(Kopie 1)
How would robots plan a warehouse?
By Dr. Wolfgang Keplinger, ROI Management Consulting AG
Although robots are already used today in many small parts warehouses, it is currently still clear that they were designed for humans. There are long rows of shelves arranged so that workers can easily pass between them and access each of the stored containers as easily as possible. And even if today this task is carried out in most warehouses by automatic storage/retrieval units (SRU) or autonomous shuttles, the basic principle of the shelf warehouse with its open front surfaces, its traffic areas and spaces has changed little over time. But what would a warehouse look like that would not follow the traditional patterns of human operating logic, but instead would be optimized solely for automated operation by robots?
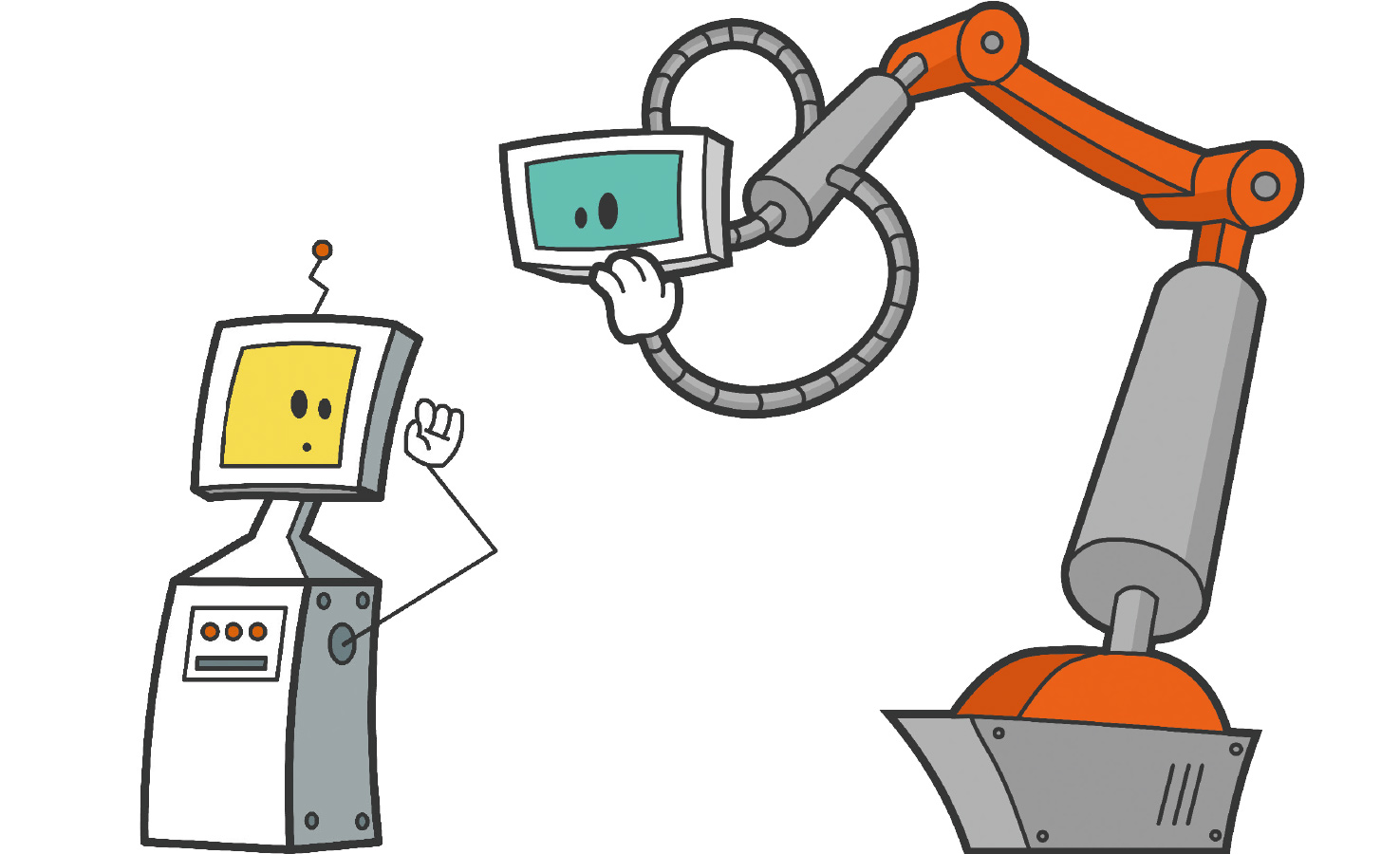
Rethinking the warehouse
The AutoStore system for automatic storage and order picking of small parts from the Norwegian manufacturer Hatteland provides an answer to this thought experiment. Based on the premise of arranging containers as space-saving as possible in the available area, the system breaks radically with the design principles of traditional warehousing: Instead of shelves, the containers are stacked directly on top of and next to each other. Mounted above these stacks is a track system on which autonomous, battery-powered vehicles travel to pick up, rearrange and transport the containers individually to the directly connected ports for goods reception and order picking. This eliminates the usual traffic routes and reduces the distances between the individual containers.
Self-Optimizing Processes
This space gain has its price: Unlike in traditional rack warehouses, KLT containers stored further below in the AutoStore can not be controlled directly, but must first be „excavated“ before the actual picking process. To accomplish this task, several transport vehicles work together independently. Through self-optimizing processes, containers with items that are less frequently used continue to sink downwards, while articles with frequent accesses remain at the top and are thus available more quickly. Advance notice in the order buffer allows for timely restacking, so that the ports are permanently supplied.
The result is a system for automatic storage and picking of small parts, which is designed in multi-faceted ways for radical efficiency increase:
Location: Due to the extreme compacting of the storage area, the AutoStore system can achieve a space gain of up to 400%. The modular design configuration and flexible arrangement in the room also facilitate integration into existing building structures and thus ensure high scalability with changing capacities.
Speed: The compact arrangement of KLT containers shortens the paths for the transport robots and enables efficient storage/retrieval performance. With an acceleration of 0.8 m/s2 and a speed of 3.1 m/s, a robot achieves about 25 storage/retrievals per hour. By connecting additional vehicles and ports during operation, the overall efficiency of the system can be increased as needed.
Energy: The vehicles are operated fully electrically and have a module for energy recovery when lowering the containers in a vacated storage space. Their energy consumption is therefore only 0.1 kW/h. When the vehicles are not in use, they drive independently to the charging stations located at the edge of the grid. In addition, power consumption can be scaled by using fewer vehicles in phases with lower throughput.
Reliability: The parallel use of several vehicles per module reduces the failure risk of the entire system to a minimum. If one robot fails, another one takes over its task. This gives AutoStore up to 99.6% uptime.
Radical increase of efficiency
The AutoStore system is thus not just another evolutionary step in automatic small parts logistics, as was the case with storage/retrieval units or autonomous shuttles before. Rather, this technology is a paradigm shift in which the basic principles of storage technology have been freshly reconsidered. On the one hand, this radical increase in efficiency is possible because robots are not only constantly becoming cheaper but also becoming more and more energy-efficient. On the other hand, this is the first time a warehouse has been designed to be operated and used by robots rather than humans.
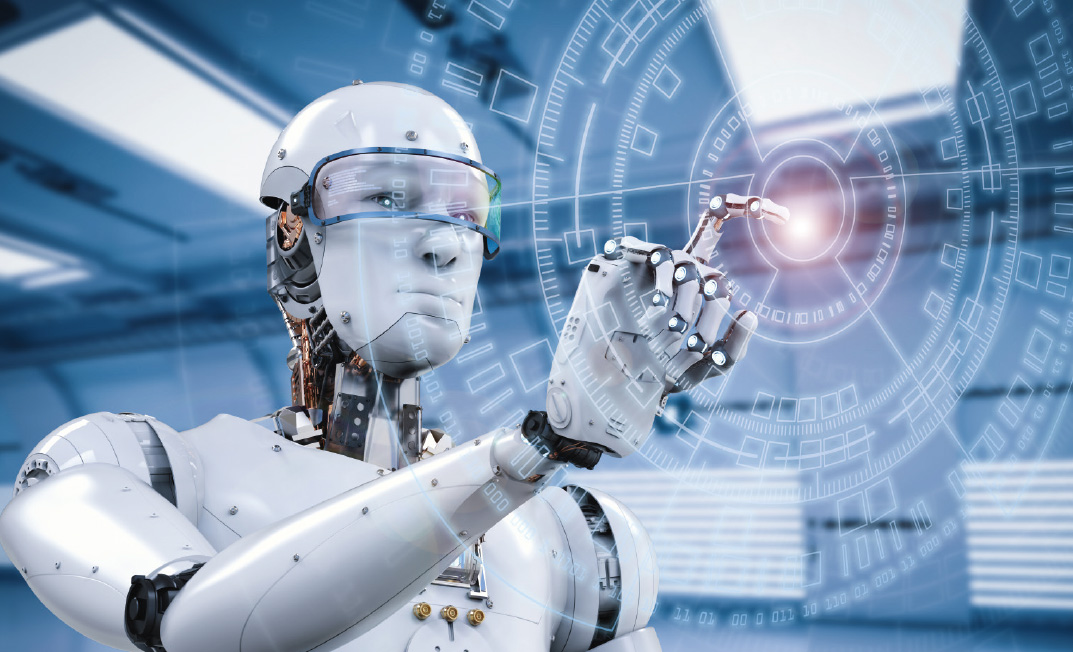