![[Translate to English:] [Translate to English:]](/fileadmin/_processed_/d/2/csm_AdobeStock_179043222_Molkerei_Headerbild_df2727764e.jpg)
Cushioning cost pressure with energy management
A dairy group maps sustainability potential in MWh and CapEx
In order to soften the cost pressure of its energy-intensive production, a dairy group defined new energy-saving measures for one of its plants. The particular challenge: to obtain a decision-ready overview of options for action in a short space of time, quantifying the savings potential both in MWh (megawatt hours) and in EUR.
Together with EFESO, the company identified suitable measures in an assessment. Within five weeks, it received an overview of their effectiveness in terms of CapEx (Capital Expenditures), amortization period and other key figures.
Challenge
A dairy group has identified energy efficiency as a lever to cushion the cost pressure from falling production volumes. In a plant with exemplary energy management, further measures with detailed savings potential are now being identified.
MOREEFESO solution approach
In an assessment, the project team determined potential energy efficiency projects and the maturity level of energy management at the site. The management received a longlist of 40 efficiency levers, which specifically quantified the potential of the measures in terms of savings, CapEx, and amortization.
MORELessons learned
A systematic selection and an approach based on the Pareto principle make it easier to quickly focus on the most effective measures. This prevents bad investments and avoids dealing with unimportant details.
MOREEFESO success model
EFESO's “Active Energy Management” approach shows, how further potential in energy efficiency can be activated beyond the project example. This expands the scope for action beyond technologies.
MOREEnergy efficiency as a cost lever
With around 20 international production sites, the company is one of the largest dairy groups in the world. The products are exported to over 70 countries and undergo extensive processing, for example for homogenization or to ensure shelf life over longer periods of time. This requires complex, large-scale and energy-intensive machines and production facilities in which the raw materials and end products are heated and cooled.
Under these conditions, there is no alternative to producing food at high capacity – if volumes fall, the cost pressure from operating, cleaning and maintaining the systems increases. In addition, energy efficiency measures no longer help once volumes have been lost. The dairy group already had this scenario in mind and took various measures to counteract it.
The objective: transparency about the financial impact of energy management.
Exemplary energy management as a starting point
Several plants had already identified energy efficiency as an option for reducing costs but were not yet exploiting the full potential of this approach. One production site in Europe was now to act as a “lighthouse project”. It was to show how the most effective starting points for energy consumption savings could be identified throughout the plant. Suitable measures were also identified and evaluated for possible implementation. This approach is therefore suitable as a “best practice” for other sites.
A living culture of improvement
The group management selected the plant with his two production lines as a “lighthouse”, because its top management had already been actively pursuing energy-efficient management as an important task for years. This not only resulted in solutions at a high level in some cases. The site also continuously addressed opportunities for improvement: in an “energy circle”, managers from several organizational areas regularly defined and monitored the plant's energy targets (KPIs), decided on measures and followed up on their implementation.
As the relevant expertise developed over time, the plant already achieved good results at the start of the collaboration with EFESO. The team at the plant not only dealt with classic issues such as waste heat recovery and reduced the overall energy requirement by around 20 %. The site also took advantage of negative electricity prices through load management. In addition, the workforce was made aware of the topic of energy efficiency through regular training sessions. So, the employees were motivated and empowered to actively participate.
A critical view from the outside
The “energy circle” wanted to continue this already exemplary initial situation with further successes. Together with the plant management, it decided to reflect on the existing knowledge and the status achieved with the independent, critical view of an industry-experienced management consultancy. It was also necessary to identify further measures as cost-cutting options and to prepare these as a decision paper for the company management as follows:
- Specification: what amount will a measure save over what period of time? How are the amortization period and CapEx quantified?
- Prioritization: which measure is particularly effective based on which investments and results?
This is where EFESO came into play as an industry-experienced partner in solving operational challenges. The EFESO consultants contributed their expertise from the implementation of cost reduction and sustainability programs to the joint project team with those responsible for the dairy site.
Merging the environmental and CapEx perspectives
In this case, the project focused on an energy assessment at the lighthouse plant with two main directs:
1) Identification of energy efficiency projects. The project team gained an overview of the processes at the plant during a site visit – and discussed possible new approaches to reducing energy consumption constructively from the outset. The results were an initial, rough estimate of feasibility and business cases for the implementation of measures (see examples).
2) Determination of the maturity level of energy management. To this end, the project team recorded which data on energy consumption is collected when and how. This also showed that the workforce actively collected and shared such information with a high level of initiative to achieve improvements.
Four measures were responsible for 75% of the recorded cost savings and accounted for 70% of CapEx.
Prioritization of cost reduction levers
As a result of the assessment, EFESO drew up a detailed list of 40 measures to reduce costs in the plant's energy management. The project team evaluated each measure with key figures on how much energy and money it could save – and over what period of time investment costs would be amortized, e.g., for new systems or a technological upgrade of the existing machines and energy infrastructure.
This enabled the company not only to quickly identify the range of improvement options, but also to prioritize them – based on their impact on energy costs and their CapEx:
- Effectiveness: Four measures proved to be responsible for 75% of the recorded cost savings and together accounted for 70% of the CapEx. In particular, the use of a combined heat and power plant offered great potential with a payback period of two years.
- Amortization period < three years: A further 15% of the total cost savings could be realized through projects with a term of less than three years. The project team identified reducing the compressed air pressure in the high-pressure compressed air network and changing the pressure of the feed water pump as particularly productive starting points for reducing costs.
- Amortization period > three years: The remaining measures addressed 10% of the possible savings but require more time to implement. These included, for example, the optimization of heat management in a glass rinsing system or the insulation of steam pipes.
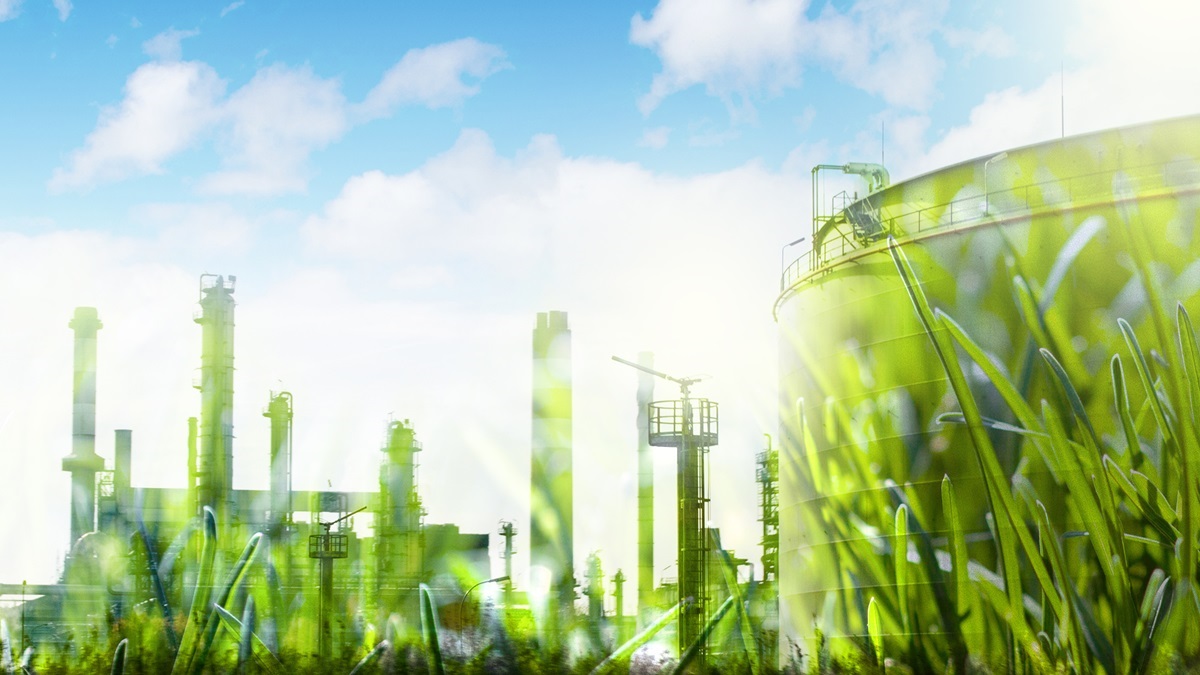
Measure:
- Construction of a combined heat and power plant to generate electricity and heat.
- Hot water generation through additional heat recovery from the exhaust gases produced.
Forecast:
- Financial savings: approx. EUR 820,000 p.a.
- CapEx: EUR 1.5 million
- Implementation period: 1 to 2 years
- Amortization period: 2.5 years
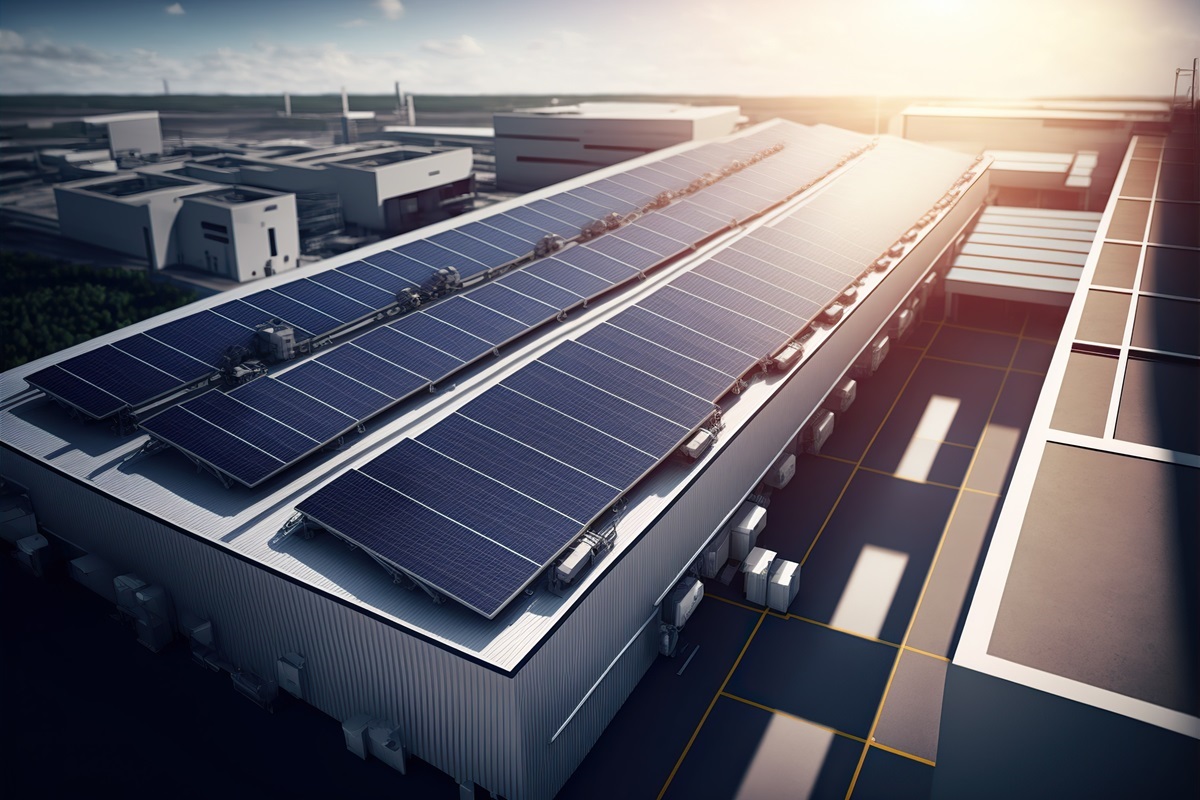
Measure:
- Construction of a new photovoltaic system to generate electricity.
- Enables partial decoupling of the plant's own electricity requirements from the electricity price.
Forecast:
- Financial savings: approx. EUR 450,000 p.a.
- CapEx: EUR 2.5 million
- Implementation period: 6 to 12 months
- Amortization period: 5.5 years
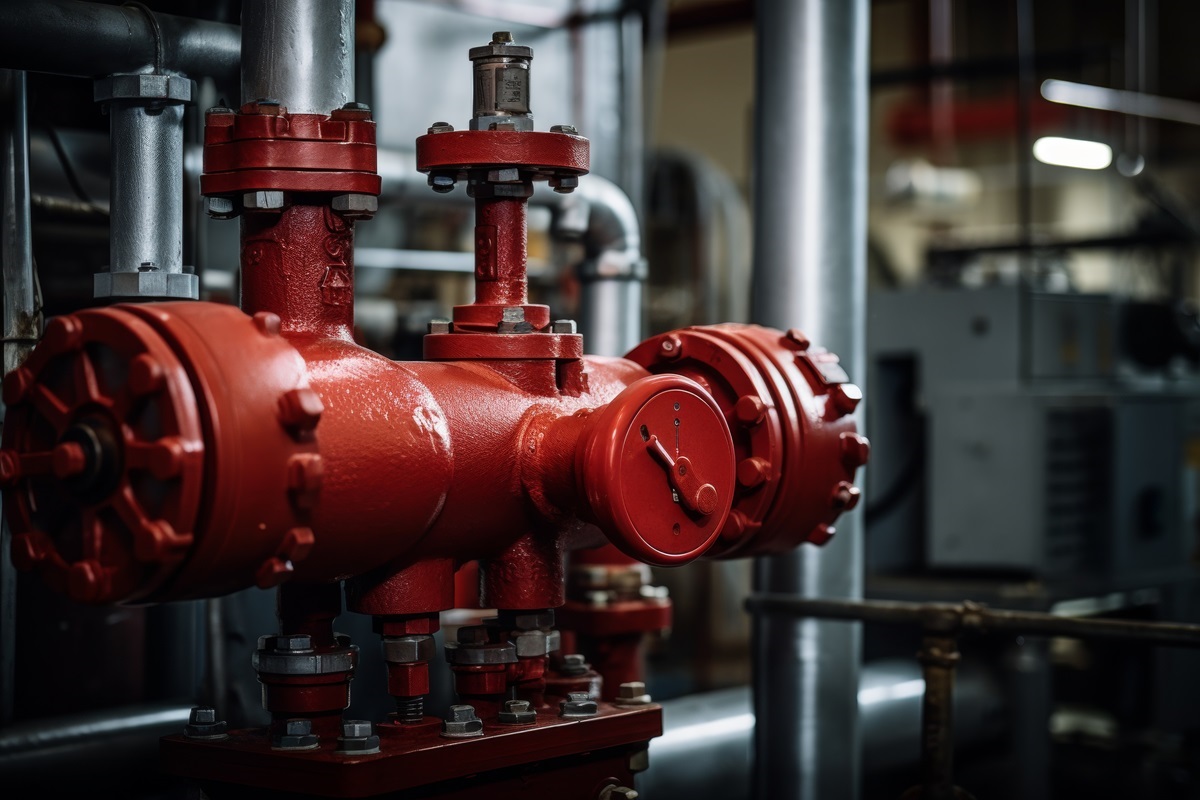
Measure:
- Use of maintenance-free steam traps with a 10-year guarantee instead of mechanical traps
- Reduction of steam losses.
Forecast:
- Financial savings: approx. EUR 250,000 p.a.
- CapEx: EUR 100,000
- Implementation period: 3 to 6 months
- Amortization period: 0.5 years
Focus on the most effective changes
Regardless of the plant and industry-specific starting conditions, these approaches are recommended in energy management assessments:
Go from the “big picture” to the details – not the other way around!
In this case, the assessment started in an ideal situation. The team at the plant had already acquired a great deal of expertise and was highly motivated to pursue opportunities for improvement. However, there was a risk of getting lost in implementation details or not correctly assessing the actual benefits or profitability of measures and technologies.
When discussing options for reducing energy or costs, a “big picture” overview of the collected measures should first be drawn up and roughly divided into a few blocks according to their estimated effectiveness (e.g., savings potential > 50%, < 50%, 5-10%). This simplifies the sorting and prioritization of measures and avoids a time-consuming discussion of detailed questions about ultimately unimportant “levers” in the subsequent steps.
Evaluate the measures according to the Pareto principle!
The Pareto principle is also a useful guideline for prioritizing measures in energy management: How can 80% of the targeted savings be achieved with 20% of the total expenditure? Which measures require a high implementation / cost effort, but produce comparatively unimportant results? This simple subdivision helps to quickly find the most effective levers.
In this case, the amortization period was also used as a selection criterion – all measures that would have taken more than three years to implement were eliminated. However, this does not automatically make the measure unsuitable. In the case of further technological development, it may be worth reassessing its suitability after one or two years.
Optimal energy management is not limited to buildings, machines, and systems.
Active Energy Management: Expanding the scope of action beyond technologies
In this case study, the focus was on the assessment in order to quickly show the potential in a plant. The dairy group also tested a methodology that validates the environmental and financial dimensions of energy management and can be applied to other sites.
Energy management can of course go beyond purely technical measures to save further energy costs. Ideally, the focus should not only be on technological issues and solutions, but also on identifying potential for improvement in other dimensions. EFESO pursues an “Active Energy Management” approach with four key areas:
1) Energy strategy: This includes, for example, setting “energy efficiency” as a top management issue, cascading plant targets to other areas of the company and defining an annual action plan to strategically drive the issue forward.
2) Integration with Operational Excellence (OPEX): Main parts are the definition and monitoring of energy KPIs and their integration into the shop floor management.
3) Digital & Data: A central element here can be, for example, the use of sensors with a high level of aggregation of sensor data in KPIs. Furthermore, a digitalization strategy is recommendable.
4) Human dynamics: Raising staff awareness of energy efficiency is just as critical to success in this field as cross-functional cooperation within the energy management team.
These four focal points provide the guidelines for effective long-term energy management. The implementation plan for “Active Energy Management” can then be designed according to the company's needs – for example, by synchronizing the savings / cost reduction measures with those of digitalization and automation.