw materials of conventional production, enabling cost-effective and high-quality manufacturing of unusual geometries and small series as well as guaranteeing an extremely high degree of flexibility. This is why today automotive, healthcare, defense and aerospace industries – and not only these – are investing in additive manufacturing equipment and systems.
However, at this point people often enough dismiss this growth as being primarily generated by prototyping and the production of expensive or highly complex components. They continue to add that additive manufacturing, in relation to the overall volume of production, is still a negligible market segment, limited to specific production tasks and driven by grand visions and insignificant results. And that additive manufacturing on an industrial scale is a rather capital-intensive and sophisticated technology that wouldn’t work at the “flick of a switch”.
There is an element of truth in this, but we shouldn’t just take the easy road since the real picture is changing radically, and there is increasing evidence for this. There are many reasons to believe that large-format 3D printing will gain a firm hold in industry as a manufacturing process and that many established forms of organization and process as well as profitability calculations and supply chains will be challenged. For companies that systematically engage with the new technology, 3D printing has already found entry into the design stages and is influencing the value chain from procurement through to aftersales service. In relation to the extend and planning of the integration process, the impact of the technology on an organization will be distinctly felt – for example through the elimination of entire production steps and the localization of manufacturing, the shortening of value chains through increased vertical integration, new qualification requirements and team structures, or the emergence of new process-based, technical interfaces to customers.
Nevertheless, the fact that a purposeful and well planned deployment of 3D printing provides tangible benefits is just one side of the coin. The other side of the coin is that the technology allows us to take a completely new look at supposed invariants. The question here is, for example, whether classical series production needs really large factory buildings. From the perspective of overall costs doesn’t it pay off more to opt for small, local production sites with 3D technology instead of outsourcing or bought-in parts? Is it possible to devise an extremely customer focused production process without extensive investments in new infrastructure? Can fully automated 3D foundries be set up by combining additive manufacturing and other Industry 4.0 technologies? Is it possible to operate outside of typical hierarchies and team structures in production?
Of course, many solutions based on 3D printing are currently too slow or too costly in order to break up structures across the whole of industry. However, they show that these fractures are in principle possible, while the technology grows more cost-effective and powerful by the year. In other words – scenarios counting on an extensive integration of additive manufacturing are currently not an imperative for every segment of the value chain or for every company. But at the same time, it is not an option to avoid thinking about such scenarios.