EVERYTHING IN TIME
CONVERSION FROM SHOP FLOOR TO CYCLE ASSEMBLY AT MAPLAN GMBH
Workshop manufacturing continues to be the method of choice for the production of complex products with a wide variety of variants, such as special-purpose machinery. However, the case of MAPLAN GmbH shows how the introduction of the cycle principle can be made possible even in extremely complex manufacturing environments, thus radically reducing throughput times.
When MAPLAN GmbH opened its manufacturing site in Kottingbrunn in 2016, it ventured into unknown territory in two ways. Firstly, because the manufacturer of elastomer injection moulding machines replaced its previous main plant in Ternitz with a completely new factory. On the other hand, because MAPLAN was the first manufacturer in the elastomer sector to implement synchronized flow assembly. Previously, the injection moulding machines and presses were manufactured there exclusively in the stand assembly area, with the majority of the components being brought to the machine at the same time. The changeover to cycle assembly posed an enormous challenge, especially in view of the large number of variants. This is because almost all the systems manufactured at the site are unique, with customer-specific features.
LINE BALANCING USING “ROM“
Due to this high variety of variants, the work contents within the line also vary greatly. In order to ensure clocked assembly despite these fluctuations, ROI first developed and evaluated the optimum assembly process with the help of the ROI Tool ROM®. ROM® - the ROI operation sequence method - is a system of predetermined times, with which a very fast and well-founded determination of best-practice times is possible, which simulate an optimized and waste-free assembly and material supply system, on the basis of the parts list. The information obtained in this way formed the basis for the line balancing and a flexible personnel deployment concept in which the employees are no longer deployed exclusively at a fixed workstation, but are in some cases also on the move with the machine. On the other hand, the intensive examination of each individual component also revealed optimization potential, which was implemented together with the designers.
SELF-CONTROLLING MATERIAL FLOW THANKS TO INTELLIGENT LOGISTICS CONCEPT
In addition, ROI supplied a logistics concept adapted to the new form of assembly, with which an optimum material flow can be ensured from goods receipt to dispatch. This included the direct connection of upstream pre-assembly processes as well as the definition of Kanban replenishment processes. The most important deliveries are automatically sorted upwards by the system and usually made available on an hourly or daily basis. As a result, downtimes could be reduced to a minimum.
MORE SPACE AND SHORTER LEAD TIMES
With the help of the new logistics concept, the storage space could be reduced by about half while at the same time doubling the stock turnover. The measures were also effective in assembly. By switching to cycle manufacturing, the lead time from the start of assembly to delivery to the customer was more than halved from just under a month to twelve days. The original plan was to increase the proportion of machines produced in line with the cycle from initially 30 percent to 70 percent within three years. “After only nine months, we already have a 60 percent share,” says Wolfgang Meyer. With its innovative assembly and logistics concept, the MAPLAN plant in Kottingbrunn took second place in the overall ranking of “Factory 2018” and won the “Green Factory 2018” category. The event is regarded as the most renowned manufacturing competition in Austria and is jointly awarded by Fraunhofer Austria and WEKA Industrie Medien
More at: https://fabrikkonferenz.at/
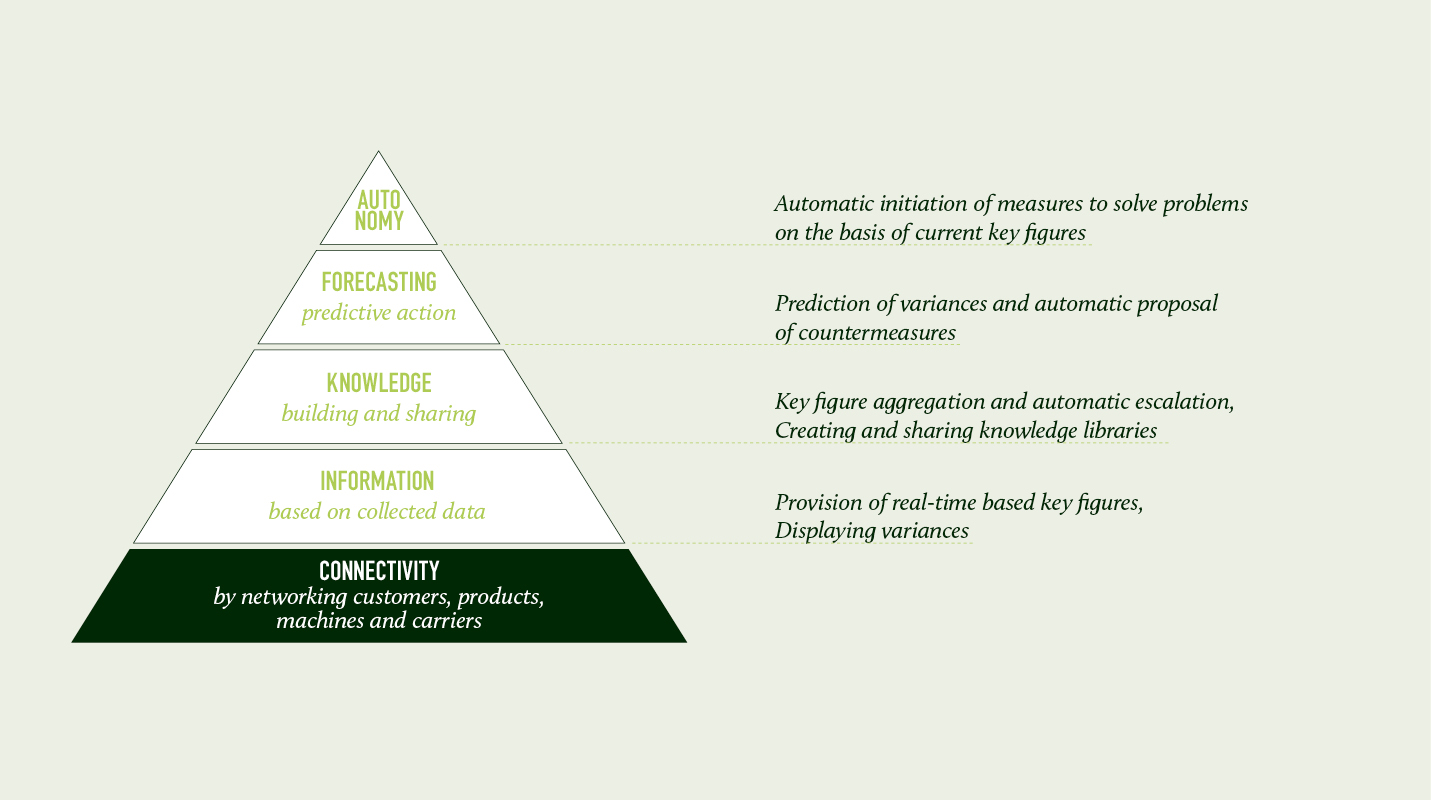
MODULE 4: ROLLOUT AND PROTECTION OF SUSTAINABILITY
THE LONG WAY TO THE ENDURANCE RUNNER
If implemented consistently, Lean Manufacturing is not only a tool for process optimization, but rather a state of continuous improvement. The final vision is a system that combines high process stability with constant experimentation and thus ensures continuous optimization of the manufacturing system. Thus, it is not only a matter of streamlining processes, but also of keeping them “on suspense”.
Achieving this state - and above all securing it in the long term - is a task that extends far beyond the individual areas. In practice, however, responsibility for the continuous further development of processes is often outsourced to the individual employees on the shop floor or in manufacturing-related areas. However, it is impossible for you alone to achieve this. Instead, the companies themselves are required to create the structural prerequisites for a continuous improvement process. This includes various aspects:
Qualification & know-how building
The central prerequisite for the sustainable anchoring of the lean concept in the organization is the development of the company’s own know-how resources. On the one hand, this takes place through the targeted development of junior managers who act as drivers of the topic in the company and anchor the lean concept at management level. On the other hand, by setting up internal qualification infrastructures, for example with the help of train-thetrainer programs.
Internalization & Incentive Systems
In order to promote the anchoring of improvement concepts in the specialist departments and in day-to-day business, additional incentive systems should be created in addition to regular further training programmes in order to motivate employees at all levels to become actively involved in the transformation process. This ranges from individual target agreements to gamification approaches or award concepts.
Scaling & global rollout
Rolling out Lean or OPEX programs in a global plant network requires a centrally controlled, coordinated procedure. Based on a standardized analysis and an internal benchmark of all plants, a framework is set up that the various plants can process in parallel. The use of internal best practices or a control unit approach ensures an agile and flexible procedure and enables rapid optimization of the manufacturing systems in the area. At the same time, the new target systems must be made known to the local operation managers in the local organizations.
Standardization & Global Knowledge Management
In order to ensure an effective exchange between the different locations beyond the roll-out phase, global standards are required that ensure comparability of processes and problem-solving approaches through consolidated key performance indicator systems. The second step is to make the collected process knowledge available globally via appropriate interfaces. Here, too, global knowledge management can be supported by best practice sharing platforms and networking events.
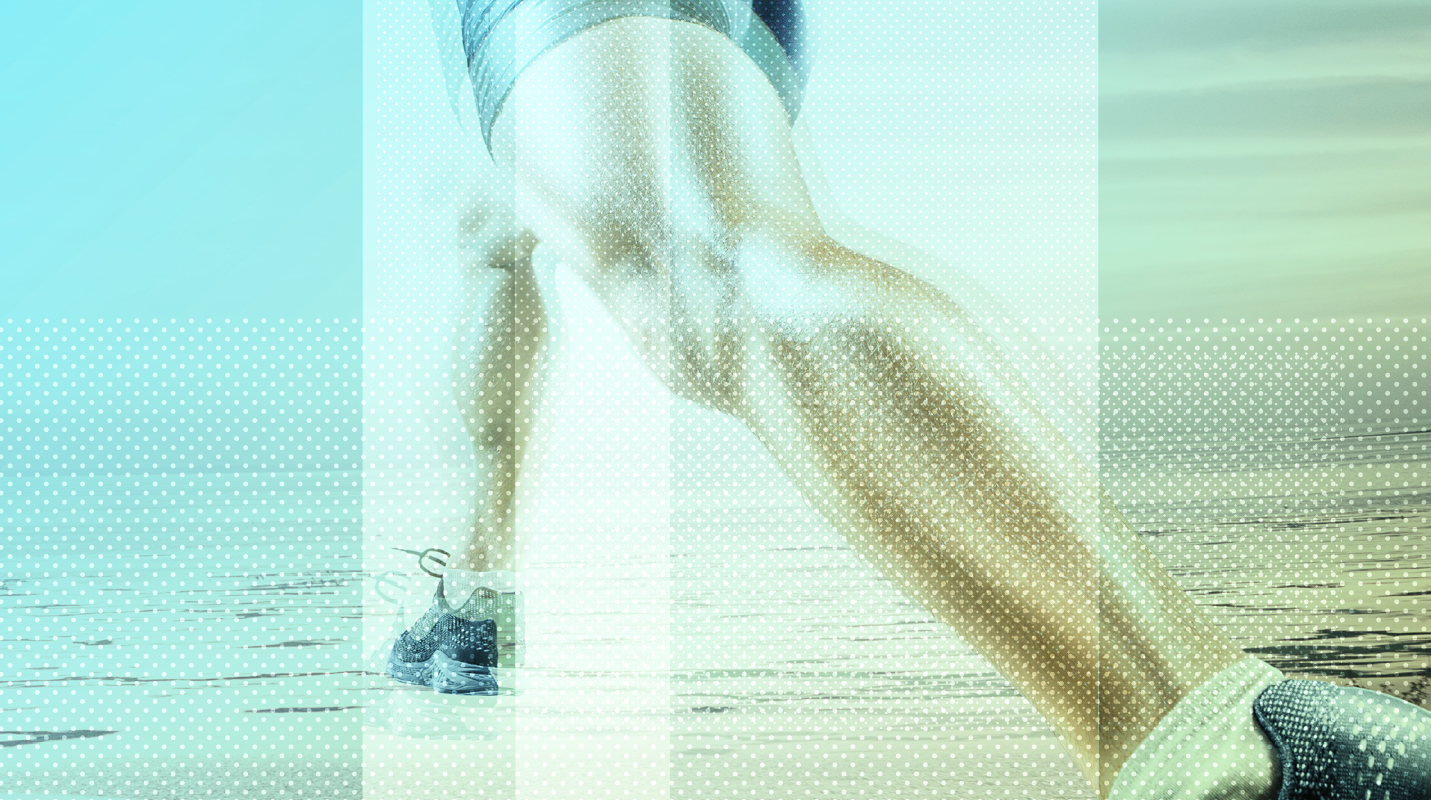