Best practice assembly and logistics
Modern assembly systems are capable of manufacturing complex and multi-variant products at competitive costs. They are capable of individual production and small series and are flexible with regard to fluctuations in the number of pieces. This also applies in a differentiated form to series production.
EFESO management consultancy has the necessary tools at its disposal:
With ROM®, the ROI operation sequence method, a waste-free assembly system is simulated in a short time on the basis of the parts list. Optimal assembly time and potential are thus determined.
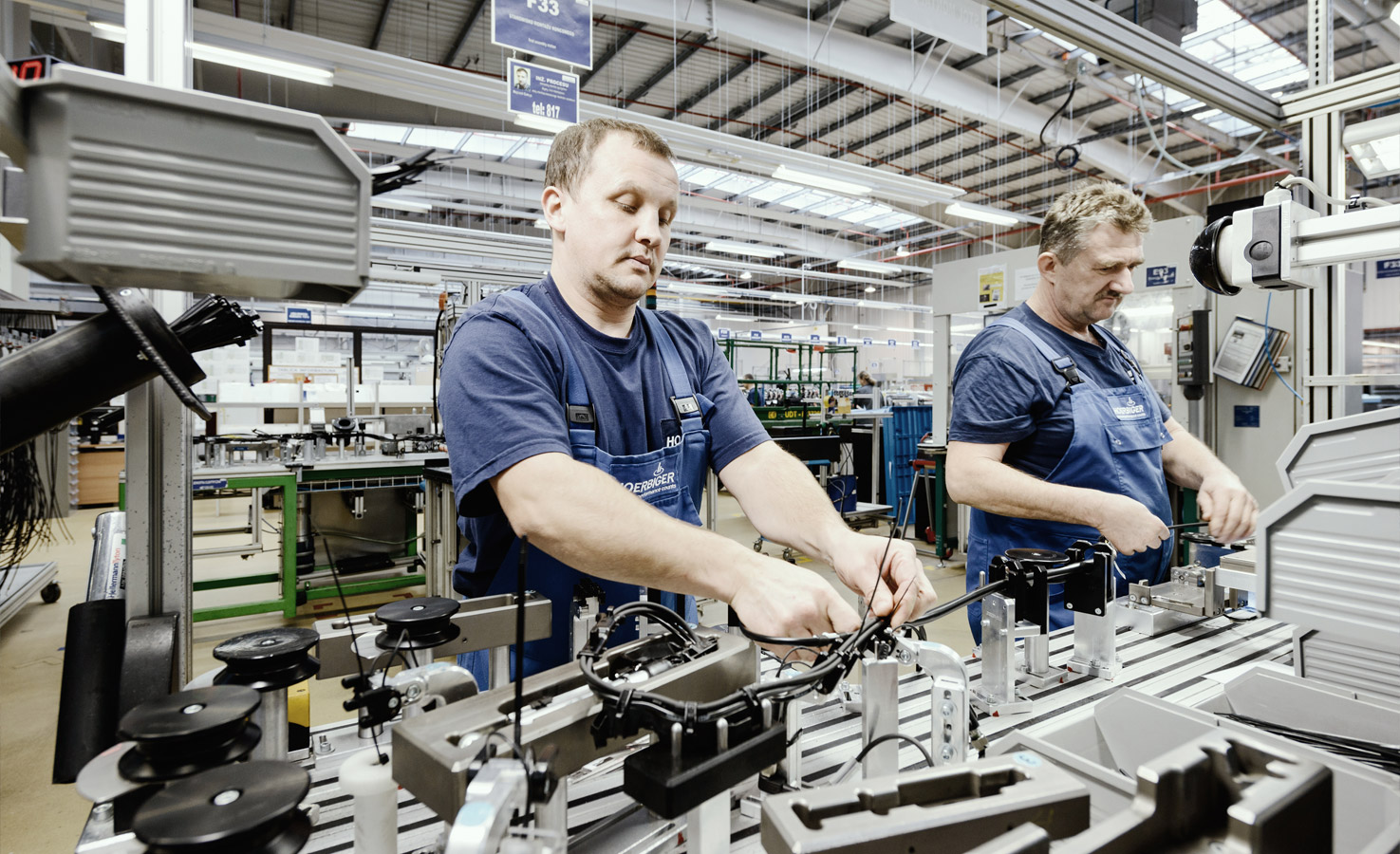
©Boleslawiec
The assembly system itself is developed from a best-practice modular system based on the following basic principles:
- clear separation of assembly and logistics,
- Introduction One-Piece-Flow,
- flexible timing,
- Optimal separation and integration of pre- and final assembly,
- reasonable automation, low cost intelligent automation,
- Use of industry 4.0 technologies,
- Pull principle and flexible retooling in parts supply,
- standardized replenishment processes,
- modular and use-neutral assembly system and workplace design,
- team-oriented and capacity flexible organizational concepts
- Ergonomically designed workplaces
- Electric forklift vs. diesel forklift (CO2 issue)
- Digitalisation as the basis for efficient and thus resource-saving processes
- Occupational safety (accidents, hazardous substances, ...)
In addition, ROM® can provide valuable input on aspects relevant to production and assembly which should already be taken into account in the product design phase.