We establish a management system with OPEX managers in the organization that defines the goals of the OPEX initiatives in order to implement the site strategy. The results are recorded daily in shop floor management; effective measures are implemented together with the operational areas and transferred into standards for continuous improvement. Through regular checks (daily, weekly, monthly), executives and OPEX managers ensure that these standards are followed and continuously developed.
CONSULTING FOR OPERATIONAL EXCELLENCE
Establishing OPEX and WCOM™ in the company
Companies achieve Operational Excellence (OPEX) by aligning their structures, leadership, processes, technologies, and cultural characteristics towards continuous improvement. This requires:
- A clear strategic target for the direction of further development.
- A consistent increase in efficiency in direct and indirect corporate functions. This primarily affects production, assembly, logistics, maintenance, quality assurance, IT, purchasing and R&D processes.
- Strict reduction and elimination of waste. This contributes to a significant improvement in performance and KPIs, for example, in meeting sustainability targets.
- Enabling the organization to continuously improve, e.g., by systematically linking the management of short- and long-term OPEX activities (see “Infinite Loop”).
With EFESO's OPEX approach, companies realize short-term results improvements and systematically develop their entire organization's maturity level towards excellence. Our OPEX programs achieve average savings of 5:1 to 10:1 in project costs.
Our approach is designed to enable our clients to realize the improvements independently and further develop their OPEX maturity. When working with EFESO, companies benefit from the following:
Measurable results
Effective performance enhancement and empowerment
We enable our customers to achieve independent, continuous improvement. In doing so, we do not limit ourselves to the application of method kits but instead anchor an OPEX management system within three months, for example, in pilot projects about centerlining, set-up, etc.
According to the “tandem principle”, the company should use the results achieved as quickly as possible and further develop the OPEX system introduced independently. Initially, we increase performance and anchor the results in shop floor management. In the first few weeks, we provide intensive support to employees with our OPEX expertise. Over time, we switch to the role of collaborating expert - and then usually retire to the role of coach within a few months.
In contrast to other consulting approaches, we create long-term added value: every employee should not only learn the OPEX approach but also experience it and implement it independently. In this way, we anchor the topic of OPEX sustainably in the work processes and the organizational culture.
Broader perspective
We use our OPEX system to sharpen employees' perception of effectiveness and efficiency. In doing so, we broaden the horizon beyond the usual OPEX topics to other transformation fields such as:
- IT / OT architectures and automation in manufacturing.
- Networking and improving workflows in product development, production and logistics.
- Global footprint management with future-oriented technologies such as a supply chain tower.
- Establishing and further developing production sites as part of a Future Factory initiative.
Best-practice case studies with real solutions are an integral part of our OPEX programs. Here, our customers benefit from the extensive operations expertise of the EFESO team from projects on Lean Management, Industrial Sustainability, Future Factory and much more.
Long-lasting qualification
Qualifying employees in all roles and / or positions is a central component of EFESO's OPEX projects. Right from the start, we provide intensive training to enable employees to actively participate in the project. Trainers from our Learning Campus and our Transformation & Leadership team contribute with in-depth technical expertise from comparable industry projects. For example, we support companies in the design, development, and go-live of an in-house academy that meets OPEX's training needs.
The goal of the training initiatives is to cultivate a mindset and behavior among employees at all levels that fosters a passion for operational enhancements. The focus is always on the learning success of the employees: for example, we qualify key personnel in the company through training and onboarding in the train-the-trainer approach. This creates a foundation for sustainable knowledge transfer and builds up own resources to operate an in-house academy.
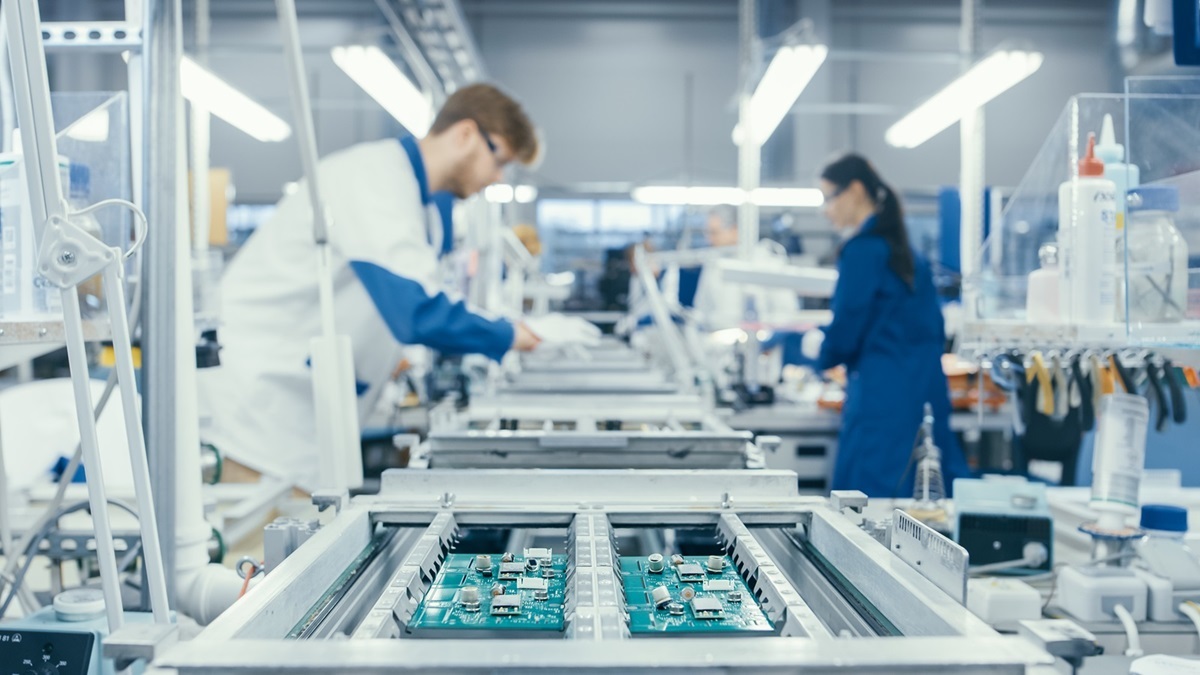
In some manufacturing companies, improving the setup process proves to be a suitable pilot project for achieving significant results quickly. In this case, we make the topic of OPEX tangible with:
- Training the project team in setup optimization methods. We focus primarily on experience-based and practical formats such as learning simulations.
- Analysis of the setup process, identification of errors and opportunities for improvement.
- Definition of a new standard (setup plan with target values for set-up time) based on the expertise of employees and OPEX experts.
- Anchoring the standard in the daily control routines of shop floor management.
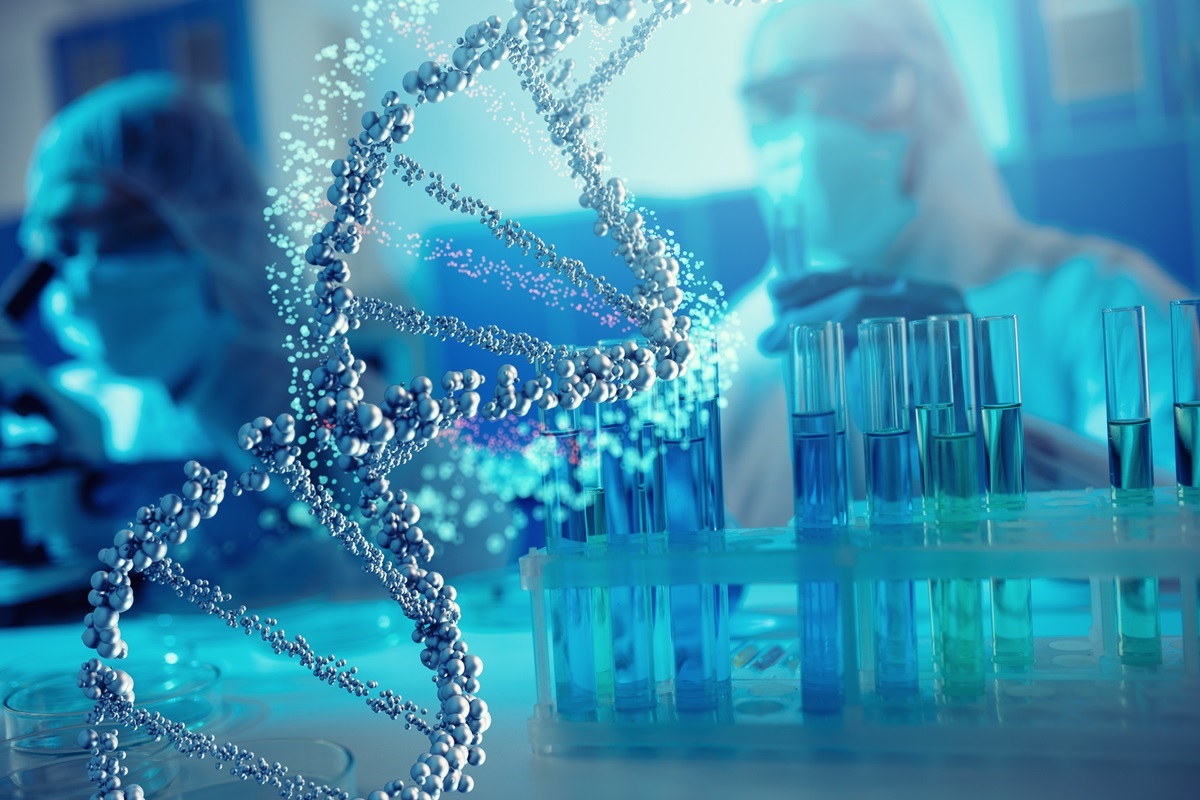
We developed a WCOM 4.0 concept for a company in the chemical industry. One of the tasks was to identify added value that could be realized through digitalization. Results were e.g:
- Up to 10% increase in OEE through the use of digital support.
- 55-10% reduction in losses through automated Q data processing.
- Reduction of manual effort through the integration of digital tools.
OPEX as a management system
We are pioneers and companions for industrial companies on the path to Operational Excellence. We particularly apply our expertise to these tasks:
- Design / further development of processes and structures.
- Definition, selection and implementation of suitable technologies.
- Design of role-appropriate leadership behavior and positive team dynamics.
- Design of communication: creation of suitable infrastructure, realization of change communication.
EFESO's “Infinite Loop” visualizes how we work with companies to implement a fixed process of realizing and securing improvements. This ...
- ... prevents the failure of improvement initiatives;
- ... establishes standards to minimize losses;
- ... makes losses and the gaps to the target KPIs transparent;
- ... communicates the OPEX standard and control mechanisms for compliance to employees from the line to the management;
- .... shows in the shift, daily and weekly meetings what measures need to be taken in the event of deviations;
- ... is continuously repeated as a cycle for KPIs where there is a gap to the target.
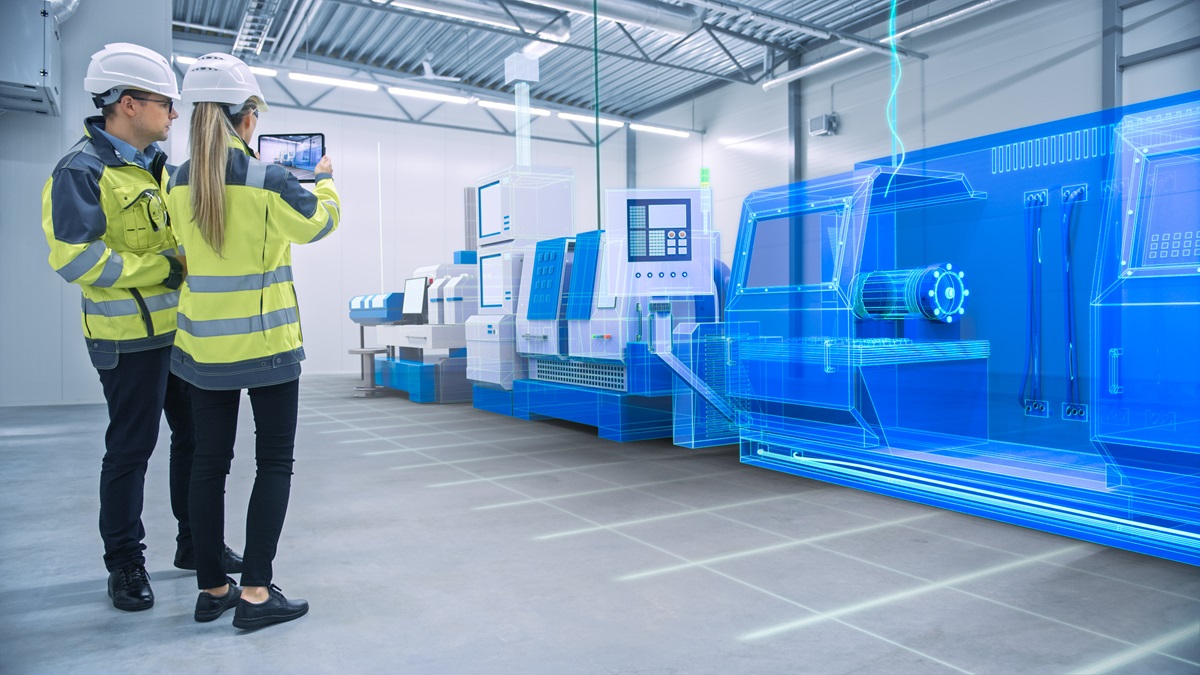
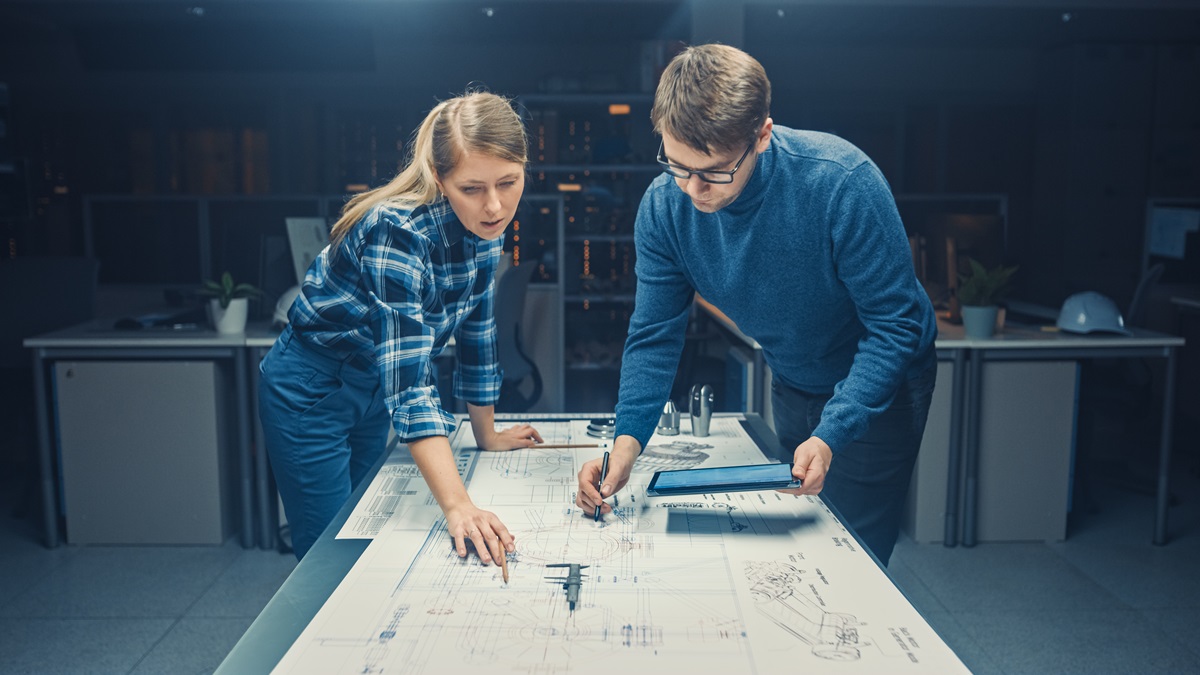
Achieving top performance: WCOM™ in the industry
EFESO has built up its OPEX expertise over more than 40 years with corresponding projects in various sectors of the manufacturing industry. EFESO's World Class Operations Management (WCOM™) approach forms a key basis for this. This methodology for OPEX implementation is based on approaches such as TPM, Lean and Six Sigma and is recognized by the Japan Institute of Plant Maintenance (JIPM). More than 70 EFESO customers around the world have received the prestigious JIPM Award to date.
Operational Excellence & WCOM™ in the factory
Our WCOM™ approach is based on the zero-loss principle. This comprises three dimensions: Loss Detection, Loss Elimination and Loss Prevention. Understanding all losses and their values helps our clients make informed decisions on where to begin improvements. We also work together to identify the appropriate methods and tools to minimize or eliminate these losses.
In this context, our customers also realize their Total Productive Maintenance (TPM) / Maintenance Excellence goals, for example, so that the Overall Equipment Effectiveness (OEE) improves.
The development of a corresponding OPEX system takes place gradually and cooperatively with all levels of the company. The focus here is not only on the technology-supported further development of processes and IT / OT systems. We assign just as much importance to empowering employees to develop these processes and systems on a permanent basis.
Operational Excellence & WCOM™ in the company
The WCOM™ approach provides a solid OPEX strategy for further developing the entire organization – even across locations and countries. It combines a clear strategic storyline (“why”) with solid governance (“how, who and when”) to ensure effective and efficient implementation of projects (“what”).
In this variant of our OPEX programs, the program objectives are usually first aligned with the corporate strategy, which can form the basis for a group-wide roadmap. The programs start at pilot sites and are then rolled out across the company. All local projects use a “toolkit” with tailored, standardized methods and (IT) tools in the respective national languages.
After a brief assessment of the initial situation, the program's implementation at the respective locations is closely monitored. A training academy tailored to the company often plays a key role in quickly imparting the OPEX / WCOM™ know-how and enabling independent program implementation at all levels.
Acting with the future in mind: combining digitalization and OPEX initiatives
By combining digitalization and Industry 4.0 in an Operational Excellence approach, companies can achieve more results in less time. Together with EFESO, they can check, for example, whether their IT and OT infrastructure is generating the desired or necessary data required in the context of OPEX programs. Once again, the priority here is to empower employees to live an OPEX culture in their day-to-day work – as a necessary basis for digitization success.
We always extend the perspective for improvements beyond the status quo into the future, such as through data analytics and predictive models for maintenance or quality, simplifying decision-making. We also identify fields of application for Robot Process Automation (RPA), ONE Digital Twin, Artificial Intelligence (AI) and other pioneering technologies of the Future Factory.
Christopher Borgmann, WAM Digital Transformation Manager at Armacell, and Christopher Martin, Senior Manager at EFESO, present a practical example of WCOM 4.0 in an expert interview for produktion.de.
WCOM™ meets Digitalization: WCOM™ 4.0
As they continue to develop, companies are sometimes confronted with the fact that they are reaching their "limits" in WCOM™ improvements, if they have largely exploited the potential of the traditional approach. At the same time, digitalization initiatives can come under scrutiny if progress is visible in individual solutions, but overall expectations for results are not met.
Building your WCOM™ 4.0 with EFESO
Combining WCOM™ and Digitalization into one integrated program can solve these challenges and can elevate your organization to the next level. Streamline and connect the best of both worlds with EFESO’s WCOM 4.0 approach.
- Performance boost: Double-digit improvements and higher speed in SQDC KPIs year over year.
- Increased ROI: Higher payback on investment in personnel and technology.
- Reduced Complexity: Consolidation of WCOM & Digitalization in ONE integrated program.
We are driving this forward via two points: By Digitized Operations Processes, we enhance value-adding and support processes in the factory. By an Digitized WCOM™ System, we boost Operational Excellence work processes and program management.
To achive these and more results, we support you with our unique offering of capabilities:
DIGITALIZATION & INDUSTRY 4.0
- EFESO is Europe’s leading consultancy for industrial digitalization.
- End-to-end expertise from digitalization strategy to implementation.
- Access to Top benchmarks in digitalization through the prestigious INDUSTRIE 4.0 AWARD.
- Extensive experience and best-practice database from hundreds of projects.
LEADERSHIP & CHANGE
- Developing authentic leaders for successful change in digital environments.
- Sustainable anchoring of change by mobilizing the organization at all levels.
WCOM™ / OPERATIONAL EXCELLENCE
- One of the most comprehensive operations management system frameworks.
- 40+ years of implementation experience in thousands of sites around the globe.
- 100+ of our clients have achieved World Class awards for WCOM™ application.