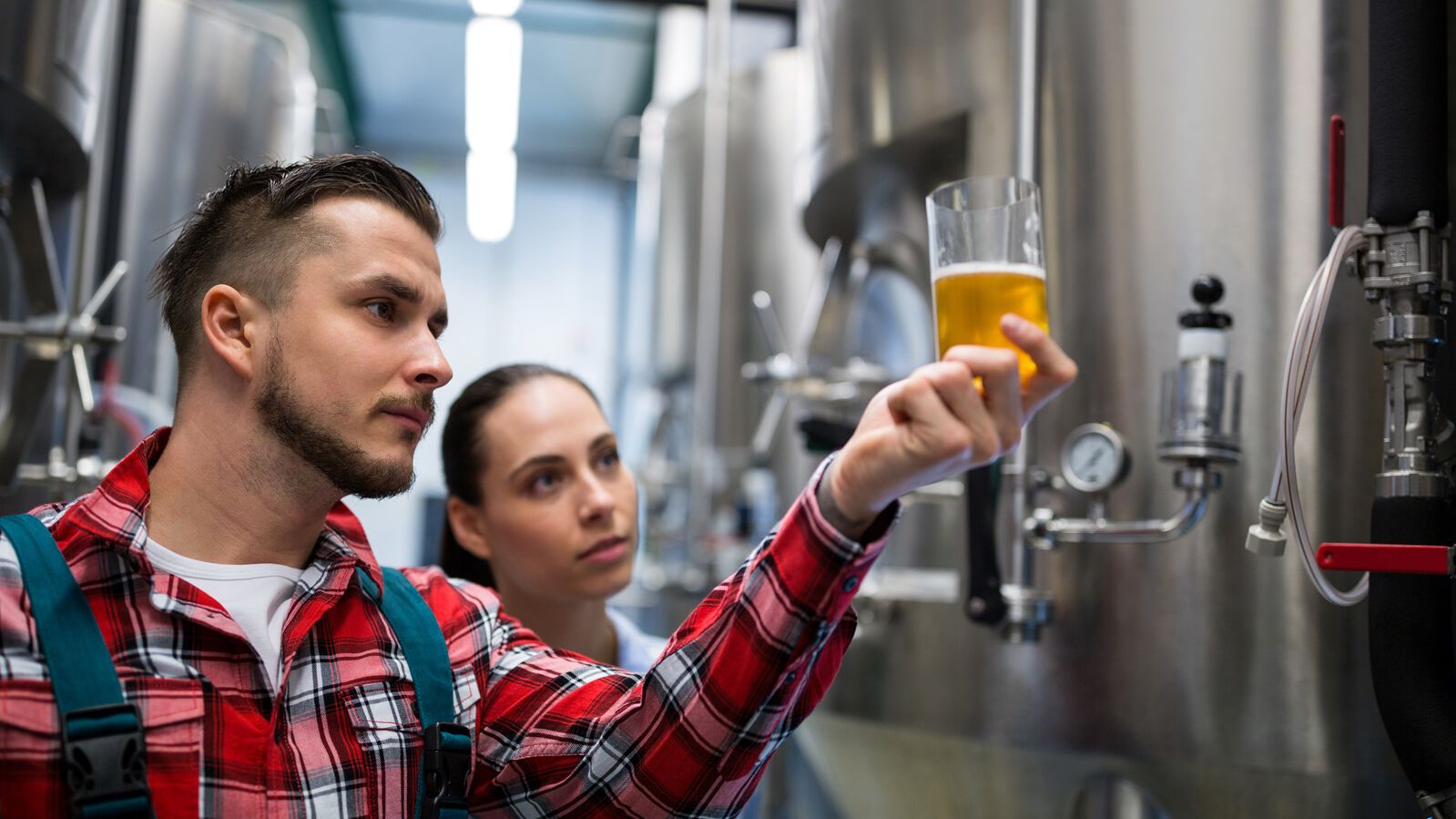
A two-track road to operational excellence
Realignment of a global brewery network with OPEX / WCOM*
With a company network of more than 150 breweries in 70 countries around the world, a leader in the brewery sector decided to launch a global continuous improvement initiative. There were two main objectives: on the one hand, cost efficiency improvements had to be achieved in the companies in order to realize new acquisitions. On the other hand, a common, standardized way of working was to optimize global supply chain processes.
Together with EFESO, the beverage manufacturer developed and implemented a customized *OPEX (Operational Excellence) / WCOM (World Class Operations Management) program. The special challenge: to find a "common sense" for the further development of the different organizational and management cultures in the individual locations. And, building on this, to establish an effective, standardizable set of methods for continuous improvement.
EFESO solution approach
For EFESO, this project was the starting point of his own WCOM approach. With a standardized set of measures, WCOM was successfully anchored in the organization worldwide.
MORELessons learned
Close cooperation with the EFESO country teams made it possible to get the employees in the locations excited about WCOM. Furthermore, an understanding of the cultural dimension of the work is just as important as professional operations knowledge.
MOREEFESO success model
By accelerating the WCOM / OPEX approach, the company doubled his productivity and reduced variable costs by 35%. This was contributing to supply chain savings of €400 million.
MOREIncreasing performance on the brewery's shop floor
Before starting the project with EFESO, the brewery group pursued various approaches with an in-house consulting team, e.g. to reduce costs in production, minimize risks in the supply chain or streamline processes. They used classical methods like deep assessments in the factory lines, which was followed by detailed instructions for improvements in theory and low results in practice.
At this point, the company realized that it could make better use of its existing strengths with new perspectives on organizational development. In a pilot project with EFESO in a South American plant, it tested what could be achieved with a WCOM program: in a couple of months, the project team of employees and EFESO consultants increased the Overall Equipment Effectiveness (OEE) of the lines significantly by making maintenance more effective.
During a plant visit to this project, the management from the European headquarters saw for themselves how effectively and sustainably the WCOM program was working. In addition to the clear performance increase in the pilot line's KPIs, the employees were enthusiastic about the new work processes – and highly motivated to pass on their experiences as "best practice" to other lines and plants.
Accordingly, the brewery group quickly recognized the enormous potential of the WCOM approach and commissioned EFESO to continue the success story of the pilot project at other sites around the world. As the company acquired beer brands in Asia, Africa and other locations in the following years, the timing of the project launch proved to be ideal.
The brewery doubled the productivity of its factories within one year.
Beverage company benefits from automotive WCOM best practices
To fulfill this mission, the project team used an approach that EFESO had previously developed at an automotive supplier and successfully established at its plants around the world. This was based on the Japanese Total Productive Maintenance (TPM) approach. By adapting those best practices for its operational systems and methods, the brewery group doubled the productivity of its factories within one year – and for EFESO, it was the starting point of his own WCOM approach.
In such cross-continent and cross-cultural projects, an implementation partner has to provide at least two very important qualifications: Firstly, to develop a standardized set of methods and implementation measures for the plants. Secondly, to be able to communicate this in the respective national language and establish it in employee training. The EFESO project team pursued the following WCOM (World Class Operations Management) approach with the beverage company as a "two-track" path to achieving the goals:
Direction of impact I: WCOM within the factory
- Zero-loss principle: The WCOM approach developed by EFESO is based on the zero-loss principle and comprises the dimensions of loss recognition, loss elimination and loss avoidance. The knowledge of all losses and their value helped the company to make the right decisions on the most effective starting points for improvements. Together, the appropriate tool set was developed to minimize or eliminate these losses.
- OPEX capability: At the same time, a corresponding OPEX system was set up step by step and in co-operation with all the key operational levels. The focus was not only on the technology-supported further development of processes and IT / OT systems. Equally important was to empower employees to use these processes and systems on a day-to-day basis – and to be able and willing to drive continuous improvement independently in the long term.
As a result, the company was able to significantly increase OEE by 20% across the entire plant network. It also reduced material waste by almost a quarter.
The company tackled more than 20,000 improvement projects worldwide.
Direction of impact II: WCOM beyond the factory
During the initial phase of the project, the company recognized that EFESO's WCOM program could unlock potential beyond plant and country boundaries. It therefore expanded its focus to improvements in the entire global supply chain network and added the following phases and elements to the program:
- Strategy / roadmap: The project team developed a clear strategic storyline ("Why") and combined this with solid governance ("How, Who and When"). This played a key role in ensuring the effective and efficient implementation of the individual improvement projects ("What") in the operations areas. A key element proved to be a group-wide roadmap that combined the program objectives with the overarching corporate strategy.
- Implementation / toolkit: As in the case of the WCOM program for production, the other WCOM programs for the value creation network also started at pilot locations and were eventually transferred company wide. All local projects used a toolkit with tailored, standardized methods and (IT) tools in the respective national languages. In total, the company tackled more than 20,000 improvement projects worldwide.
- Further development / best practices: The brewery group closely monitored the progress made in implementing the program at the respective locations. The OPEX / WCOM know-how was not only imparted through training measures in which best practices were used, for example. It was also integrated into the employees' day-to-day work according to the "train-the-trainer" principle in such a way that independent implementation of the program was made possible in all areas and levels of the organization.
Communicating value creation standards internationally
When implementing the points described above, the following empirical values proved to be particularly critical to the success of the entire project:
Show presence and convey passion – in the local language.
When creating the toolkits, the focus was not on technologies. Rather, the aim was to standardize functioning Lean / TPM methods in such a way that the WCOM implementation could be carried out uniformly in the respective national language at all locations worldwide. During this implementation phase, the presence of the EFESO consultants from the respective country teams proved to be an important success factor: they were on site in the production lines for one or two days over a longer period of time, so that a common team spirit with the brewery staff quickly developed.
Consider perspectives from the shop floor to the management board.
An understanding of the cultural dimension of the work is just as important as professional operations knowledge. It is not enough to get individual teams or units of the organization excited about WCOM / OPEX – this should be achieved "across the board". The team took the successful communication between all hierarchical levels with them as a valuable experience. From day one, the right storyline and the right arguments were used to communicate with all key employees – from machine operators to the CEO.
Develop the right measurement tools for progress!
Before the project started, the company had an audit system for quality, maintenance and the management of complex production and logistics processes. Such systems are indispensable for monitoring progress and making the causes of errors and successes tangible. In this project, the perspective was deliberately changed completely: Rather than following a “top-down” approach of the corporate headquarters, the local sites developed their best practice solutions for safety, quality, maintenance, planning, etc. The entire company benefits from their exchange across locations and countries as part of the WCOM / OPEX program.
The company achieved savings of €400 million in the supply chain.
WCOM empowerment for the present and future
The company established a culture of continuous improvement throughout its entire supply chain organization and in the 150 breweries that consistently implemented the jointly developed program. The key success factors in this case were:
- The creation of a tailored, standardizable "framework" for the Operational Excellence / WCOM program with EFESO and the joint, step-by-step introduction of the program in the operating units.
- The joint elaboration of a methodical toolbox with all important fields of action in production and logistics (see graphic with examples).
- The development and implementation of on-the-job training for thousands of employees on WCOM / OPEX methods to enable the teams at the sites to independently introduce WCOM in new units or acquired plants. The plant management also used theoretical and practical training on change management.
The project results prove how effective this approach has been for the brewery group: in the first eight years of the program's implementation, productivity doubled and fixed and variable costs were reduced by 35%, contributing to supply chain savings of €400 million. Perhaps the most important advantage, however, is the forward-looking nature of EFESO's approach: thanks to the targeted training of around 700 employees, the company can constantly drive forward the continuous improvement of its production and logistics.